Formwork for Tunneling Projects: Innovations in Underground Construction
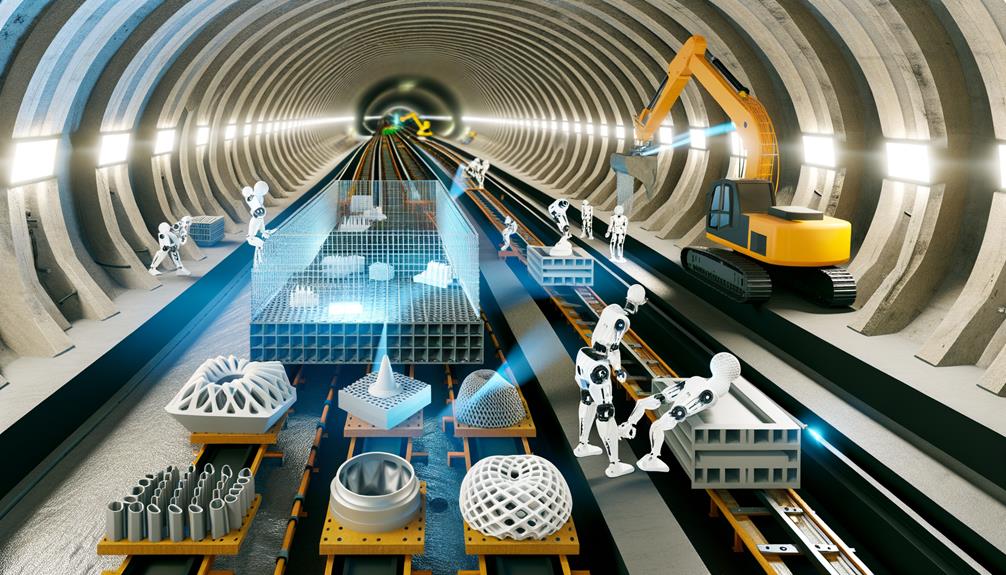
Innovative formwork solutions are transforming underground tunneling projects. Technologies like track-free traveling formwork and hydraulic steel formwork carriages optimize time and materials. Leading providers like Doka and PERI offer advanced systems that enhance safety and efficiency in tunnel construction. Tailored concrete technologies provide the structural backbone, ensuring stability and longevity of tunnels. Adapting these technologies to different tunnel-building methods, including cut-and-cover and mining-type construction, has infinitely expanded potential applications. Further exploration of these innovations promises to reveal more game-changing possibilities in the field of tunnel construction.
Innovation in Tunneling Construction
As we explore the domain of tunneling construction, it's evident that innovations in advanced formwork solutions are paving the way for more efficient and safer projects. The advent of specialized formwork systems, such as track-free travelling formwork and hydraulic steel formwork carriages, is catalyzing a revolutionary shift in tunnel construction processes.
These tailor-made formwork solutions aren't just a demonstration of progress in technology. They're a leap towards liberation from old, inefficient practices. They offer significant time savings, material efficiencies, and enhanced productivity, thoroughly transforming the landscape of tunneling projects.
In this era of rapid advancements, collaboration is key. The successful implementation of these cutting-edge formwork technologies is a confirmation of the synergistic efforts of engineering teams and construction companies. It's a vivid example of how we can break free from traditional constraints and move towards a more progressive, productive future.
Companies like Doka and PERI are at the forefront of this evolution, providing tailored formwork solutions that exemplify the industry's commitment to delivering high-quality, cost-effective, and safe tunneling projects. Their pioneering solutions aren't just meeting industry standards but setting new ones.
Innovation in tunneling construction is more than just an industry trend; it's a visionary approach that redefines how we build the world beneath us. By embracing these advancements, we're not only enhancing efficiency and safety but also paving the way for a future where the confirmation becomes possible. The future of tunneling isn't just about digging deeper, but also building smarter.
Importance of Traffic Route Construction
Delving into the importance of traffic route construction, we find that the consistent rise in global tunnel construction since the 1960s has profoundly impacted individual traffic and international trade. This growth, driven by the need for efficient and safe transportation, has led to remarkable advancements in traffic networks worldwide.
Tunnel construction has emerged as a groundbreaking solution, reducing distances, avoiding detours, and enhancing traffic flow efficiency. It's not just about saving time and costs; it's also about safeguarding urban areas from noise and pollution emissions. By burying traffic in tunnels, we're improving environmental quality, making our cities more livable and sustainable.
Bridges and tunnel structures are no longer mere architectural marvels; they're crucial arteries in our global transportation system. They represent the embodiment of human ingenuity and an unwavering commitment to progress.
The focus in traffic planning is now shifting towards acceleration, decentralization, and relocation. We're aiming to create reliable, safe, and uninterrupted travel routes, especially in urban and rural areas. Our vision is to construct traffic networks that liberate people from the constraints of geography, enabling them to connect, communicate, and trade seamlessly.
In essence, traffic route construction has become a cornerstone of growth and development. It's not just about building roads; it's about shaping our future, one tunnel at a time. This evolutionary process underscores the crucial role of formwork in tunnel construction, paving the way for a future where distance is no longer a barrier, but a gateway to boundless possibilities.
