Formwork for Marine Construction: Corrosion Resistance
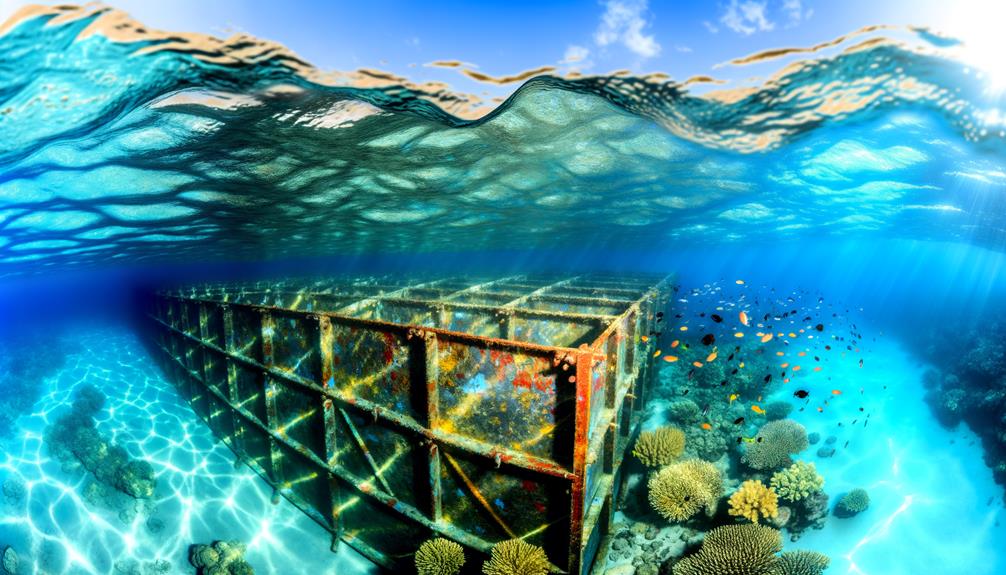
In marine construction, corrosion can be a real headache. That's why we opt for formwork materials that resist corrosion. Stainless or galvanized steel are our favorites because they withstand the harsh marine conditions. Regular maintenance is also key to keep corrosion at bay. Additionally, design techniques, like proper drainage systems, help minimize water exposure. Did you know about corrosion resistance tests? They help us select materials, particularly for those high-stakes projects! There's a lot more to contemplate when choosing the best solution, so let's continue exploring this fascinating aspect of marine construction.
Understanding Marine Construction
When we venture into the world of marine construction, we're exploring the intricate process of building robust structures in coastal or underwater environments that are constantly under siege from saltwater and corrosion. The task is formidable and demands a unique blend of expertise, innovative materials, and techniques. We're dealing with harsh conditions that require us to guarantee durability and longevity, lest our projects become victims of the unforgiving sea.
Marine construction projects are diverse and wide-ranging, encompassing the construction of ports, jetties, seawalls, offshore platforms, and other structures near or in water bodies. These environments are a test of our engineering prowess, challenging us to devise solutions that can withstand the relentless assault of the elements.
Understanding marine environments is pivotal in our quest to rise to this challenge. Our knowledge of these environments enables us to select the right materials, like corrosion-resistant steel formwork. This material is a champion in the face of saltwater exposure, promising durability in the face of adversity. It's a proof of our innovative spirit, a triumph of our relentless search for solutions.
We don't stop at materials, though. Proper design, maintenance, and protective measures are essential for guaranteeing the structural integrity and longevity of our marine construction projects. These aspects reveal our analytical approach, our commitment to meticulous planning, and our dedication to preserving what we've built.
Marine construction is a proof of man's ingenuity and resilience. As we grapple with the challenges of constructing in marine environments, we're creating structures that stand as monuments to our innovative spirit, analytical minds, and tenacity. We're not just building structures; we're building legacies.
Importance of Corrosion Resistance
Building on our understanding of marine environments and their unique challenges, we now turn our attention to the importance of corrosion resistance, particularly in the domain of steel formwork.
Corrosion resistance is not just a critical feature in marine construction; it's a necessity. The exposure to saltwater and harsh environmental conditions could lead to rapid deterioration of the formwork if it doesn't possess high corrosion resistance.
