Formwork for Complex Concrete Shapes: Techniques and Case Studies
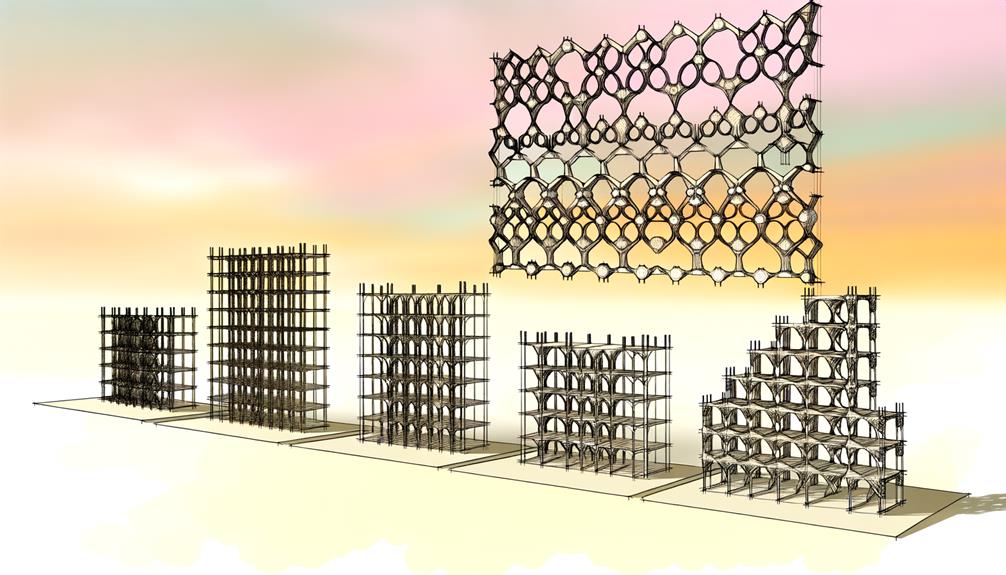
Formwork for complex concrete shapes involves innovative techniques such as flexible formwork and advanced materials like plastic and fabric. Material choice has a major impact on the construction drumbeat, ensuring strength and the desired finish. Numerous real-world case studies demonstrate the game-changing potential of modern methods. Future trends include recyclable formworks and enhanced automation through 3D printing. It's absolutely essential to detect errors early, ensuring robust construction. These upfront precautions saved considerable time and expense in the projects we'll explore next. Let's move on to reveal how these techniques have been successfully implemented.
Understanding Formwork Types
Diving into the world of formwork types, it's clear that the choice between traditional, flexible, or recyclable systems hinges on multiple factors such as the project's required geometry, construction demands, and the degree of customization needed. Traditional formwork, usually employing wood and metal components, is ideal when regular geometries are desired. This system, while sturdy and reliable, offers limited flexibility regarding design innovation.
On the other hand, flexible formwork systems are a game-changer, enabling us to create non-standard shapes and geometries. Innovative techniques, such as fabric formwork and digitally fabricated formwork, have revolutionized the way we build complex concrete structures. Reduced material and labor costs are added advantages of these systems, making them a popular choice for projects requiring a high level of customization.
The third type, recyclable formwork systems, is a nod to the growing need for sustainability in the construction sector. By using environmentally-friendly materials and digital fabrication methods, this system marries the virtues of ecological responsibility with the practicality of efficient construction.
It's important to note that the choice of formwork type isn't a one-size-fits-all solution. Each type has its strengths and constraints, and the decision largely hinges on the project's unique demands. How complicated is the shape? How much customization is needed? What're the construction requirements? These questions help guide us to the most suitable formwork type, liberating us from the constraints of standard designs and paving the way for innovative, sustainable construction.
Designing Effective Formwork
When it comes to crafting complex concrete shapes, the design of our formwork plays a pivotal role, as it not only determines the precision of the final product but also its structural integrity. It's not just about selecting the right formwork, but understanding how it can be manipulated to create the desired geometry, and ensuring the surface quality of our complex structures meets the highest standards.
