Ultimate Guide to Formwork Systems
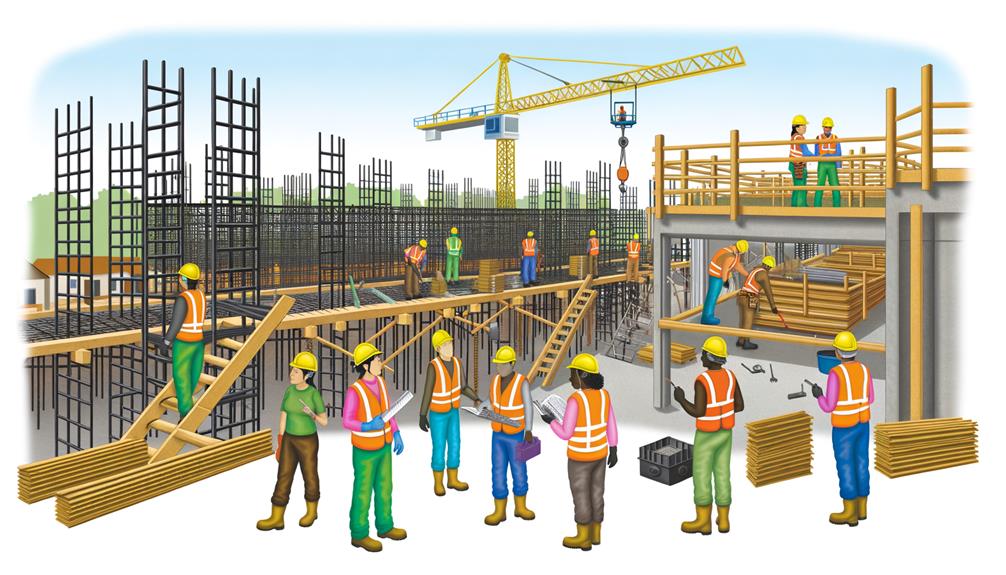
Formwork systems are essential in shaping and supporting concrete in construction. They vary in material, from plywood and steel to insulated styles, each with distinct pros and cons. Choosing the right formwork affects a project's success, aesthetics, and structural strength. It's a delicate balancing act that considers durability, flexibility, and cost-efficiency. Then, there's the creation of formworks for beams and columns. Modern systems offer precision, alignment, and adaptability specific to a project's needs. Venturing further gives a clearer understanding of why these systems are essential for structural integrity.
Understanding Formwork Systems
To fully comprehend the complex world of formwork systems, we must first grasp that they're temporary structures utilized in construction to provide both support and shape to concrete, ensuring the strength, stability, and the desired form of elements such as beams and columns. This fundamental understanding liberates us from the shackles of confusion, illuminating the very essence of these indispensable systems in the construction industry.
The intricate design of formwork systems is based on the principle of temporary support. They're built to bear the weight and withstand the pressure of still-wet, unset concrete, holding it in place until it solidifies and gains sufficient strength to stand on its own. However, their role isn't merely supportive. They also define the shape of the concrete elements, providing a mold in which the concrete is poured and formed.
We've got two main types of formwork systems: stay-in-place and permanent insulated formwork. Stay-in-place formwork is designed to remain in situ even after the concrete has hardened, offering additional reinforcement and long-term structural support. This type is particularly beneficial for structures that require increased resilience, such as piers and columns.
On the other hand, permanent insulated formwork combines the dual functions of molding and insulating the concrete. This innovative system enhances both the energy efficiency and structural integrity of the resulting structure, ensuring that it's not just strong and stable, but also eco-friendly.
In essence, understanding formwork systems is about recognizing their dual role: supporting and shaping the concrete, while also providing added benefits that depend on the specific type of formwork chosen.
Formwork Materials and Selection
Diving into the realm of formwork materials and selection, we encounter a variety of options, each with its distinct strengths and drawbacks, influencing the strength, aesthetics, and overall success of our construction projects. Exploring this landscape, it's crucial to determine the ideal material for each unique project, taking into account considerations such as durability, flexibility, aesthetics, and cost-efficiency.
Plywood surfaces as a popular choice, thanks to its durability, smooth finish, and ability to enhance the strength of concrete structures. However, steel and aluminum formwork, although more costly, offer superior strength and resilience, making them ideal for larger projects. They also provide an exceptionally smooth concrete finish, contributing to visually appealing structures.