Principles and Targets of Tunnel Construction
Building on the foundational role of traffic route construction, let's now explore the principles and targets of tunnel construction, a field that goes beyond mere engineering to encompass a vision for seamless, safe, and sustainable transportation.
The principles of tunnel construction are largely dictated by the geological conditions and project requirements, guiding the selection of appropriate load-bearing structures. It's not a pivotal approach; instead, we carefully choose from a variety of construction methods, including open-cut tunneling and mining techniques, to cater to the unique characteristics of each tunnel.
Principle | Description | Example |
---|---|---|
Geological Conditions | Ground characteristics govern tunnel construction | Selective use of open-cut or mining techniques |
Project Requirements | Specific needs steer the construction approach | Use of standard or special cross-sections |
Load-bearing Structures | Structural choice is critical for stability | Selection based on geology and project needs |
Our targets in tunnel construction are, however, unwavering. We aim to create reliable, safe, and uninterrupted travel routes that can fuel economic integration. By reducing distances, avoiding unnecessary detours, and protecting from emissions, tunnel structures play a vital role in shaping robust traffic networks.
Target | Benefit | Outcome |
---|---|---|
Reliable Routes | Ensures smooth travel | Economic integration |
Safety | Reduces accidents | Public confidence in infrastructure |
Uninterrupted Travel | Avoids detours | Time and cost savings |
In essence, tunnel construction is a balancing act of principles and targets, a visionary endeavor that seeks to liberate transportation from its conventional constraints, paving the way for a more connected future.
Role of Concrete Technology in Tunneling
In the world of tunnel construction, concrete technology plays an indispensable role, providing the structural backbone that guarantees the durability, stability, and safety of these subterranean passageways. This technology isn't a one-size-fits-all solution, but rather a versatile tool that we adapt to the unique specifications, geological conditions, and intended usage of each tunnel project.
The selection of construction types and load-bearing structures is a confirmation of the flexibility of concrete technology. Depending on the characteristics of the tunnel, we might choose a variety of load-bearing structures, each designed to accommodate specific geological conditions. This approach not only confirms the structural integrity of the tunnel but also maximizes its functional potential, whether for transportation, utilities, or other uses.
Standard and special cross-sections further illustrate the adaptability of concrete technology. By tailoring these sections to the needs of each tunnel project, we're able to optimize the use of materials, streamline the construction process, and enhance the durability of the finished product. This level of customization is only possible because of the progress we've made in concrete technology.
In the end, the application of concrete technology is about more than just building tunnels. It's about creating safe, durable, and efficient infrastructures that meet the demands of modern society. It's about pushing the boundaries of what's possible in underground construction, paving the way for future innovations. It's about liberating ourselves from the constraints of traditional construction methods and embracing the limitless potential of concrete technology in tunneling.
PERI Solutions for Tunnel Construction
Traversing the complexities of tunnel construction, we often turn to PERI, a company renowned for their innovative formwork solutions specifically tailored for such intricate projects. This global powerhouse simplifies the challenging task of tunnel construction with their modular approach to formwork and scaffolding systems. Their prowess in providing precise, dependable, and sustainable solutions is a proof of their commitment to liberating us from traditional constraints.
To appreciate the magic that PERI brings to the table, let's explore their key offerings:
- Innovative Formwork Solutions: PERI's formwork solutions aren't just products; they're game changers that transform the way we think, design, and execute tunnel construction projects.
- VARIOKIT Engineering Construction Kit: Covering all life cycle phases of tunnel structures, this kit brings versatility and adaptability to our fingertips.
- Modular Concept: The beauty of PERI's modular concept lies in its simplicity and variability. It empowers us to adapt to changing project requirements without sacrificing efficiency or quality.
- Global Consulting, Planning, and Engineering Capabilities: PERI isn't just a supplier, but a reliable partner who walks the journey with us, providing expert advice and strategic insights every step of the way.
Dokas Approach to Tunnel Projects
Exploring the maze of tunnel construction, we uncover Doka's approach, which provides custom formwork solutions tailored to the distinctive requirements of each project, including those utilizing the cut-and-cover construction method. Envisioning a world of seamless construction, Doka weaves a network of international logistics that enable quick responses to unforeseen influences, fostering an environment of freedom and resilience in the face of uncertainty.
In the pursuit of a harmonious balance of quality, safety, and cost-effectiveness, Doka has engineered modular systems that aim to bring tunnel projects in on-budget without compromising on the integrity of the infrastructure. These systems are a reflection of Doka's commitment to creating adaptable and agile solutions that cater to the emerging complexities of tunnel construction.
Doka's avant-garde formwork solutions, such as the Load-bearing tower SL-1 and Tunnel System MT, illustrate their innovative approach to meeting the unique needs of tunnel construction. These systems represent the embodiment of Doka's analytical and visionary mindset, merging practicality with ambitious design.
Beyond just providing formwork solutions, Doka explores project-specific planning. Their customer-oriented approach to top-cover method tunnel construction demonstrates an understanding of the diverse range of project requirements, offering liberation from the constraints of traditional construction methods.
