Formwork Tips and Tricks for Beginners
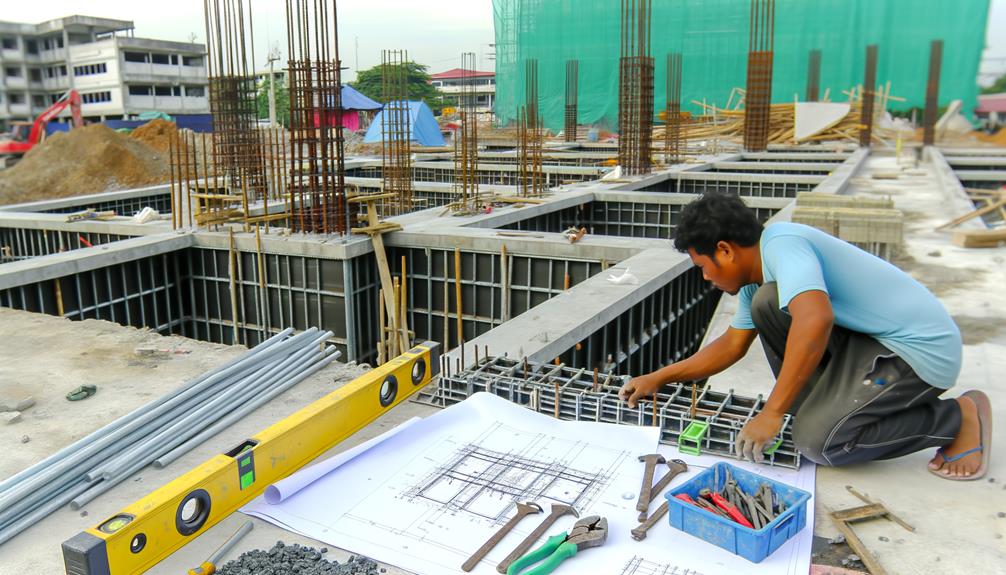
We're sharing formwork basics to help beginners. First, understand formwork is a temporary mould for concrete. Choosing the right material, such as timber or plywood, is essential, as is mastering the skill of formwork carpentry. Safely support the weight of the structure, guarding against collapse. Create efficient designs with load-bearing capacity. Remember, maintenance is key for a robust formwork. Regular inspections, cleaning, and storage will guarantee your formwork stays in prime condition. Once you grasp these foundational concepts, your journey into advanced strategies and troubleshooting typical formwork problems awaits. Ready to further sharpen your skills?
Understanding Formwork Basics
Let's explore the fundamentals of formwork, a temporary mould skillfully constructed to shape wet concrete until it hardens, a critical process that requires an understanding of materials, structural integrity, and hydrostatic pressure. This knowledge isn't just theoretical, it's practical, and it's vital to anyone seeking liberation through the art of construction.
Formwork can be crafted from various materials, including timber, plywood, or tie wire. Sometimes, even sapling trees are used in the process. We don't simply pick these materials randomly but choose them based on the specific needs of the project. The artisanal skill involved in formwork carpentry ensures this temporary structure can bear the weight of the wet concrete, the reinforcement steel, and endure environmental conditions until the concrete sets.
Proper propping is a non-negotiable aspect of formwork. Suspended slabs, for example, require appropriate support to handle the weight of the reinforcement steel and the wet concrete. Without it, the structural integrity of the entire construction is at risk. We need to be mindful of this in every step of our work.
Perhaps the most crucial aspect of formwork is understanding hydrostatic pressure. This pressure can potentially cause a formwork to collapse, leading to costly delays and potential safety hazards. We must be skilled at calculating and managing this pressure to guarantee the secure and successful shaping of concrete structures.
Importance of Formwork in Construction
Having explored the basics of formwork, we can now appreciate its fundamental role in construction, serving as the backbone in shaping wet concrete into the desired structures like slabs, walls, and columns. It's much more than a temporary scaffold; it's the invisible hand that guides the concrete, ensuring it perfectly embodies the architectural vision.
Formwork provides the essential support that wet concrete needs during the setting process. It's akin to a guardian angel, ensuring the structural integrity and safety of concrete elements both during and after the pouring process. Without formwork, the wet concrete would lose its shape, compromising the stability and safety of the structure. It's this pivotal role that underscores the value of formwork in construction, a role that can't be overstated.