Conversely, plastic formwork offers a lightweight alternative, perfect for smaller projects with repetitive formwork needs, with the added advantage of being easy to clean. Nevertheless, durability could be a concern over extended use.
Fabric formwork is a game-changer, offering flexibility and opportunities for creative design elements in construction projects. This innovative material allows for unique, non-linear design possibilities, freeing us from the constraints of traditional formwork.
Wood, while versatile and lightweight, may not be the top choice for complex pours or large-scale projects. Its limitations in efficiency and flexibility could impede project progression and outcome.
Hence, when choosing formwork materials, we must consider the project's scale, complexity, design aspirations, and budget constraints. The selection should free us from limitations, opening new horizons in construction possibilities. Our goal is to maximize efficiency, durability, and aesthetic appeal while balancing cost-effectiveness.
Formwork for Beams and Columns
When it comes to formwork for beams and columns, it's essential to understand that these structures play a pivotal role in ensuring the strength, shape, and stability of these key structural elements during the construction process. They're literally indispensable, supporting wet and dry concrete alike, and are central to the success of any construction project.
Different types of formwork materials are chosen for beams and columns based on project requirements. This variety allows us to tailor our approach to meet the specific needs and specifications of every project. From the lightweight and flexible, to the robust and rigid, we've got a formwork solution that fits.
Formwork systems for beams and columns are more than just practical; they're innovative. We're not just talking about a simple mold here, but a dynamic system that can adapt to the unique challenges of each build. This adaptability frees us from the constraints of traditional construction methods, allowing us to push the boundaries of what's possible.
Moreover, the formwork structures surrounding beams and columns are essential components of construction projects. They're not just there to hold things in place, but to make sure that every inch of the structure is perfectly aligned and secure. It's about precision, not just practicality.
Building Beam and Column Formwork
In building beam and column formwork, we utilize a variety of materials like timber, plywood, steel, and aluminum to create robust structures that not only shape but also support the horizontal and vertical concrete elements integral to construction sites. These materials, meticulously chosen for their durability and sturdiness, provide the necessary backing to guarantee the successful casting of concrete structures.
Formwork systems for beams differ from those for columns, considering the varying structural requirements and loads. Each system is uniquely designed to withstand the pressure exerted by the wet concrete, and to hold its shape until it hardens and cures. The materials we use must be not just durable, but also resilient enough to endure the weight and pressure of the concrete.
Fast-Form column formwork emerges as a lightweight, efficient, and durable solution for constructing columns. Its innovative design yields high-quality surface finishes, adding to the aesthetic appeal of the completed structure. We appreciate that it's not all about appearances, though. The Fast-Form system also prioritizes safety, with features like lightweight components, integral concreting platforms, and straightforward assembly procedures.
Embracing these systems can offer a certain liberation, freeing us from traditional formwork methods that are often labor-intensive and time-consuming. Through the use of innovative formwork systems like Fast-Form, we can increase efficiency, reduce manual labor, and guarantee the creation of superior-quality concrete structures. In the end, the buildings we raise aren't just aesthetically pleasing, but reliable, safe, and built to last.
Beam Formwork Installation
Setting up beam formwork, a process involving the creation of temporary structures to support and shape concrete beams, is a critical step in construction, demanding precision alignment, robust bracing systems, and meticulous attention to detail. The stakes are high; any misalignment could jeopardize the stability and safety of the entire structure.
We begin by carefully aligning the formwork, guaranteeing it meets design specifications. The usage of modern digital tools like laser levels and digital theodolites enhances accuracy, liberating us from reliance on traditional, less precise methods. This guarantees that the resultant concrete beams are of the exact dimension and position as envisaged in the architectural plan.
Next, we establish a robust bracing and support system. This needs to be sturdy enough to withstand the weight of wet concrete, which we pour into the formwork. Shoring jacks and posts, often made from steel or aluminum, provide this essential support. They're adjustable and can be fine-tuned to maintain alignment as the concrete sets.
The design of the beam formwork varies based on the beam's size, shape, and load requirements. We employ cutting-edge technologies that allow for customization, ensuring the formwork accommodates these variables. This innovative approach reduces waste and increases efficiency.