The strength, durability, and flexibility of the formwork material are all critical factors in our design process. However, this doesn't mean we're confined to traditional approaches. On the contrary, we're constantly exploring advanced techniques to push the boundaries of what's possible. We've seen significant success with fabric formwork and digitally fabricated systems, particularly for non-standard geometries. These innovations allow us to mould concrete into shapes that would have been unthinkable with conventional methods.
That being said, there's no one-size-fits-all solution. Each project is unique, and our formwork design must be tailored to meet its specific requirements. We're not just building structures; we're creating works of art. This requires a deep understanding of the property of the formwork material and the concrete, as well as the interaction between the two. It also necessitates a willingness to experiment, to iterate, and to learn from our successes and failures.
Case studies of successful complex concrete shapes underscore the importance of good formwork design. They serve as a validation to our ingenuity and craftsmanship, and a reminder that with the right formwork, even the most complicated designs can be realized. If there's one thing we've learned, it's that effective formwork design is the cornerstone of any complex concrete project.
Importance of Formwork Materials
The selection of formwork materials is a decision of paramount importance, impacting the quality, finish, and durability of our concrete structures. We can't emphasize enough how crucial it is to make an informed choice, considering the specific needs of each project. Timber, plywood, steel, aluminum, and plastic, each offer unique properties that can be utilized to achieve optimum results.
Timber and plywood are traditional choices, but they may not provide the water resistance and durability that steel and aluminum offer. These metals, strong and resilient, are well-suited for structures that need to withstand harsh environmental conditions. However, they're not always the best option. We must balance durability with factors like cost, weight, and ease of use.
This is where lightweight materials like plastic come in. Plastic formwork panels are easy to handle, clean, and are particularly suitable for small projects with repetitive tasks. They may not have the same lifespan as metal, but their ease of use can lead to significant time and cost savings.
Moreover, the right formwork material can prevent construction issues like honeycombing and guarantee a smooth concrete surface. It's not just about the immediate construction process; it's also about the long-term performance and aesthetics of our structures.
Case Study: Traditional Formwork System
In examining numerous construction projects, we've found that traditional formwork systems, primarily incorporating wood and metal components, continue to hold a strong position in the industry due to their reliability, especially when dealing with structures of regular geometries. Despite the emergence of innovative technologies, these systems remain steadfast, exhibiting a strength rooted in their simplicity and durability.
These traditional systems, known for their manual craftsmanship and well-established fabrication techniques, aren't just about sticking to the old ways. They're about harnessing the power of tried-and-true methods, coupled with the assurance of known outcomes. This isn't to say they're void of challenges. They often require skilled labor, but the trade-off is a robust, reliable structure that can withstand the test of time and environmental stressors.
We've observed their effectiveness across various construction applications. Their versatility, whether for a residential building or a multi-story commercial complex, is commendable. Despite the labor-intensive nature of traditional systems, their benefits, from cost-effectiveness to the predictability of results, make them an attractive choice for many in the industry.
In our quest for liberation, we mustn't overlook the value of tradition. The beauty of traditional formwork lies in its ability to deliver reliable, durable structures with regular geometries, reflecting the harmonious blend of art and engineering. As we continue to explore more complex concrete shapes, we must remember: innovation and tradition aren't mutually exclusive but can coexist, each enhancing the other's strengths.
Case Study: Flexible Formwork System
Shifting our focus to flexible formwork systems, we find they're revolutionizing the construction industry by enabling the creation of complex, non-standard concrete shapes while reducing material and labor costs. This innovative approach offers unprecedented flexibility in design, fostering the realization of intricate geometries and ground-breaking architectural structures.