Moreover, formwork is the magic tool that brings architects' and engineers' designs to life. It allows for customization of concrete shapes and sizes, liberating designers from the constraints of traditional construction methods. With formwork, the only limit is one's imagination.
Understanding the importance of formwork helps beginners grasp its pivotal role in successful construction projects. It's the unsung hero of construction, silently shaping our world one structure at a time. Without it, our skylines would be notably less impressive.
Choosing the Right Formwork Material
Browsing through the myriad of formwork materials available on the market, we realize that each offers unique benefits suited to different construction needs. Understanding these materials and their particular advantages is the key to picking the right one for your project.
Timber formwork, for instance, is a cost-effective solution. It's easily customizable, making it a favorite among constructors looking for flexibility. On the other hand, plywood formwork is your go-to when durability is paramount. It's a common choice for various concrete structures due to its robustness.
Aluminum formwork stands out for its lightweight nature and reusability. This makes it a practical choice for repetitive construction designs where frequent formwork removal and repositioning are required. If you're dealing with heavy-duty applications, steel formwork is your best bet. It offers high strength and durability that can withstand significant pressures.
Lastly, plastic formwork is worth considering for small-scale concrete works. It's lightweight, easy to handle, and can be quickly set up. Despite its lightness, it's sturdy enough to hold the concrete until it hardens.
Efficient Formwork Design Strategies
Exploring the realm of effective formwork design strategies, it's crucial to prioritize load-bearing capacity and structural requirements, guaranteeing a sturdy and secure construction. We must comprehend that the strength of the formwork directly impacts the stability of the structure it molds. Hence, it's paramount to adopt a meticulous approach in design and execution, leaving no room for compromises.
We can't overlook the role of technology in formwork design. Leveraging the power of specialized formwork design software, we can perform precise calculations and achieve peak efficiency. These tools not only provide accurate results but also allow us to foresee potential issues, thereby promoting proactive issue-solving.
Safety, without a doubt, holds a central place in our design strategy. We should integrate safety features such as guardrails and fall protection systems into our formwork designs. This not only protects our workforce but also ensures conformity with regulatory standards.
However, efficiency isn't solely about technicalities and safety. It's also about sustainability and cost-effectiveness. We advocate for the use of reusable formwork systems, which can markedly reduce costs and environmental impact.
Lastly, we shouldn't hesitate to seek guidance from experienced formwork designers. Their invaluable insights can guide us towards successful project outcomes. Essentially, efficient formwork design strategies are a blend of technical expertise, practical wisdom, and constant adaptation to the evolving construction landscape. It's a journey of liberation, freeing us from traditional constraints, and enabling us to create innovative, sustainable, and cost-effective construction solutions.
Types of Formwork Systems
Diving into the different types of formwork systems, we find an array of options, each with its unique features and benefits, designed to meet specific construction needs. Traditional systems, for instance, commonly utilize plywood due to its versatility and widespread availability. It's a tried and true choice that offers a balance of strength and flexibility, making it a reliable pick for various projects.
Then we've modular formwork systems, typically made of lightweight aluminum or steel. These systems are a proof of the evolution of formwork, offering ease of handling and assembly, thereby liberating construction workers from the constraints of heavier materials. However, it's not all about weight; safety considerations are paramount when selecting formwork systems. The right choice can provide a protective shield to workers from potential hazards.
An integral part of these systems is the standard formwork frames and bracing. These elements secure the stability and safety of the formwork system, a fundamental aspect that can't be overlooked. Let's not forget that modular systems, while lighter, require proper bracing and support to maintain structural integrity during concrete pouring. Therefore, these systems present a delicate balance of lightweight materials and robust support mechanisms.
Erecting Formwork: Step-by-Step
After understanding the types and components of formwork systems, let's map out the process of erecting formwork, breaking it down into manageable steps. This process can seem challenging, but with our guidance, you'll be able to navigate it with ease.
The first step is to mark the layout of the formwork on the ground. We use chalk lines and stakes for this purpose, making sure that the formwork will be placed accurately. This is a pivotal stage because it sets the foundation for the rest of the work.
Next, we install the formwork panels or boards. They must be securely fastened, with adequate bracing and supports to prevent them from shifting during the concrete pouring phase. It's here that we start to see our vision take shape.
Now we focus on aligning the formwork. The importance of this step can't be overstated. The formwork must be leveled and aligned according to the design specifications and measurements to guarantee a structurally sound result.
