Formwork Material Selection: Wood Vs. Steel Vs. Aluminum
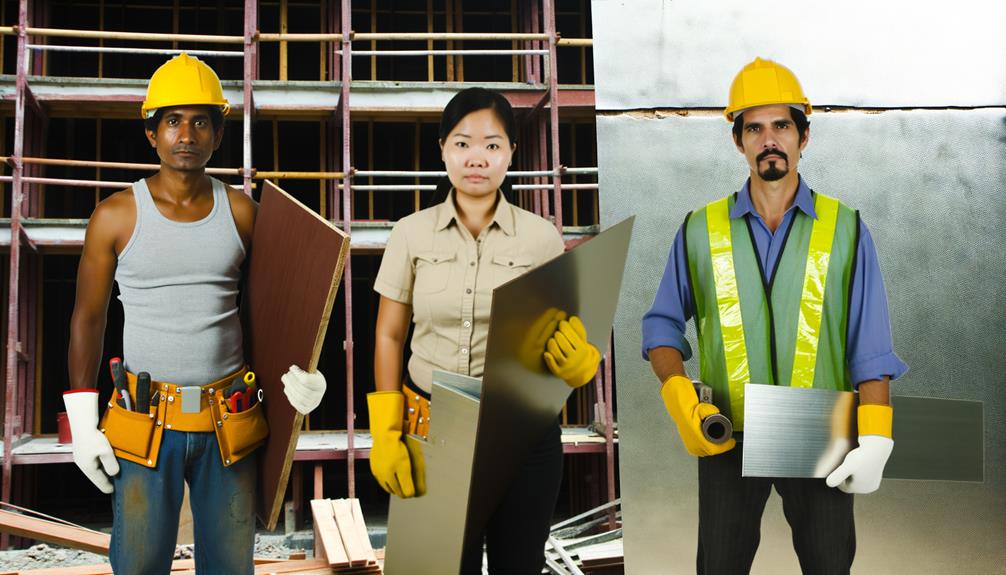
We often compare formwork materials—wood, steel, aluminum—in construction. Wood is cost-effective for smaller projects and environmentally friendly; however, its lifespan is limited. Steel offers high durability and precision, but it's heavy and expensive initially. Aluminum achieves a balance: It's strong and lightweight but lacks versatility. Ultimately, the choice depends on the project's scale, lifetime cost-benefit analysis, and environmental impact. Diving deeper into the sustainability, recyclability, and specific pros and cons of each material uncovers the best fit for specific construction needs. Want to make an informed choice? There's much more to explore!
Understanding Formwork Materials
Explore the specifics of formwork materials, particularly highlighting wood, steel, and aluminum, each showcasing unique characteristics in relation to thickness, weight, and loading capacity. We need to understand each of these materials in detail to make informed decisions about their practicality and efficiency in construction projects.
Wooden formwork, typically constructed using timber or plywood sheets, has a thickness that ranges from 12 to 18 mm. Lightweight, it weighs between 10 to 12 kg/sqm, making it a popular choice for smaller projects. However, its loading capacity is lower, at around 25-30 kN/sqm, which may limit its use in larger, heavy-duty constructions.
Steel formwork, on the other hand, is made from steel sheets or panels. It's thicker, around 55 mm, and notably heavier, weighing between 35 to 85 kg/sqm. This weight and the greater strength of steel give it a higher loading capacity of 30-60 kN/sqm. It's resilient and durable, ideal for substantial construction endeavors.
Lastly, aluminum formwork is a blend of strength and weight. Constructed with lightweight aluminum panels or frames, it has a thickness of about 65 mm and weighs 20 to 25 kg/sqm. Impressively, despite its lower weight, aluminum formwork can support a loading capacity of 50-70 kN/sqm, making it a robust yet manageable option.
Benefits of Wooden Formwork
Diving into the benefits of wooden formwork, it's clear that its cost-effectiveness and lightweight nature stand as key advantages, despite potential trade-offs in labor and maintenance costs. Weighing around 10 to 12 kg per square meter, it's less burdensome to transport and handle on-site compared to heavier materials. This lightweight characteristic also aids in reducing the manpower and equipment required, thereby decreasing overall project costs.