Attention to detail is paramount throughout the process. We painstakingly check and double-check every aspect, from alignment to bracing strength. This meticulousness isn't just about achieving high-quality outcomes; it's about safeguarding the safety of all involved.
Introduction to Column Formwork
Moving on to column formwork, we explore an essential component that shapes and supports vertical concrete elements, ensuring their correct dimensions, alignment, and finish during construction. This critical facet of construction liberates architects and engineers to design diverse structures with a variety of column sizes and shapes, all made possible by the flexibility of formwork systems.
To better understand the scope and utility of column formwork, let's dive into a comparison table:
Key Aspects | Importance | Benefits |
---|---|---|
Dimensional Accuracy | Guarantees columns adhere strictly to design blueprint | Enhances structural integrity |
Alignment and Finish | Ensures straight and well-finished columns | Boosts aesthetics and durability |
Safety Features | Facilitates easy assembly with minimal tools; includes integrated concreting platforms with guard rails | Enhances worker safety and productivity |
Column formwork's versatility is its greatest strength. Different formwork systems cater to a diverse range of column dimensions and shapes. This adaptability allows for customization and facilitates the creation of unique architectural designs without compromising on the structural integrity, safety, or efficiency of the construction process.
We must also consider the safety features inherent in column formwork. An easy assembly process requiring minimal tools can notably reduce the risk of accidents on site, while integrated concreting platforms with guard rails offer additional protection for workers during construction.
Fast-Form Column Formwork Advancements
Turning our attention now to advancements in Fast-Form Column Formwork, we note it's not only the lightest system on the market but also offers a unique fixing system that bolts directly onto slabs, revolutionizing construction speed and efficiency. This innovative design reduces the need for highly skilled labour, liberating companies from labor-intensive processes and high operational costs.
The Fast-Form system also integrates safety features in its design, including integral concreting platforms with guard rails and the capability to work from just one side. This thoughtful inclusion not only enhances worker protection but also contributes to the overall productivity of the project, allowing for more streamlined operations.
In terms of durability, Fast-Form Column Formwork exceeds expectations. Components are designed to last over 25 years, an impressive lifespan that again contributes to cost-efficiency. It's also an environmentally conscious choice, being made from 100% fully recyclable materials.
But the Fast-Form system's efficiency and ease of use truly shine through in its assembly process. It allows for precision adjustments on-site, an invaluable feature for ensuring the accuracy and quality of construction works. Additionally, the option to fit formliners for customized finishes adds flexibility to the system, making it adaptable to a wide range of project requirements.
Formwork Hire Services Overview
Venturing into the domain of formwork hire services, Fast-Form Systems introduces a cost-effective and safety-enhancing solution for construction projects, providing high-quality equipment for hire. This option liberates you from the hefty investment and repeated maintenance costs associated with buying formwork, while still allowing access to premium equipment.
Here are three key benefits of our formwork hire services:
- Risk Minimization: Our equipment adheres to strict safety standards. It's designed to reduce the likelihood of accidents on site, not only protecting your workforce but also potentially reducing your liability.
- Maintenance Freedom: Once you're done with a project, there's no need to worry about storing or maintaining the equipment. Simply return it, and we'll take care of the rest.
- Cost-Effectiveness: By hiring instead of buying, you can manage your costs more effectively, paying only for the period you need the equipment. This can greatly reduce your project expenses.
Our formwork hire service isn't just about equipment lending, it's about understanding your project needs and supplying the best solution that meets those needs. We offer competitive rates, ensuring you get value for your money while maintaining the quality of your construction.
In essence, we're providing a liberating way to handle your formwork needs. You're freed from the burden of ownership, while still enjoying the benefits of using premium equipment. With us, you get the best of both worlds, making it a win-win situation for your construction projects.
Decoding Formwork Specifications
Delving into the intricacies of formwork specifications, it's crucial to highlight that they're specifically tailored based on concrete type, pouring temperature, pressure build-up requirements, and the particular job's structural design considerations. These elements directly influence the formwork's capacity and durability, further determining the quality of the finished structure.
Cracking the code of these specifications, we must underscore the importance of a quality finish. It's not just about aesthetics; it greatly impacts the concrete's interaction with the formwork and eventual longevity. Temperature plays a critical role in this process. Precise specifications ensure the concrete pour happens at the best temperature, mitigating the risk of cracks or unequal pressure distribution.