Adjustable formwork braces are our secret weapon to fine-tune the alignment and verticality of the formwork. These tools give us the flexibility to adjust the formwork as needed before pouring the concrete, making certain our structure will be robust and durable.
Lastly, we regularly check and adjust the formwork for any deviations or misalignments. This vigilance maintains the integrity of the concrete structure, making sure our work is nothing short of perfect.
This step-by-step method liberates us from the complexities of the process, allowing us to focus on the task at hand and build with confidence. It's a foolproof process that guarantees a flawless formwork setup.
Safety Measures During Formwork Setup
In the domain of formwork setup, nothing is more vital than implementing strict safety measures to safeguard our team from potential mishaps. It's essential we prioritize proper training on formwork safety measures. This isn't merely a bureaucratic box to tick; it's a vital tool in our arsenal to prevent accidents during setup.
We must also make sure that all our workers are equipped with personal protective equipment (PPE), including helmets, gloves, and safety boots. Such gear isn't optional – it's a necessity. Each piece plays an important role, acting as the first line of defense against potential injuries.
To strengthen our safety efforts, we regularly conduct safety briefings. This isn't just about repeating the same old safety talk. Instead, we emphasize the importance of following established safety protocols, making each worker a crucial link in our safety chain. It's about fostering a culture of safety consciousness, where each team member is vigilant, not just for their safety, but for their colleagues as well.
In our quest to prevent injuries, we've implemented robust fall protection systems. Guardrails and safety nets are more than mere equipment; they're life-saving tools that help us maintain a safe working environment.
Lastly, we acknowledge the importance of maintaining our formwork equipment. Regular inspections help us identify any potential hazards or defects that could compromise safety. It's not just about making our work easier; it's about ensuring the wellbeing of our team.
Wall and Column Formwork Techniques
When addressing wall and column formwork, it's vital we consider techniques that not only improve our efficiency but also strengthen our dedication to safety. Wall formwork needs to be strong to withstand wind loads and provide the necessary support for concrete placement. Column formwork, on the other hand, requires strategic positioning of clamps, through bolts, and secure nailing to resist the hydrostatic pressure.
To guarantee the stability and integrity of wall and column formwork systems, proper bracing design by competent personnel is non-negotiable. It's also essential to provide lateral support with braces to prevent premature removal of wall formwork and ensure safety during construction.
To help you better understand these techniques, let's outline four key points:
- Design wall formwork to handle wind loads and concrete placement support. This involves careful material selection and structural design.
- Apply strategic placement of column formwork components. Install clamps, through bolts, and nails to resist hydrostatic pressure.
- Implement a proper bracing design. This requires the expertise of competent personnel to ensure stability and integrity.
- Use lateral braces for support to prevent premature removal of wall formwork. This step is essential for safety during construction.
Lastly, consider using precast columns, beams, and modular systems. These can greatly enhance both safety measures and efficiency in wall and column formwork construction. By incorporating these techniques, we're not only optimizing our work but also freeing ourselves from unnecessary risks and inefficiencies. It's all about working smarter, not harder.
Formwork for Suspended Slabs
Shifting our focus to formwork for suspended slabs, it's important to emphasize that proper propping is essential to support the weight of wet concrete and reinforcement steel. This isn't just a technicality—it's a critical safeguard. Over-propping trumps under-propping any day when it comes to ensuring structural stability and preventing accidents.
We can't overstate the importance of adequate support elements like bracing, struts, and tie bolts in successful formwork of suspended slabs. They're not just add-ons; they're essential components that warrant careful selection and meticulous placement. The wrong choice or incorrect positioning can compromise the entire structure.
Beyond this, understanding the impact of hydrostatic pressure in formwork is key. It's not just a theoretical concept to be puzzled over in textbooks. It's a real-world force that can make or break your formwork for suspended slabs. A sound grasp of how it works can enable you to support suspended slabs effectively, and sidestep potential pitfalls.
Finally, never underestimate the power of careful planning and adherence to safety guidelines. They're your first line of defense against mishaps and accidents during formwork construction. Remember, we're not just constructing formwork—we're crafting safety.
In the quest for formwork mastery, it's not just about gathering knowledge. It's about applying that knowledge intelligently, creatively, and, above all, safely. It's about liberation—liberation from fear, from uncertainty, and from the constraints of the conventional. So, let's immerse ourselves, embrace the challenge, and revolutionize our approach to formwork for suspended slabs.