For budget-conscious projects, wooden formwork emerges as an appealing choice due to its lower upfront material cost. This factor, coupled with its thickness range of 12 to 18 mm, provides a balance of affordability and functional performance. The ability to withstand a loading capacity of 25-30 kN/sqm further accentuates its viability for a multitude of construction projects.
Beyond the financial and logistical aspects, the environmental benefit of wood as a renewable resource shouldn't be overlooked. This feature, coupled with the capacity for 5 to 8 repetitions, provides a measure of sustainability in construction projects.
However, it's worth noting that the installation and dismantling of wooden formwork can be laborious and time-consuming. These factors must be weighed against its cost and environmental benefits when making a selection. Despite this, its unique blend of affordability, lightweight nature, and renewable source make wooden formwork a viable choice for many construction projects. In our quest for liberation from excessive costs and environmental harm, these benefits of wooden formwork can't be dismissed lightly.
Drawbacks of Wooden Formwork
While wooden formwork presents several advantages, it's important to ponder its drawbacks, including its limited lifespan, susceptibility to damage, and labor-intensive installation process. Wooden formwork typically allows for only 5 to 8 uses, a stark contrast to its steel and aluminum counterparts. This limited lifespan often necessitates replacement, leading to increased costs and delays in project completion.
Additionally, wood is much more prone to wear and damage. Its structural integrity can be compromised by factors like moisture, termites, or rough handling, necessitating regular inspection and maintenance. It's also worth noting that wooden formwork has a lower load-bearing capacity, around 25-30 kN/sqm, which may limit its suitability for heavy-duty construction projects.
Moreover, the installation and dismantling of wooden formwork are time-consuming and labor-intensive processes. The need for skilled laborers, coupled with the longer time required, can inflate labor costs, offsetting the initial cost-effectiveness of the material.
Let's take a look at these drawbacks in a summarized table for easier comprehension:
Drawback | Explanation | Impact |
---|---|---|
Limited lifespan | 5-8 uses before replacement | Increased costs and delays |
Susceptibility to damage | Prone to wear from moisture, termites, rough handling | Regular maintenance and potential replacement |
Labor-intensive installation | Requires skilled labor and longer time | Increased labor costs |
Advantages of Steel Formwork
Shifting our focus to steel formwork, we find a multitude of advantages that make it a favored choice in demanding construction environments. Its high durability, rigidity, and strength render it a prime solution for rigorous construction projects. These characteristics mean that steel formwork stands up to the test of time and the pressures of heavy-duty work, offering a steadfast reliability that's appreciated in the construction world.
A significant advantage of steel formwork is its reusability. Unlike other materials that deteriorate rapidly, steel formwork can be used and reused multiple times. This trait provides not only a sustainable choice but also long-term cost savings and efficiency. In the long run, the initial investment in steel formwork is offset by its continued performance and low maintenance costs.
Furthermore, the non-absorbent nature of steel formwork reduces the risk of concrete honeycombing. This guarantees a quality finish, enhancing the overall look and longevity of the construction. The precise, smooth finish that steel formwork offers is unparalleled by other materials.
Customization is another strength of steel formwork. Adjustments to components are easier and more precise compared to other materials. This flexibility allows for the creation of unique, complex structures without compromising structural integrity.
Lastly, the strength and durability of steel formwork make it a preferred choice for large-scale concrete construction projects. Its ability to withstand high pressure and weight makes it ideal for substantial structures. We can confidently assert that steel formwork, with its multiple advantages, is a liberating choice for those seeking efficiency, durability, and quality in their construction projects.
Disadvantages of Steel Formwork
Despite the numerous benefits of steel formwork, it's important to acknowledge its drawbacks as well, which can substantially impact a project. One of the most substantial disadvantages of steel formwork is its weight. Heavier than aluminum, it presents a significant challenge in transportation and handling on site. This heavy weight can lead to increased labor requirements for installation and dismantling, adding to the project's overall labor costs.