Strength is another key aspect of these specifications. The formwork must withstand the pressure of concrete, including the live loads during construction. Hence, the design and material of the formwork are meticulously chosen to resist these stresses, ensuring the safety of the workforce and the structure.
Deciphering formwork specifications further, we find that structural calculations are integral to formwork safety and stability. These calculations, based on the job's unique requirements and structural design considerations, determine the positioning, load-bearing capacity and support system for the formwork.
To sum it up, decoding formwork specifications is akin to understanding the blueprint for a successful construction project. It's a detailed, innovative process tailored to each job's requirements, ensuring safety, efficiency, and quality. So, let's embrace this understanding, freeing us from potential construction pitfalls and paving the way for engineering excellence.
Benefits of Hiring Formwork
Entering the domain of formwork hire, it's evident that it offers tangible benefits such as enhanced safety, minimal upkeep, access to premium equipment, cost-effectiveness, and overall efficiency in construction projects. We've dug deep into the details, and here's what we've unearthed.
Firstly, safety is a paramount concern on any construction site. Hiring formwork markedly lowers the risks associated with onsite accidents. You're provided with top-of-the-line, well-maintained equipment which reduces the likelihood of mishaps.
Secondly, the convenience of formwork hire is unparalleled. The maintenance and upkeep of the equipment are practically zero, as once the task is complete, the equipment is returned. No worries about storage, no headaches about maintenance!
Thirdly, cost-effectiveness is a major draw for many. Competitive hire rates mean that you get access to high-quality equipment without breaking the bank.
There's also a hidden gem that we've discovered. Formwork hire offers an overall increase in efficiency. It's a straightforward process – you get the right equipment when you need it, use it, and return it. No downtime waiting for equipment to arrive, no time wasted on equipment maintenance.
In short, formwork hire is a liberating choice that takes off the burdens of equipment purchase, maintenance, and storage. It's a cost-effective, safety-enhancing, efficiency-boosting option that's hard to beat. So, why not consider this option for your next construction project? We're confident that it's a decision you won't regret.
Falsework Vs. Formwork
Now that we've explored the benefits of formwork hire, it's time to delve into the comparison between falsework and formwork, two vital elements in the construction industry.
Falsework and formwork serve distinct, yet interconnected roles, creating a symbiotic relationship. You might think of falsework as the supportive backbone, holding temporary structures securely, including formwork, until the permanent structure can stand on its own. This pivotal role guarantees safety, stability, and prevents premature collapse, which is why it's often used with steel beams, bridge spans, and prefabricated concrete elements.
On the other hand, formwork is the mold that shapes and contains the wet concrete until it can support itself. It's a high-risk task, involving the operation of heavy machinery like cranes and often requiring work at heights. Its significance can't be overstated as it provides the exact shape and design of the structure.
It's evident that both falsework and formwork aren't only critical but inseparable in the construction industry. The successful operation of one is dependent on the other. Choosing the right type and quality of both is non-negotiable.
We've also noted that while both entail risk, formwork presents a higher level due to the complexities involved. Therefore, hiring experienced professionals and investing in quality materials for both falsework and formwork is crucial.
In essence, falsework is the silent guardian, while formwork is the creative director in this construction play. Each has a unique role, but together they create a harmonious, safe, and efficient construction process.
Engineering of Scaffold and Formwork
Expanding on the significance of falsework and formwork in construction, let's redirect our attention to the precise engineering of scaffold and formwork systems, a vital aspect that guarantees safety, efficiency, and successful project completion. Scaffold and formwork engineering is a specialized discipline that requires a deep understanding of structural analysis, material strength, and load capacity. It's about designing temporary structures that not only hold up but also optimize construction operations.
- Load Capacity: This is the maximum weight the scaffold and formwork system can safely support. It's determined by factors such as the strength of the materials used, the design of the structures, and the nature of the load itself. We don't merely aim for survival under maximum load; we aim for resilience and steadiness.
- Material Strength: The strength of the materials used plays a significant role in the overall integrity of the scaffold and formwork systems. The right choice of material can make the difference between a stable structure and a potential collapse. We're not just choosing materials; we're forging a foundation of trust and dependability.