Ensuring Stability of Formwork Structures
In our efforts to transform our approach to formwork, let's shift our focus to preserving the stability of these structures, a crucial aspect that guarantees both safety and structural integrity. The stability of formwork structures is non-negotiable, and it requires an analytical and precise application of certain techniques.
- Proper Bracing: It's critical to brace our formwork structures with both horizontal and diagonal supports. This ensures the formwork remains steady during the concrete pouring and curing processes.
- Secure Pegging of Diagonal Braces: Our diagonal braces must be pegged securely, at least six inches deep into the ground. This prevents any shifting of the formwork under the weight of the concrete.
- Use of Suitable Materials: To prevent the concrete from sticking and destabilizing the formwork, we must use the right facing materials on the inside of the formwork.
- Application of Release Agents: Apply a release agent on the formwork surfaces. This reduces the risk of concrete sticking to the formwork and helps maintain its stability.
Formwork Removal: Best Practices
Proceeding to the next pivotal step in our formwork journey, let's explore the best practices for formwork removal. This is a process that requires finesse, understanding, and patience. The goal is to maintain the structural integrity of the concrete element while making sure our formwork components are intact and reusable.
Firstly, let's not rush into this process. Waiting for the concrete to fully cure before removing the formwork is essential. This patience helps to prevent any potential damage to the structure. As we all know, concrete isn't forgiving to mistakes! So, let's take our time to allow the concrete to reach its maximum strength.
Next, gently tap and loosen the formwork components using a rubber mallet. The goal is to remove the formwork without causing any harm to the structure or the formwork itself. This method isn't only efficient but also effective in preserving both our formwork and the structure.
Applying a release agent on the formwork is another best practice. This helps to prevent the concrete from sticking to the formwork, making the removal easier. It's a simple yet significant step that can save us a lot of time and effort.
Lastly, it's important to follow a systematic approach to formwork removal. This approach ensures all edges and surfaces remain unscathed during the removal process. Careful planning and execution are key to achieving this.
Dealing With Common Formwork Problems
While we've perfected the art of formwork removal, we can't ignore the common issues that often affect the formwork process, like misalignment, inadequate propping, and insufficient bracing among others. These challenges can potentially lead to a compromised structural integrity, causing project delays and presenting safety risks.
Let's explore the core of these common formwork problems and how we can overcome them, freeing ourselves from unnecessary stress and costly errors.
- Misalignment: This occurs when the formwork components aren't precisely aligned. It could distort the concrete structure, leading to aesthetic and structural issues. We can prevent this by ensuring precise measurements and careful assembly.
- Adequate Support: Formwork requires proper support to bear the weight of wet concrete. Inadequate propping can cause formwork to collapse under the pressure. By using robust supports and ensuring they're evenly distributed, we can avoid this issue.
- Sufficient Bracing: Bracing offers stability to formwork, preventing it from shifting or toppling over. We must ensure that braces are installed at correct angles and securely fastened.
- Quality Material Choices: The quality of materials utilized in formwork directly impacts its performance. Opting for low-quality materials can result in formwork failure. We should always choose materials that meet strength, durability, and safety standards.
Maintenance and Care for Your Formwork
Shifting our focus, let's explore the ins and outs of maintaining and caring for your formwork to guarantee it serves you well over the long haul. Formwork, when cared for properly, can last for numerous projects, saving us time, energy, and most importantly, money. But how do we make sure it stands the test of time?
Firstly, regular inspections are key. We can't fix what we don't see, right? Look out for damage, such as cracks, splits, or warping. These can compromise the safety and efficiency of our formwork, and we certainly don't want that.
Cleaning is another essential step. After each use, make sure to clean your formwork to prevent concrete buildup. This residue can affect the quality of your future pours, and we all know quality is paramount.
Now, onto storage. Where and how we store our formwork is just as important. A dry and well-ventilated area is our best bet to prevent moisture damage and extend the lifespan of our formwork.
Before each use, applying release agents is a must. This will ease the removal of the formwork and prevent concrete from sticking. Sounds simple, but it makes a world of difference.
Lastly, keep a detailed maintenance log. Tracking repairs, cleaning schedules, and the overall condition of the formwork will ensure peak performance. A well-maintained formwork is a well-performing formwork, and that's our ultimate goal.
In essence, maintaining and caring for your formwork isn't just a recommendation, but a necessity. It's our path to liberation from needless costs, wasted time, and subpar results. So let's roll up our sleeves and make our formwork last.