Materials such as stainless steel or galvanized steel are often employed due to their high corrosion resistance. Such materials guarantee the structural integrity of the formwork, leading to safer and more durable structures.
Furthermore, regular maintenance and inspections are vital. By identifying and addressing corrosion issues promptly, we can prevent minor issues from escalating into major structural problems.
Design considerations also play a pivotal role. For instance, incorporating proper drainage systems minimizes water exposure, thereby prolonging the lifespan of steel formwork.
Lastly, consulting professionals with specialist knowledge in marine construction can provide invaluable guidance on corrosion resistance strategies.
To summarize, here's a table highlighting the key points:
Key Point | Explanation |
---|---|
Material Choice | Use of high-quality corrosion-resistant materials like stainless or galvanized steel |
Regular Maintenance | Regular inspections and prompt response to corrosion issues |
Design Considerations | Incorporation of features like drainage systems to minimize water exposure |
Professional Consultation | Engaging experts in marine construction for guidance |
Necessity | Corrosion resistance is not optional but essential in marine construction |
In essence, corrosion resistance is fundamental to the success and longevity of marine construction projects. It's not just about building structures, but building them to last.
Types of Formwork Materials
Exploring the domain of formwork materials, it's evident that the choice hinges on several factors, including corrosion resistance, durability, and suitability for marine environments. We've found that steel, particularly stainless steel or galvanized steel, is a trusted choice. It commands respect due to its high corrosion resistance, a quality indispensable in the hostile conditions of marine construction.
Aluminum also stakes a claim in this arena, offering lightweight and durable formwork materials. Its ability to withstand marine conditions without adding significant weight to structures gives it a noticeable edge. Nevertheless, while aluminum and steel have their merits, they aren't the only players in the game.
Wood, despite its vulnerability to water damage and deterioration, still finds a place in some marine construction projects, although less frequently. Its use requires careful consideration and strategic implementation to curb the inherent risks associated with its susceptibility to the marine environment.
Moreover, the emergence of composite materials like fiberglass-reinforced plastics has added a new dimension to marine construction. These materials expertly balance strength with corrosion resistance, making them a potent contender for marine applications.
Lastly, we can't overlook the role of polymer formworks. Their versatility and resistance to marine conditions make them a feasible choice for specific construction needs. They offer an innovative solution that pushes the boundaries of traditional formwork materials.
Steel Formwork: Advantages
Shifting our focus to the advantages of steel formwork reveals its high durability and strength as a prime asset in withstanding the harsh realities of coastal and marine conditions. It's not just about its physical robustness; its resilience lies in its ability to resist corrosion, ensuring longevity and structural integrity in marine environments. We're talking about a material that doesn't just survive but thrives in the face of adversity, a true proof of its versatility.
Steel formwork is the quintessential framework for concrete structures like retaining walls and piers in coastal construction projects. It's the backbone that provides the necessary stability, the silent support that holds everything together. With its strong and unwavering presence, it becomes an indispensable ally in the face of challenging marine conditions, offering a level of dependability that's hard to beat.
But it's not just about strength and stability. Steel formwork brings an element of adaptability to the table, making it suitable for various applications in architectural concrete projects near water bodies. From small-scale projects to large-scale structures, steel formwork bends but doesn't break under the pressure, delivering results that meet the most stringent project requirements.
Another significant advantage of steel formwork is its customizability. It can be tailored to meet the unique needs of marine construction projects, offering a level of flexibility that's as inspiring as it's practical. It's not just about building structures; it's about building solutions, about finding the perfect balance between functionality and aesthetics, between strength and flexibility. And that, fundamentally, is the power of steel formwork.
Wood Formwork: Limitations
While steel formwork showcases impressive resilience in marine construction, the limitations of wood formwork in such challenging environments can't be ignored. Despite its wide use in traditional construction, wood formwork struggles in marine conditions. Its susceptibility to water damage and decay is a significant concern. Unforgiving moisture levels in these environments speed up the deterioration process, impacting the formwork's structural integrity.
In marine construction, we're dealing with structures that must stand the test of time. However, the use of wood formwork can compromise this longevity. High moisture levels accelerate the decay process, reducing the lifespan of the formwork. This leads to frequent maintenance and replacement needs, driving up costs and construction timelines.