Cut-And-Cover Vs Mining-Type Tunnel Construction
As we progress, let's compare and contrast the cut-and-cover tunneling method with the mining-type tunnel construction, shedding light on how Doka's innovative formwork solutions cater to the unique demands of these two approaches.
The cut-and-cover method involves excavating a trench from the surface, constructing the tunnel, and then covering it with excavated soil. It's a cost-effective approach often used in urban areas. Doka provides us with cost-optimized formwork solutions tailored to this method.
On the other hand, mining-type construction involves creating tunnels underground and continuously stabilizing them. It's a more complex procedure, but Doka rises to the challenge by providing project-specific formwork solutions that streamline the construction process.
Now, let's explore the specifics. Here's how Doka revolutionizes formwork solutions for these two methods:
- Load-bearing tower SL-1: This solution helps distribute the loads in the cut-and-cover method, ensuring stable and safe construction.
- Large-area formwork Top 50: This is perfect for the mining-type construction with its flexibility and cost-effectiveness.
- Tunnel System MT: This system is designed for all tunnel cross-sections, making it versatile for both methods.
- Supporting construction frame: This supports the weight of fresh concrete and other loads, guaranteeing the safety and stability of the project.
In essence, Doka's formwork solutions cater to the unique demands of both tunneling methods. They not only provide efficient and tailored solutions, but also guarantee safety and stability. With Doka as a partner, we're truly unlocking the potential of underground construction.
Adapting to Different Tunnel-Building Methods
When it comes to adapting to different tunnel-building methods, we find Doka's tailored formwork solutions to be a game-changer, offering unparalleled flexibility and efficiency across cut-and-cover, mining-type, and top-cover construction techniques. With specific formwork solutions, such as Load-bearing tower SL-1 and Tunnel System MT, different tunnel-building requirements are competently catered for.
Tunneling Method | Doka's Solution | Benefits |
---|---|---|
Cut-and-Cover | Load-bearing tower SL-1 | Adapts to varying widths, heights, and inclines |
Mining-Type | Tunnel System MT | Optimizes concrete cycle times |
Top-Cover | Large-area formwork Top 50 | Flexibility in forming different shapes and sizes |
All Methods | Load-bearing tower Staxo 100 | Provides high load capacity and safety |
All Methods | Supporting construction frame | Offers versatility and stability |
We're struck by how Doka's large-area formwork Top 50 and Load-bearing tower Staxo 100 provide efficient support for tunnel projects. The versatility and stability offered by the company's supporting construction frame holds immense promise for various tunnel construction scenarios. It's not just about the technology, but also about the vision and the ability to adapt and innovate.
Doka's global capabilities in consulting, planning, and engineering make it a reliable partner for diverse tunnel construction methods. The company is not merely a provider of formwork solutions but a collaborative partner in the quest for liberating engineering possibilities. By enabling us to break free from traditional constraints, Doka's tailored solutions are shaping the future of underground construction.
Frequently Asked Questions
What Is the Tunnel Formwork Method?
We're discussing the tunnel formwork method, a revolutionary technique in tunnel construction. It involves creating temporary molds to shape concrete structures. This innovative solution guarantees precision, offering us efficiency and adaptability to various tunnel shapes.
It's not just about speed and reduced labor, it's safety too. With formwork systems, we're ushering in a new era of structural integrity and quality in underground constructions.
This is our path towards liberation in construction.
Which Method Is Used for Underground Tunnel Construction?
We're commonly using three methods for underground tunnel construction: cut-and-cover, mining-type, and top-cover. Each has its own unique benefits. Cut-and-cover is a simple, cost-effective technique, while mining-type provides excellent structural stability.
The top-cover method, on the other hand, allows for precise planning and construction. Selecting the right method is crucial for a successful, safe, and efficient project.
What Are the Advantages of Tunnel Formwork System?
We're seeing remarkable benefits with tunnel formwork systems. They're saving us around five days per wall, cutting down on labor, and reducing materials. We've noticed significant cost savings and a boost in efficiency.
With track-free travelling formwork, we're moving faster and avoiding construction clashes. Plus, reusable steel components are providing a sustainable edge.
It's a groundbreaking innovation, transforming how we think about underground construction.
What Are the Disadvantages of Tunnel Formwork?
We've identified several disadvantages of tunnel formwork.
High initial costs for specialized systems are a significant drawback. We're also faced with the challenges of limited space and intricate geometries in formwork design.
Managing maintenance and storage often requires dedicated facilities. Varying tunnel cross-sections pose logistical issues.
Finally, installation in tunnels can be time-consuming and labor-intensive compared to above-ground structures.
We're constantly seeking solutions to these issues.
Conclusion
As we've explored, innovative formwork solutions are reshaping tunnel construction. The role of concrete technology is crucial, with PERI and Dokas leading the charge.
Whether it's cut-and-cover or mining-type tunnels, adapting to different methods is key.
Looking ahead, we foresee a future where these advancements streamline traffic route construction, underpinning efficient, safer, and more sustainable underground projects.
Let's continue pushing the boundaries of tunnel construction, transforming the way we navigate our world.