Formwork for Slab Construction: Reinforcement and Support
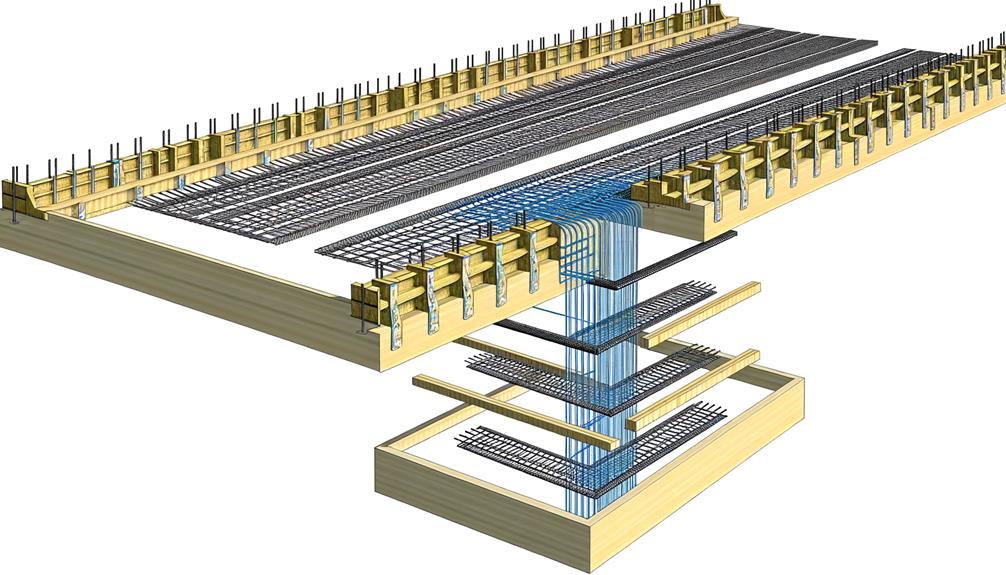
In slab construction, we utilize formwork as a mold that provides concrete its shape and structural support. We can't underestimate the importance of slab reinforcement for integrity and longevity. We customize our formwork design with precision, taking into account the weight of wet concrete, material choice, and support structure. Our goal is to guarantee the desired shape, strength, and finish. Choosing between different types, like sturdy steel Roadform or custom timber shuttering, depends on your project needs. Facing challenges, ensuring safety, and utilizing innovations like aluminum-framed panels are all part of the play. Continue on, and we'll unravel more about this intricate process.
Understanding Formwork Basics
To fully understand the complexities of slab construction, we must first explore the nitty-gritty of formwork, a temporary yet crucial support system that gives shape and structure to the concrete before it solidifies. This essential step in the construction process is often overlooked, yet it carries the weight and responsibility of ensuring a solid, durable slab.
Formwork systems comprise panels, beams, joists, and uprights. These components work in unison to distribute loads effectively, mirroring the kind of harmony we aim for in our own lives. Each part plays its role, contributing to the overall structural integrity and stability of the concrete slab during construction. Think of formwork as the scaffolding of your dreams, providing support and shape until they stand strong and independent.
However, the path to liberation isn't without its challenges. Just as we must understand our own strengths and limitations to grow, we must also recognize the importance of proper formwork in the slab construction process. Improper or inadequate formwork can result in structural instability, leading to costly and time-consuming repairs. We must be vigilant, ensuring that the formwork is robust enough to withstand the weight of our aspirations, the concrete.
Importance of Slab Reinforcement
Delving further into the bedrock of slab construction, we can't overlook the instrumental role of slab reinforcement, a pivotal strategy that strengthens the slab's structural integrity, minimizes risks during construction, and guarantees the slab's ability to bear the required loads with unwavering stability.
To understand the essence of slab reinforcement, it's important to appreciate the complex interplay of forces within the slab structure. Reinforcement not only resists these forces but also distributes them evenly across the slab, effectively preventing structural failure. To this end, we utilize tailored reinforcement solutions, optimizing the performance to meet specific project requirements.
Let's consider the following facets of slab reinforcement:
- Enhancing structural integrity: Reinforcement fortifies the slab, allowing it to withstand both anticipated and unexpected loads.
- Risk minimization during construction: Proper reinforcement techniques ensure a safer construction environment, reducing the risk of slab failure.
- Tailored solutions: The reinforcement strategy can be customized to meet the unique needs of the project, maximizing effectiveness.
- Durability and Longevity: Effective reinforcement can greatly extend the slab's lifespan, reducing maintenance costs and potential for damage over time.
In essence, the choice of appropriate reinforcement materials and techniques is paramount for ensuring the slab's durability and strength. Hence, slab reinforcement isn't merely an aspect of slab construction; it's a cornerstone, a confirmation of our commitment to safety, quality, and longevity. This understanding liberates us from the constraints of short-term thinking and propels us towards visionary construction practices, where every decision is rooted in a robust understanding of structural dynamics and an unwavering dedication to excellence.