Moreover, steel formwork's cost is an enormous factor to take into account. Typically, it's more expensive than its wooden counterpart, resulting in a higher initial project cost. These increased costs can create financial strain, especially for projects operating under tight budgets.
Another downside of steel formwork is its susceptibility to rust if not properly maintained. This corrosion can greatly affect the formwork's longevity and reusability, leading to additional costs in the long run. Regular upkeep and maintenance are hence crucial, adding another layer of costs and responsibility to the project.
Adding to this, steel formwork's high scrap metal value exposes it to potential theft on construction sites. This vulnerability necessitates additional security measures, another cost and logistical factor to take into account.
While steel formwork does offer several notable advantages, these disadvantages can't be overlooked. Each project needs to weigh these factors carefully, considering the impact of these drawbacks on the project's timeline, budget, and overall feasibility. As we navigate the complexities of formwork material selection, it's essential to take into account all aspects of each option before making a decision.
Pros of Aluminum Formwork
Turning our attention to aluminum formwork, we can't help but notice its several advantages that make it an attractive choice for many construction projects. Its light weight, for instance, eases transportation and handling on construction sites, thereby reducing labor intensity and increasing efficiency.
One of aluminum's most important attributes is its strength and durability. It withstands high concrete pressures during construction, ensuring stability and safety. Additionally, aluminum formwork is resistant to rust and corrosion, guaranteeing longevity and allowing its reuse in multiple projects.
Advantages | Description |
---|---|
1. Weight | Lighter, easier to transport and handle. |
2. Durability | Withstands high pressures, rust and corrosion resistant. |
3. Quality | Produces high-quality concrete surfaces without additional finishing. |
The quality of concrete surfaces produced using aluminum formwork is another remarkable benefit. Thanks to its smooth finish, additional finishing processes are often unnecessary, leading to savings in time and resources. This aspect greatly enhances the aesthetic appeal of the completed structure.
Perhaps, the most liberating advantage of aluminum formwork is its rapid installation and dismantling. This attribute not only saves time but also reduces labor costs, making it a cost-effective solution in the long run. It thereby contributes significantly to the overall project efficiency, enabling quicker turnover times and higher project throughput.
Cons of Aluminum Formwork
While we've acknowledged the numerous benefits of aluminum formwork, it's important to also ponder its drawbacks for a balanced perspective. The first disadvantage to ponder is the potential for theft. Due to the higher resale value of aluminum scraps compared to steel, aluminum formwork is more likely to be stolen. This risk could result in unexpected project delays and additional costs for replacement.
Secondly, aluminum formwork lacks versatility in the long run. It's harder to modify and customize compared to steel formwork. This limitation could prove problematic when undertaking construction projects that require unique or non-standard formwork designs. Steel, in contrast, can be adapted more easily, offering greater flexibility.
Moreover, as much as aluminum formwork is lighter in weight than steel, making it easier to transport, this attribute isn't always beneficial. The lightweight nature of aluminum can sometimes lead to stability issues, especially in windy conditions. These conditions can pose safety risks to the construction site and the workers.
Lastly, while aluminum formwork is often ideal for large concrete construction projects where weight and transportation are key considerations, it may not be the best choice for smaller or less complex projects. The higher initial cost of aluminum formwork, although potentially cost-effective in the long term due to its durability and reusability, mightn't be justifiable for smaller projects with tighter budgets.
Cost Comparison: Wood, Steel, Aluminum
In analyzing the costs of wood, steel, and aluminum formwork, we need to take into account not just the initial material prices, but also factors such as maintenance, labor, and reusability. It's not just about the upfront cost, but the total cost of ownership.
For a more in-depth understanding, let's break down the costs associated with each material:
- Wood Formwork: Wood may seem like the cheapest option initially. However, when you factor in the higher labor and maintenance costs, the total cost of ownership can quickly add up. Additionally, wood formwork isn't as reusable as steel and aluminum, so you'll need to account for replacement costs.