Advanced Formwork Tips
Having understood the importance of maintaining our formwork, let's now elevate our construction prowess by exploring some advanced formwork tips that can transform our approach to formwork construction. This journey will take us through a world of innovative materials, digital tools, and safety measures, all aimed at making our work more efficient, precise, and safer.
- Embrace Modular Systems: Advanced formwork techniques often involve using steel or aluminum modular systems. These aren't only durable but also increase efficiency. We're no longer bound by the limitations of traditional wood formwork.
- Incorporate Digital Tools: Precision is key in advanced formwork construction. Incorporating digital tools and Building Information Modeling (BIM) software can enhance our accuracy to a great extent. These tools liberate us from guesswork, allowing us to execute our plans with mathematical precision.
- Prioritize Safety: Advanced formwork solutions prioritize safety by implementing sophisticated bracing and support systems. These systems guarantee the formwork stays in place, protecting us and our work from potential hazards.
- Utilize Lightweight Materials: The use of lightweight materials in advanced formwork designs improves portability and ease of installation. These materials, such as fibreglass, make formwork assembly and disassembly a breeze.
Remember though, advanced formwork methods often require specialized training to guarantee proper assembly and structural integrity. So, don't shy away from investing in learning. It's through this mastery that we can truly liberate ourselves from the constraints of traditional methods, and usher in a new era of advanced, efficient, and safe formwork construction.
Learning From Formwork Mistakes
In spite of our best efforts, mistakes in formwork construction can occur, and it's through analyzing these errors that we can identify areas for improvement and prevent future mishaps. We must learn to embrace these mistakes, not as failures, but as opportunities to refine our craft and strengthen our skills.
Analyzing formwork mistakes allows us to understand where we've gone wrong and where improvements can be made. It's important that we document these errors and their consequences, ensuring we don't repeat the same mistakes in future projects. This process of self-evaluation and reflection is essential in our journey towards mastering formwork construction.
Guidance from experienced professionals is invaluable in preventing common formwork errors. Their expertise and insights can shed light on best practices, helping us avoid pitfalls and enhancing our understanding of the intricacies of formwork construction. We shouldn't shy away from seeking their advice; their wisdom can set us on the right path and accelerate our learning process.
Quality control measures are critical in catching mistakes early and ensuring our formwork is properly constructed. Such measures serve as our safety net, saving us time and resources in the long run. They're not just about catching errors, they're about ensuring we can deliver the best possible results in all our projects.
Frequently Asked Questions
What Are the Basics of Formwork?
We're discussing the fundamentals of formwork here. It's the temporary structure we construct to hold wet concrete until it hardens.
We utilize materials like timber, plywood, and tie wire, depending on the job. Our task demands skill and knowledge to guarantee the eventual concrete structure has integrity.
We're also obligated by local codes and safety measures. It's a intricate, but rewarding process that forms the basis of our construction work.
What Are Four Principles of Good Formwork?
We've identified four principles of good formwork:
rigidity,
watertightness,
proper bracing,
and adherence to local codes.
These principles guarantee structural integrity and safety. Consulting with experienced designers is vital to achieving these standards.
When we follow these principles, we're not just building, we're creating art that stands the test of time. It's more than construction; it's our contribution to shaping a resilient and beautiful built environment.
How to Learn Formwork?
We're advocates for learning formwork through hands-on experience. It's crucial to grasp the basics, understand different formwork systems, and master safety measures.
We'd recommend assisting seasoned carpenters on site, absorbing their knowledge and techniques. It's through this practical experience that we'll truly learn.
How Long Should You Leave Shuttering on Concrete?
We'd recommend leaving shuttering on concrete for at least 24 to 48 hours. This allows the concrete to cure and gain strength. However, factors such as weather conditions and the specific mix design can influence this duration.
It's vital to heed expert advice for the best timing. Removing shuttering prematurely can cause defects and weaken the structure. So, take care and make sure we're giving our concrete the best chance at durability and resilience.
Conclusion
We've journeyed through the basics of formwork, its importance, right material selection, and efficient design strategies.
We've explored various formwork systems, tackled common problems, and learned maintenance tips.
The advanced tips and learning from mistakes sections capped our knowledge.
As we continue to innovate, let's apply these formwork tips and tricks, ensuring we're building structures that aren't only strong and safe but also cost-effective.
Remember, success lies in continuous learning and improvement.