Formwork for Specialized Structures: Challenges and Solutions
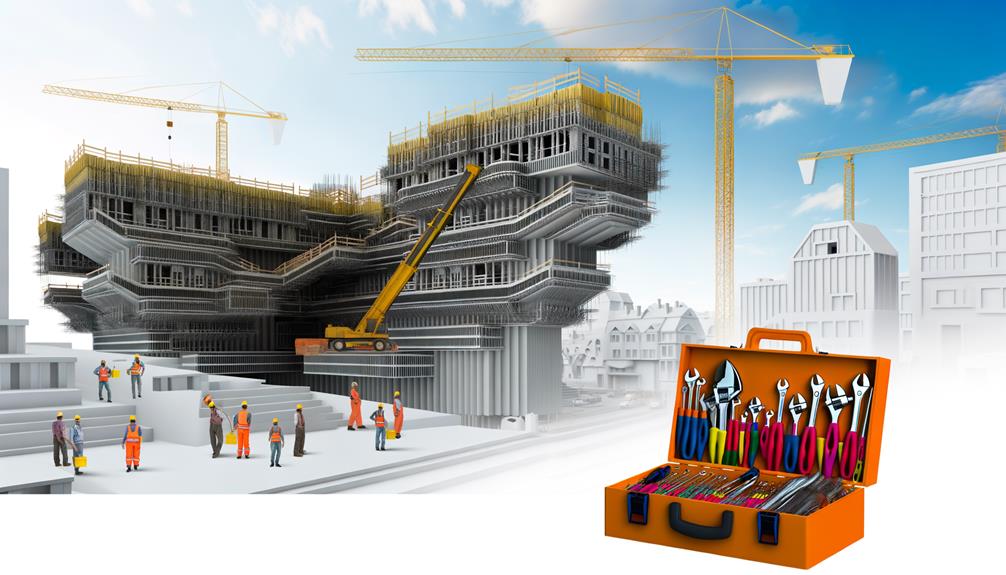
Specialized formwork in construction involves unique challenges like complex geometries, irregular shapes and intricate detailing. These demand innovative, custom solutions and high-quality precision. To tackle these, we're breaking boundaries with advanced materials and technologies. Advanced composites, use of recycled materials, self-healing properties – these are all part of our toolkit. We're also enhancing accuracy and speed with self-climbing and hydraulic support systems, as well as automated tech like robotics. With successful examples like Gaudí's Colonia Güells church, we're showing how it's done. Stick around and you'll discover the exciting future trends we're initiating in the field.
Understanding Specialized Formwork
Delving into the domain of specialized formwork, we find that it's a custom solution designed to meet the unique demands of non-standard structures, such as curved walls or complex geometries. This tailored approach allows us to navigate the intricate challenges that arise when standard formwork solutions fall short. Therefore, the essence of specialized formwork lies in its adaptability and precision, shaped by the specific demands of each project.
Advanced formwork technologies play a vital role in realizing these specialized structures. We harness these technologies to create complex forms with a significant level of accuracy and efficiency. The integration of technology not only streamlines the construction process but also expands the scope of possibilities, allowing us to bring even the most ambitious designs to life.
Innovation is another cornerstone of specialized formwork. We often incorporate cutting-edge materials and techniques to meet the unique requirements of each structure. This may involve the use of lightweight, high-strength materials, or the application of novel techniques that push the boundaries of conventional construction.
However, the success of specialized formwork hinges on expertise in design, fabrication, and installation. It's a process that requires a deep understanding of formwork principles, as well as the ability to translate complex designs into practical, buildable solutions. Every step of the process, from initial design to final installation, must be executed with precision to guarantee the successful construction of the structure.
Challenges in Specialized Formwork
Traversing the labyrinth of challenges in specialized formwork, we often encounter complex geometries, irregular shapes, and intricate detailing that demand custom designs and innovative solutions. These complexities place a heavy burden on our design and fabrication processes, pushing us to expand our knowledge and think outside the box.