Moreover, the degradation of wood formwork doesn't just affect the structure's longevity, but also its quality and safety. The instability caused by water damage can lead to concrete flaws, posing a threat to the overall safety of the structure. Therefore, the use of wood formwork in marine construction can result in high-risk scenarios, where the stability of the structure is compromised.
These limitations clearly show that wood formwork isn't an ideal choice for marine construction. It's then that we look towards alternatives, like steel, that offer improved corrosion resistance and durability. In our quest for liberation from the constraints of traditional construction methods, we must recognize and address the limitations of wood formwork to secure the safety, quality, and longevity of our marine structures. In doing so, we're not just building structures, but we're building a safer and more sustainable future.
Examining Drained-Lined Formwork
Diving into the world of drained-lined formwork, we find an innovative solution that presents promising results in the battle against corrosion in marine construction. This cutting-edge technique has shown significant improvements in corrosion resistance and bonding strength in concrete structures. It's an exciting development in the field, offering substantial benefits regarding durability and life-span of marine infrastructures.
Analyzing the process, we observe that the concrete poured using drained-lined formwork exhibits lower mass loss and higher tensile strength. This isn't just a minor enhancement; it's a significant leap forward in concrete durability. Increasing tensile strength and reducing mass loss leads to a more robust and long-lasting structure, capable of withstanding the harsh marine environment.
Furthermore, we've noticed that drained-lined formwork reduces chloride content in concrete. This improvement not only enhances corrosion resistance but also contributes to a protective environment for reinforcing steel, which we'll explore more in our next discussion. It's evident that this innovative formwork provides a viable solution to the significant issue of corrosion in marine construction.
Effects on Reinforcing Steel
Stepping into the domain of reinforcing steel, we find that corrosion, particularly in marine environments, becomes a formidable adversary due to the presence of chlorides from saltwater. This relentless foe infiltrates the concrete, reaching the reinforcing steel and gradually inflicting corrosive damage over time. The result? A weakened structure with compromised integrity, something we can't afford in marine construction.
Now, how do we combat this adversary? It's all about prevention. Our first line of defense is ensuring an adequate concrete cover thickness. This protective layer serves as a barrier, shielding the reinforcing steel from the chloride onslaught. But it's not just about thickness, it's also about quality – a poorly mixed or porous concrete cover might as well be an open invitation for corrosion.
Moreover, we can't just rely on concrete cover alone. We need to employ other protective measures, like coatings or corrosion-resistant steel. These aren't mere add-ons; they're essential elements in our strategy against corrosion. Coatings, for instance, serve as an extra layer of armor, warding off the corrosive effects of chlorides. On the other hand, using corrosion-resistant steel means we're choosing a material that inherently stands up against corrosion. It's like choosing a warrior who's already trained to fight the battle.
Corrosion Resistance Tests
As we strategize our defense against corrosion, we mustn't overlook the role of corrosion resistance tests, which meticulously assess the ability of formwork materials to withstand the harsh marine environments. These tests are crucial in determining the suitability of formwork materials for marine construction projects. By exposing sample materials to corrosive elements such as saltwater and seawater, we gain valuable insights into their durability and longevity.
There are several testing methods employed to evaluate the corrosion resistance of formwork materials. These include:
- Standard exposure tests: Here, formwork samples are exposed to corrosive elements for a set period, and the extent of corrosion is then assessed.
- Accelerated corrosion tests: These simulate long-term exposure to corrosive environments in a shorter time frame.
- Electrochemical tests: These use electrical currents to accelerate corrosion, providing rapid results.
These tests provide a wealth of data, allowing us to make informed decisions about the most suitable materials for marine construction projects. We don't just want to survive; we want to thrive in our endeavors. And to do that, we need to be smart, innovative, and meticulous in our approach.
Corrosion resistance tests are a critical part of the solution, giving us the power to predict and plan for the effects of corrosive marine environments. Through these tests, we can choose materials that not only withstand the harsh conditions but also provide longevity to our marine structures. Essentially, these tests are our strong allies in our continuous battle against corrosion.