Designing Effective Formwork
On the journey towards crafting superior slab constructions, we find ourselves at the critical stage of designing effective formwork, a process that demands precision, foresight, and a keen understanding of the materials at hand. This isn't merely about creating a mold for the concrete; it's about creating a supportive skeleton that guarantees the structural integrity, safety, and accurate placement of the concrete.
Designing formwork isn't just about the immediate task. It's about anticipating the weight of wet concrete and any additional loads that may be added during the construction process. This requires a deep understanding of the materials we're working with, their strengths, weaknesses, and how they interact under pressure. It's about making sure that the formwork can handle the task without buckling under the weight or shifting out of place.
The type of material we choose for the formwork, the support structure we design, and the bracing we incorporate all play pivotal roles in the quality and efficiency of slab construction. When we get this right, we facilitate the casting of slabs with the desired shape, strength, and finish. We guarantee that the slabs aren't just functional, but also aesthetically pleasing and built to last.
Designing effective formwork is about liberation. It's about freeing ourselves from the limitations of poor design and embracing the possibilities that precision, foresight, and understanding can bring to slab construction. It's about liberating the full potential of the materials we use and the structures we build. It's about crafting a future that's built on solid foundations and can withstand the test of time.
Different Types of Formwork
Having explored the design principles of effective formwork, let's now examine the distinct types of formwork – Steel Roadform and custom-made timber shuttering – shedding light on their unique characteristics and applications in slab construction.
Steel Roadform, known for its solidity, reusability, and stackability, is an ideal solution for standard slab constructions. It provides exceptional stability when faced with forces exerted by wet concrete and vibration equipment, ensuring the concrete slab maintains its shape during the setting process.
On the other hand, we've custom-made timber shuttering, versatile enough to conform to structures with odd shapes and greater depths. This formwork type allows for a more tailored approach, accommodating the intricacies of unique architectural designs. Key features of timber shuttering include form lining and bracing, which safeguard the formwork's strength and stability.
To summarize, we can list the important points about these two types of formwork:
- Steel Roadform is the go-to choice for standard slab constructions due to its robustness and reusability.
- It's easily stackable, making storage and transportation efficient.
- Custom-made timber shuttering is preferred for complex structures with unusual shapes or greater depths.
- Essential components of timber shuttering include form lining and bracing, enhancing its strength and stability.
Choosing the right formwork is a liberating process, offering you the freedom to execute your architectural vision without compromising on structural integrity. By appreciating the unique advantages and applications of Steel Roadform and custom-made timber shuttering, you can make informed decisions, ensuring a successful slab construction.
Challenges in Formwork Construction
Handling the challenges in formwork construction, we must guarantee proper reinforcement placement for structural integrity, support the weight of wet concrete during pouring and curing stages, and maintain absolute precision to guarantee accurate dimensions and load-bearing capacity. Ensuring these necessities, however, isn't a walk in the park, as it requires a deep understanding of how formwork operates under various conditions.
To further break down these challenges, we've prepared a detailed table:
Challenge | Reason | Solution |
---|---|---|
Reinforcement Placement | Ensures structural integrity | Accurate design and supervision |
Weight Support | Wet concrete is heavy | Precise calculations and sturdy materials |
Dimensional Precision | Dictates load-bearing capacity | Advanced tools and techniques |
Resistance to Forces | Includes pressure, vibrations, weather | Robust design and quality materials |
One of the overlooked challenges is the formwork's ability to withstand different forces, such as the pressure from wet concrete, vibrations from concrete consolidation, and harsh weather conditions. It's not enough to merely erect a formwork structure; it must be resilient and robust to ensure a safe and efficient construction process.
Another pressing challenge lies in preventing issues like concrete leakage and misalignment. These issues can compromise the concrete's quality and the overall project's success, leading to unnecessary costs and delays.
Best Practices for Formwork Installation
While overcoming the challenges in formwork construction lays the groundwork for success, it's equally important for us to focus on the best practices for formwork installation, which can greatly enhance the structural integrity of the concrete slabs. Let's explore deeply into these practices, ensuring we build a stronger, more efficient, and sustainable future in slab construction.
The first key practice is the secure bracing and aligning of formwork. This isn't just about installing the formwork; it's about doing it in a way that prevents displacement during concrete pouring and setting. Precision and accuracy are paramount here, as any misalignment can compromise the structural integrity of the slab.
Reinforcement within the formwork system is another vital practice. It's not just about using reinforcement, but using it adequately. This helps distribute loads evenly, preventing structural failures and enhancing the longevity and resilience of the concrete slabs.
We also believe in the power of high-quality release agents. When used effectively, they make formwork removal a breeze and enhance the surface finish of the concrete.
Securely brace and align formwork
Adequate reinforcement within the formwork system
Use of high-quality release agents
Seek professional advice
Lastly, we can't overstate the importance of seeking professional advice. An experienced eye can spot potential issues, optimize efficiency, and greatly improve the quality of the project. This step, while often overlooked, can be the difference between a successful project and a costly failure.