- Regulatory Compliance: The engineering of scaffold and formwork systems must adhere to safety regulations and industry standards. It's not just about ticking boxes; it's about upholding the highest standards of safety and ensuring the wellbeing of every single worker on site.
Formwork Safety and Risk Mitigation
Exploring the maze of formwork safety and risk mitigation, it's evident that the design of the formwork plays a vital role in ensuring worker safety by preserving structural integrity during concrete pouring. This means that a slipshod design isn't an option; we need a robust approach that factors in potential risks and follows engineering standards.
Imagine formwork as a protective shell, safeguarding workers from the pitfalls of the construction process. It's a safety net, but one that's only as strong as its weakest link. This is where falsework comes into play, providing support for temporary structures until their permanent counterparts can stand alone. It's an essential player in our risk mitigation strategy, reducing hazards during the construction phase.
However, we can't simply rely on design and falsework; there's more to the safety equation. Certified engineer inspections and compliance with standards like AS 3610 are the keystone of our safety fortress. This isn't a box-ticking exercise; it's a meticulous process that ensures every inch of our formwork is up to scratch.
Maintenance and Inspection of Formwork
Delving deep into the domain of formwork, regular inspections and diligent maintenance become our lifeline, ensuring these temporary structures can bear the weight of construction activities while meeting stringent safety standards. We must recognize the pivotal role played by certified engineers in performing these regular checks, making sure our formwork structures comply with safety standards. This periodic scrutiny guards against potential hazards, helps to avert accidents, and maintains the structural integrity of our worksites.
Maintenance of formwork is a holistic process that involves more than just a cursory glance. Instead, it involves:
- Checking for wear and tear, which if neglected, could compromise the structural stability of the formwork.
- Ensuring proper alignment, which is crucial to the correct distribution of loads and the overall stability of the structure.
- Addressing any damage promptly and thoroughly, to prevent small issues from escalating into major problems.
Compliance with AS 3610 standards isn't just an option; it's a necessity. These standards serve as our compass, guiding our construction activities and ensuring safety measures are met. A Formwork Structural Certificate isn't simply a piece of paper; it's a proof of the safety and stability of the formwork systems we employ.
Frequently Asked Questions
What Are the 4 Principles of Good Formwork?
We believe that good formwork revolves around four key principles.
To begin with, it must support both wet and dry concrete securely.
Next, proper bracing is crucial to maintain its shape and structural integrity.
Third, it must have leak-proof joints to prevent concrete leakage and guarantee a smooth finish.
What Are the Basics of Formwork?
We're diving into the basics of formwork, the temporary molds used in construction. These molds shape concrete elements like beams and columns, ensuring their strength and stability.
The materials used can vary, from timber and plywood, to steel, aluminum, and plastic. The type of formwork chosen depends on the project's requirements and design complexity, with different systems used for bases, walls, columns, and slabs.
That's the foundation of understanding formwork!
What Is the Most Durable Type of Formwork?
We've found that steel formwork is the most durable. Its strength and longevity surpass others, withstanding wear and tear like a champ. It's reusable too, making it cost-effective and eco-friendly.
But don't discount aluminum formwork. It's lighter yet matches steel in durability when maintained well. Ideal for high rises and heavy-duty projects, steel formwork guarantees consistent quality and structural integrity. It's a true game-changer in concrete construction.
What Are the Three Main Principles That Govern the Design and Construction of Formwork?
We've identified three key principles that drive formwork design and construction.
Firstly, load-bearing capacity is essential for supporting both wet and dry concrete effectively.
Secondly, structural integrity is crucial for preserving formwork's shape during concrete pouring.
Lastly, leak-proof joints are necessary to prevent concrete leakage for a smooth, uniform finish.
Following these principles guarantees reliable construction of beams, columns, and other concrete structures.
Conclusion
In wrapping up, we've examined formwork systems, their materials, and selection process.
We've explored beam and column formwork construction, the distinction between falsework and formwork, and the engineering aspect.
We've also emphasized the importance of safety measures, risk mitigation, and regular maintenance and inspection.
Ultimately, understanding these elements is crucial in ensuring a successful, efficient, and safe construction project.
Always remember, a well-managed formwork system can be a game-changer in your construction endeavors.