Analysis of Test Results
When we investigate the analysis of corrosion resistance test results, it becomes clear just how effectively steel formwork, when treated with proper corrosion-resistant coatings, can withstand the harsh marine environments. The data is unequivocal: steel formwork, provided it's meticulously coated and maintained, exhibits remarkable resilience against corrosion. This isn't just a minor advantage; it's a game-changer in marine construction.
Our analysis of the data demonstrates that the durability and longevity of steel formwork in coastal and marine construction projects are substantially enhanced by the application of these specialized coatings. The numbers don't lie, and they show a promising trend. When we compare steel formwork with other materials under the same corrosive conditions, steel consistently outperforms, maintaining its structural integrity and performance with little to no degradation over time.
But let's explore further. It's not just any steel that can achieve these results. Our research suggests that the quality of the steel plays a significant role. High-quality steel, coupled with robust, corrosion-resistant coatings, emerges as the frontrunner in this race against the elements.
In other words, it's a two-pronged approach to combating corrosion in marine formwork: superior steel quality and effective protective coatings. The combination of these two factors yields a formwork material that's not just resistant to corrosion, but practically immune to it.
Best Practices for Resistance
To guarantee the high-quality corrosion resistance of marine construction formwork, it's essential to adopt several best practices, starting with the selection of corrosion-resistant steel such as stainless steel or galvanized steel. This fundamental step ensures that the formwork exhibits a prolonged lifespan, even when exposed to harsh marine environments.
One can't underestimate the significance of regular maintenance and inspection. These proactive measures enable us to identify and address corrosion issues on time. Detecting the early signs of corrosion and taking swift action can greatly extend the life of formwork and prevent costly replacements in the future.
Design considerations also play a pivotal role in enhancing corrosion resistance. Effective drainage systems, for instance, minimize water exposure thereby reducing the chances of corrosion. Here is a concise list of some best practices:
- Utilizing stainless steel or galvanized steel for formwork construction.
- Conducting frequent maintenance and inspection to promptly detect and address corrosion issues.
- Incorporating effective drainage systems in design plans to minimize water exposure.
In addition, consulting professionals with expertise in marine construction can provide invaluable guidance. Their insights can help us mitigate corrosion risks and ensure the durability of our formwork.
Frequently Asked Questions
What Is the Most Commonly Used Material for Formwork?
We're often asked about the most commonly used material for formwork. It's steel, without a doubt. It's highly chosen for its strength and durability.
Not just any steel, though. We're talking about stainless and galvanized steel, tailored to resist corrosion. It's ideal for building sturdy structures like retaining walls and piers.
We can adjust it to meet specific project needs. So, for those seeking liberation from subpar materials, steel is your reliable solution.
Which Concrete Is Used in Marine Environment?
We've found that marine-grade concrete, infused with additives like fly ash or slag, is commonly used in marine environments. It's designed to resist chloride penetration, protecting the steel reinforcement from corrosion.
High-performance concrete mixes with low water-cement ratios are also favored for their superior strength and durability. Additionally, special admixtures, such as corrosion inhibitors, are often added for extra protection against harsh marine conditions.
Should the Formwork Be Strong Enough to Withstand the Concrete Which Shall Be Cast in Place?
Certainly, we must guarantee that our formwork's strength surpasses the pressures exerted during concrete casting. It's crucial to prevent deformations, bulges, or even collapses.
This not only enhances safety on-site but also contributes to the final structure's quality and durability. We're being innovative and analytical by making sure our formwork meets or exceeds design specifications.
It's a liberating approach, knowing we're building with strength and integrity.
What Are the Different Types of Formwork?
We've got numerous types of formwork, each with its own merits.
There's traditional timber formwork, a cost-effective and versatile option.
Steel formwork, on the other hand, boasts strength and durability.
Aluminum formwork is lightweight and reusable, making for quick construction.
Finally, plastic formwork, also lightweight and easy to handle, can be used multiple times.
Each type offers unique benefits, and it's crucial to make an informed choice.
Conclusion
In wrapping up, we've explored the essential role of formwork in marine construction, especially its corrosion resistance. Analyzing both steel and wood formwork, it's evident that steel offers more advantages.
However, conducting corrosion resistance tests and analyzing their results is crucial. We believe in adopting best practices to enhance resistance, ensuring longevity of our marine structures.
Innovation and a detailed approach are key in tackling corrosion, a persistent challenge in marine construction.