- Complex Geometries: The sheer complexity of specialized formwork can be intimidating. It's not just about creating formwork for rectangular or circular structures. We're dealing with structures that have unconventional shapes and complex geometries. This poses a significant challenge in design, demanding a high level of precision and expertise.
- Irregular Shapes: In contrast to standard formwork, specialized formwork often involves irregular shapes. These irregularities require custom-made solutions, which can be time-consuming and cost-intensive. It's a delicate balancing act between adhering to the architect's vision and ensuring the feasibility and practicality of the formwork.
- Intricate Detailing: The detailing in specialized formwork can be incredibly intricate. A slight miscalculation or oversight can lead to structural instability or aesthetic flaws. The stakes are high, and the margin for error is slim.
Tackling these challenges requires more than just technical expertise. It demands a culture of innovation, a collaborative design process, and a willingness to push the boundaries of what's possible. We need to embrace these challenges as opportunities to evolve, to create formwork that isn't only functional but also aesthetically pleasing and structurally sound. It's about redefining the status quo and liberating ourselves from the constraints of traditional construction methods. As we navigate these challenges, we're not just building formwork—we're shaping the future of construction.
Innovative Material Selection
In the quest to tackle the complexities of specialized formwork structures, we're turning to innovative material selection, including advanced composites, recycled materials, and bio-based alternatives, each offering unique advantages and novel solutions for design challenges.
Specialty materials like carbon fiber, fiberglass, and engineered wood are paving the way for high strength-to-weight ratio structures. They're not only durable and light but also versatile, allowing for a myriad of shapes and forms. On the other hand, eco-friendly options like bamboo, hempcrete, and mycelium-based materials are making waves for their sustainable attributes.
Material Type | Unique Advantages |
---|---|
Advanced Composites | High strength-to-weight ratio |
Recycled Materials | Cost-effective and eco-friendly |
Bio-based Alternatives | Sustainable and renewable |
Smart Materials | Self-healing, adaptable to conditions |
Taking it a step further, we're seeing the emergence of smart materials with self-healing properties and adaptability to environmental conditions. Picture formwork that can repair its own cracks or adjust to temperature changes – a game-changer in durability and longevity.
And let's not forget the potential of integrating technology within these materials. Sensors and actuators embedded in formworks can greatly enhance monitoring, performance, and efficiency, leading to safer and more reliable structures.
Advanced Support Systems
Moving onto advanced support systems, we're witnessing a remarkable shift in efficiency and productivity with the introduction of self-climbing formwork and hydraulic systems, both of which greatly enhance continuous vertical construction progress. These systems are revolutionizing construction processes, liberating us from the constraints of traditional methods, and facilitating the creation of structures that previously seemed unattainable.
Self-climbing formwork offers distinct advantages, allowing construction to proceed at varying heights without the need for dismantling and reassembling. This not only streamlines the construction process but also reduces the risk of accidents, enhancing the safety of the workforce.
Hydraulic systems, on the other hand, offer a safe and efficient solution for supporting formwork during high-rise building construction. They can be adjusted to accommodate a wide range of load capacities, providing the flexibility needed in modern construction projects.
Automated formwork systems, like robotic arms, are another game-changer. They enhance precision and speed in formwork placement and support, thereby optimizing construction processes.
To illustrate, let's consider the following:
- Telescopic props: These offer adjustable heights, providing flexibility and adaptability in formwork construction. They're instrumental in accommodating varying site conditions and design requirements.
- Self-climbing formwork: This facilitates continuous vertical construction progress, eliminating the need for cumbersome and time-consuming reassembly after each level.
- Automated systems: These utilize technology such as robotic arms to boost precision and speed, maximizing efficiency and productivity.
Case Studies: Real-world Applications
Let's explore some fascinating case studies that highlight the real-world applications and effectiveness of specialized formwork in innovative architectural projects. These cases demonstrate how intricate design challenges have been overcome using unique formwork solutions, proving both their practicality and versatility.
The first case is Gaudí's Colonia Güells church which exhibits the innovative use of hyperbolic paraboloids in formwork for specialized structures. Next, we have Luis Moya's hyperbolic paraboloid roof for School Santa María del Pilar, showcasing the practical application of formwork in unique architectural endeavors.