Safety Measures in Formwork Construction
In the domain of formwork construction, we can't underestimate the essential role of safety measures, which range from thorough training for workers to regular inspections of formwork components, all aimed at ensuring absolute structural integrity and stability. It's all about creating a safe and efficient work environment, liberating us from potential hazards and promoting productivity.
We're adamant about implementing proper training, ensuring that every worker knows how to handle equipment and materials safely. It's not just about knowing what to do; it's also about understanding why we do it. Safety isn't a box to tick; it's a culture we're cultivating.
Regular inspection of formwork components is another critical safety measure. It's not enough to assemble the components and hope they hold up; we must be proactive in checking for any signs of wear or damage. This vigilance enables us to spot potential issues before they become accidents waiting to happen.
We've also implemented fall protection systems such as guardrails, safety nets, or personal protective equipment. When we're working at height, we can't afford to take risks.
Safety Measures | Importance | Implementation |
---|---|---|
Proper Training | Ensures understanding of safety practices | Regular training sessions |
Regular Inspections | Prevents accidents due to wear or damage | Routine checks on all components |
Fall Protection Systems | Prevents injuries from falls | Use of guardrails, safety nets, etc. |
Following the manufacturer's guidelines for formwork assembly and usage is non-negotiable. These guidelines are there for a reason, and we respect that. Similarly, we don't skimp on supervision, keeping a watchful eye on all formwork activities to address any safety concerns promptly. Safety in formwork construction isn't a destination; it's a journey, and we're committed to traveling it responsibly.
Innovations in Formwork Technology
As we investigate the domain of innovations in formwork technology, we're observing a revolution in the form of advanced materials such as aluminum-framed modular panels for slab construction, reshaping the landscape of the industry. These innovations aren't merely superficial changes; they're fundamentally altering the way we approach slab construction, reinforcing our commitment to efficiency, strength, and optimum resource use.
Modern formwork systems now integrate lightweight yet sturdy components like aluminum beams and props, which greatly enhance the reliability and durability of the structure. This innovative approach guarantees the structural integrity of the slab, while also minimizing the overall construction time.
Let's explore some prime examples of such innovative formwork systems:
- Aludeck is a modular slab formwork system that leverages the strength of aluminum for a robust yet lightweight solution.
- Aluplus represents the next step in aluminum formwork technology, offering a versatile and efficient system for slab construction.
- Multiportal is a revolutionary system that combines the advantages of various formwork technologies into a single, highly efficient solution.
- ECO and 20 flex are systems that embody the principles of sustainability and flexibility in formwork construction, optimizing resources without compromising on strength or durability.
These groundbreaking innovations in formwork technology aren't just trendsetting; they're setting the pace for a future where the construction process is optimized, faster, and environmentally friendly. We're witnessing a liberation from traditional constraints in slab construction, and embracing a future where innovation fuels efficiency, resilience, and sustainable growth.
Frequently Asked Questions
What Type of Formwork Is Used for Slab?
We use various types of formwork for slab construction, including self-supporting slabs and waffle slabs. Self-supporting slabs directly distribute loads over the structure, eliminating the need for cross beams.
On the other hand, waffle slabs indirectly distribute loads over the bearing structure.
We also employ different formwork systems like Aludeck, Aluplus, Multiportal, ECO, and 20 flex depending on the specific needs of the project.
What Are the Reinforcement Requirements for Slab?
We're often asked about the reinforcement requirements for slab construction. It's all about strength and durability. Steel bars or mesh are typically used to boost structural strength.
Proper spacing and sizing of these reinforcements are essential for distributing loads evenly and preventing cracks. Factors like span, loads, and structural design determine the reinforcement needs.
Adequate reinforcement not only improves durability but also prevents deflection and increases load-bearing capacity.
What Is the Process of Formwork for Slab?
We start by designing the formwork to support the weight of the wet concrete.
Next, we set up the panels and install reinforcements like steel bars.
We then confirm everything is aligned properly before pouring the concrete.
It's crucial that we monitor the curing process to guarantee a smooth, level surface.
With careful planning and execution, we transform a temporary mold into a solid, robust concrete slab.
How Do You Support a Slab?
We back a slab by using a meticulously crafted formwork system. This system evenly disperses the loads and stresses during the setting and hardening process. We guarantee the formwork components, such as beams and joists, are robust and resistant to wear.
Depending on the type of slab, we'll utilize specific support methods to secure its integrity and stability. It's vital that we get this right — the future of the construction depends on it.
Conclusion
In exploring, we've delved into the intricacies of slab construction formwork, from understanding its basics to investigating its challenges.
We've highlighted the critical role of reinforcement and examined the various formwork types.
We've provided insights into best practices and safety measures and peeked at technological innovations shaping formwork's future.
This knowledge empowers us to craft more efficient, safer, and innovative formwork solutions, propelling the construction industry forward.