- Steel Formwork: Steel has a higher initial cost than wood. But it's more durable, reusable and requires less maintenance. In the long run, these factors can make steel more cost-effective than wood.
- Aluminum Formwork: Aluminum might be the most expensive upfront. However, it also offers the best durability and reusability. Over time, these qualities can make aluminum the most cost-effective choice.
- Total Cost of Ownership: Remember, the choice between wood, steel, and aluminum formwork shouldn't be based solely on upfront costs. It's important to take into account the total cost of ownership, which includes maintenance, labor, and reusability.
Durability Across Materials
After evaluating the costs, we must now shift our focus to another important aspect – the durability of wood, steel, and aluminum formwork. It's a vital factor that can greatly impact the lifecycle and overall cost-effectiveness of a project.
Assessing these materials head-to-head, steel formwork stands out as the most durable option with a longer lifespan and resistance to wear and tear. It's built to withstand multiple reuses, making it a cost-effective choice in the long term. Though initially pricier, the extended longevity and sturdiness guarantee a worthwhile investment.
On the other hand, aluminum formwork, while not as robust as steel, offers impressive durability. It's resistant to rust and corrosion, contributing to an extended lifespan. This makes it a reliable choice for long-term use, especially in environments where corrosion could be a concern.
Wooden formwork, unfortunately, doesn't fare as well. It's more susceptible to wear and damage over time. Though cheaper initially, the limited durability could lead to increased costs over time due to the need for frequent replacements.
Here's a succinct comparison:
Material | Durability | Lifespan |
---|---|---|
Steel | High | Long |
Aluminum | Medium | Long |
Wood | Low | Short |
Installation and Dismantling Differences
Moving on to the differences in installation and dismantling, it's evident that each material presents unique advantages and challenges. This process is a vital consideration when selecting formwork materials as it directly impacts construction timelines and labor costs.
- Steel Formwork: Steel is known for its robustness and rigidity. However, these same characteristics can make installation and dismantling more labor-intensive compared to other materials. Steel's weight necessitates a higher degree of manpower or machinery aid during these stages. But once installed, it's a reliable option that offers stability and precision.
- Aluminum Formwork: Aluminum formwork is the star of the show when it comes to ease of installation and dismantling. Its lightweight nature means less labor is needed, and the process can be completed more rapidly. This speed and efficiency can contribute to quicker project completion, making aluminum an attractive option for projects with tight deadlines.
- Wooden Formwork: Wooden formwork typically requires more time and effort to install and dismantle. However, it's worth noting that these challenges can be mitigated with skilled labor. Despite the extra effort, wood remains a popular choice due to its versatility and cost-effectiveness.
- Comparative Analysis: Steel requires more effort but offers reliability. Aluminum stands out for its speed and efficiency, while wood, although more labor-intensive, remains a cost-effective choice.
Sustainability in Formwork Selection
When it comes to sustainability in formwork selection, steel and aluminum prove more eco-friendly than wood due to their superior durability and reusability. These materials, often perceived as environmentally taxing due to their energy-intensive production, compensate with their ability to withstand repeated use. This offsets the environmental impact and promotes a more sustainable construction practice.
Contrarily, wood formwork, despite its natural origin, lacks the longevity of its metallic counterparts. This necessitates frequent replacement and disposal, contributing to a cycle of waste that's far from sustainable. By choosing steel or aluminum, we're endorsing a reduction in material wastage and contributing to a greener construction industry.
The robustness of steel and aluminum formwork isn't their only strength, though. Their long lifespan also minimizes the need for constant replenishment of resources. This is paramount in an era where resource conservation is a global concern. Additionally, these materials aren't bound by a single-use destiny. Their recyclability, without loss of quality, adds another layer to their eco-friendly profile. Though this point goes into our next topic, it's worth noting here as it underpins the sustainability argument.