Formwork techniques have also been adapted to integrate tile vaults in concrete shells, further expanding their versatility. Experimental research on composite structures with tile vaults provides enlightening insights into the efficiency of formwork in complex construction scenarios.
It's important to note that construction techniques are validated through load tests and prototypes, ensuring the reliability and safety of these formwork solutions.
Here's a quick overview of these case studies:
Case Study | Key Takeaway |
---|---|
Gaudí's Colonia Güells church | Hyperbolic paraboloids in formwork |
School Santa María del Pilar | Practical application of formwork |
Integration of tile vaults | Versatility of formwork |
Composite structures research | Efficiency of formwork |
These real-world applications liberate architectural design, allowing the creation of unique, specialized structures while ensuring practicality and safety. They truly highlight the game-changing potential of innovative formwork solutions in the world of architecture.
Future Trends in Formwork Technology
Building on the practical applications and real-world examples, we're now shifting our focus to the exciting future trends in formwork technology. The construction industry is rapidly evolving and the formwork sector is no exception. As we move forward, we're seeing a stronger emphasis on energy efficiency, noise reduction, and durability, all of which will dictate the design and functionality of future formwork technologies.
- Innovative Materials and Processes: A key trend we're seeing is the exploration of innovative formwork materials and processes. For instance, frozen sand, 3D-printed sand, and ice formwork are being tested for their potential benefits. Embracing these novel systems will allow us to shore up structures with improved efficiency and precision.
- Digital Integration: Another exciting development is the integration of digital technologies in formwork design. This not only boosts productivity but also enhances accuracy, leading to superior construction outcomes. By adopting digital software, we're able to design and visualize formwork solutions with precision, thereby reducing errors and saving valuable resources.
- Sustainability and Smart Systems: Additionally, the development of sustainable and smart formwork systems is a major focus in the evolving construction industry. We're moving towards eco-friendly materials and designs that minimize waste and maximize reuse. The advent of smart systems also allows real-time monitoring and control, leading to optimized performance and reduced risks.
Frequently Asked Questions
What Is the Problem With Formwork?
We're facing several problems with formwork. It's tricky to maintain structural integrity during concrete pouring and curing. Wrong material selection can lead to safety hazards.
Lack of adequate support can cause deformations and surface imperfections in concrete. Poor design might result in delays, spiraling costs, and compromised quality. All these complications need us to come up with precise formwork solutions, especially when dealing with complex structures.
What Is Formwork for Special Structure?
We're talking about formwork designed for unique, complex structures. It's not your everyday, run-of-the-mill type. This is for unconventional architecture and challenging construction needs.
We often customize these systems to a project's specific requirements. They're essential for creating artistic or iconic buildings. They're complex, requiring expertise, precision, and creativity.
It's not an easy task, but we're up for the challenge.
What Are the Factors Contributing to the Formwork Failure?
We've identified several factors contributing to formwork failures. These include insufficient support or inadequate bracing, poor quality materials, incorrect design, and overloading beyond capacity.
Environmental factors like strong winds or heavy rain also pose challenges. Additionally, lack of proper inspection and maintenance can lead to risks.
It's important to address these issues to prevent potential failures and guarantee the safety and efficiency of construction projects.
What Are the Advantages and Disadvantages of Formwork?
We've found that formwork offers numerous advantages like providing support for concrete during setting and ensuring accurate shapes. It's great for complex designs and promotes efficient construction.
However, it has its downsides. The initial setup can be costly, and the time for installation and removal can be lengthy. Poor formwork design can lead to defects and safety hazards. It's a give and take situation.
Conclusion
As we've explored, specialized formwork presents unique challenges, but with innovative materials, advanced support systems, and lessons from real-world applications, solutions are within reach.
We're excited by the potential of future formwork technology trends, poised to transform the construction industry.
Indeed, overcoming formwork challenges isn't just about building structures—it's about shaping the future of architectural design and construction.
We look forward to embracing this evolving landscape, continuing our quest for excellence in this critical field.