Recyclability: Steel Vs. Aluminum
Building on the sustainability value of steel and aluminum formwork, we must also consider their recyclability, a key factor that further enhances their ecological benefits. Both these materials contribute markedly to the circular economy – a system aimed at eliminating waste and making the most of resources.
In the context of recyclability, let's explore some specific factors:
- Recycling Rate: Steel formwork boasts an impressive recycling rate of about 90%. This high rate entails noteworthy reductions in waste, making it a cornerstone for sustainable construction. Conversely, aluminum formwork, with a recycling rate of 60-70%, also presents an environmentally responsible choice.
- Reusability: Both steel and aluminum can be melted down and reused without compromising their quality. This characteristic guarantees a longer lifespan for these materials, promoting resource conservation.
- Emission and Energy Consumption: The recycling process for both steel and aluminum formwork helps in reducing greenhouse gas emissions and energy consumption. This reduction, when compared to producing new materials, is substantial and therefore, greatly beneficial to our environment.
- Project's Sustainability Goals: The selection between steel and aluminum can be influenced by the project's sustainability goals. Both materials offer recyclability benefits, but the choice will ultimately depend on a balance of factors including cost, availability, and specific project requirements.
Making the Right Formwork Choice
Traversing through the selection process for the right formwork material requires a thorough analysis of the project's scale, its specific requirements, and the cost-benefit evaluation of each option. It's not just about picking one material over another; it's about finding the best solution that aligns with your project's specific needs.
Considerations should start with an evaluation of the project's scale and requirements. Larger, more complex projects may necessitate the strength and durability of steel, while smaller or temporary structures may be better suited to the lightweight, transportable nature of aluminum. Wood, on the other hand, might be a cost-effective solution for projects with lower budgets or less demanding structural requirements.
The initial cost is only part of the equation. We've got to factor in the long-term implications as well. While wood may be cheaper upfront, it could incur higher maintenance and labor costs over time. Steel and aluminum, although more expensive initially, offer superior durability and reusability, potentially leading to savings in the long run.
Additionally, we need to contemplate the speed of installation and dismantling, as well as the environmental impact of each material. Steel and aluminum are recyclable, contributing to a lower environmental footprint.
Frequently Asked Questions
Is Aluminium Formwork Better Than Timber Formwork?
We believe aluminum formwork is superior to timber. It's stronger, more durable, and resistant to damage. Despite its higher initial cost, it's more cost-effective in the long run due to its reusability.
It also saves time and labor since it's easier and quicker to install and dismantle. Additionally, it provides a smoother concrete finish than timber. So, we'd argue that aluminum formwork is indeed better than timber.
Is Aluminum Formwork Better Than Steel Formwork?
We can't definitively say aluminum formwork is better than steel. It's lighter, making it easier to handle on-site, and it's generally cheaper.
But steel's stronger and more durable, making it better for long-term use. Steel can also be customized more easily, offering greater design flexibility.
Is Metal Formwork Better Than Timber Formwork?
We believe metal formwork outperforms timber. It's more durable, reusable, and can withstand heavier loads.
While timber handles 25-30 kN/sqm, steel manages 30-60 and aluminum 50-70. Metal's resistance to water, rust, and corrosion means less maintenance and a longer lifespan.
Steel can be reused 100-120 times and aluminum over 200 times, making both cost-effective. So, in our view, metal formwork is a superior choice to timber.
What Is the Disadvantage of Aluminium Formwork?
We've found a few drawbacks to aluminum formwork. It's not as flexible for future modifications compared to steel. There's also a higher theft risk due to aluminum's high scrap value.
While the initial cost can be steep, it's cost-effective over time because of its durability. Despite these cons, its light weight makes it easier to handle and transport on site.
Conclusion
To sum up, selecting the right formwork material isn't a one-size-fits-all decision. It's about evaluating the pros and cons, taking into account the project's requirements, and the environmental impact.
While wood is cost-effective and versatile, steel offers strength and reusability. Aluminum, being lightweight and recyclable, brings sustainability to the table.
So, it's important to make an informed decision that balances all these factors, ensuring project success and environmental responsibility.