Examples of such techniques include fabric formwork and digitally fabricated formwork. The former utilizes flexible, tensioned fabrics held by a rigid frame, allowing the concrete to naturally shape itself under the forces of gravity. Digitally fabricated formwork, on the other hand, involves the use of computer-aided design and manufacturing technologies to create customizable formwork molds.
A clear picture of these techniques' potential becomes evident when we examine their successful implementation in construction projects. These case studies underscore the versatility and cost-effectiveness of flexible formwork systems in achieving unique concrete shapes.
To illustrate, consider the following table detailing two distinct projects that utilized flexible formwork systems:
Project | Formwork Technique Used |
---|---|
Project 1 | Fabric Formwork |
Project 2 | Digitally Fabricated Formwork |
In each case, the use of flexible formwork systems not only enabled the creation of unique concrete shapes but also enhanced structural efficiency and optimized material usage. These cases demonstrate that the adoption of such innovative systems can lead to a significant liberation in design potential, challenging the conventional constraints of concrete construction.
Case Study: Recyclable Formwork System
While embracing the transformative power of flexible formwork systems, we're also witnessing the rise of a new player in the formwork arena: the recyclable formwork system. This system is a paradigm shift, focusing on reducing waste by using environmentally-friendly materials. It's an innovative approach to sustainable construction practices, currently in its early stages of development, but showing promising potential.
In examining the recyclable formwork system, three key aspects stand out:
- Material Efficiency: These systems use sustainable materials, aiming to reduce waste and enhance construction efficiency. It's a leap towards an eco-friendly construction process, seeking liberation from wasteful traditional practices.
- Digital Fabrication Techniques: Incorporating techniques like CNC milling, the recyclable formwork system is designed for non-standard geometries. This opens up opportunities for unique, innovative structural solutions.
- Contribution to Future Construction Trends: By focusing on sustainability and material efficiency, the recyclable formwork system is poised to influence the future of construction technology significantly.
However, the practical application of recyclable formwork systems is still limited. Despite the potential benefits, the industry has been slow to adopt this eco-friendly alternative, possibly due to a lack of understanding or apprehension about the new technology.
Nonetheless, the recyclable formwork system represents a new frontier in the quest for sustainable construction. It's a bold step towards changing how we think about formwork, moving away from traditional methods and embracing innovative, sustainable solutions. As we continue to explore its potential, we're confident that this system will play a vital role in shaping the future of our industry.
Future Trends in Formwork Construction
Looking ahead, we see the landscape of formwork construction being reshaped by emerging trends such as the use of reusable materials, increased automation, and the integration of advanced robotics, particularly in the domain of 3D printing. These trends aren't simply passing fads, but rather they signify a strategic shift towards greater efficiency, sustainability, and practicality in the industry.
Delving into the details, we notice that the emphasis on reusable materials is driven by the dual objectives of cost-effectiveness and environmental responsibility. As we endeavor to meet growing construction demands while minimizing our ecological footprint, the adoption of reusable formwork materials becomes an inevitable choice. It's a smart move that combines economic prudence with environmental stewardship.
Similarly, the trend towards increased automation is a response to the need for speed, precision, and consistency in formwork construction. We're witnessing a shift from manual, labor-intensive processes to automated ones that can deliver higher output with fewer errors and less waste. It's about leveraging technology to enhance productivity and quality in formwork construction.
The integration of robotics, particularly in 3D printing, is perhaps the most revolutionary trend. It's a game-changer that's opening up new possibilities for creating complex concrete shapes with unprecedented ease and accuracy. By harnessing the power of 3D printing technology, we're now able to construct formworks that were once deemed impossible or impractical.
Formwork Errors and Solutions
Despite the many advancements in formwork construction, it's important to acknowledge that a significant number of projects still grapple with formwork errors, which can lead to structural defects, unwelcome delays, and serious safety hazards. Common errors include misalignment, inadequate bracing, and improper connections—all of which compromise the integrity and quality of the concrete structure.
To combat these challenges, we propose a threefold solution:
- Thorough Inspection: Rigorous and regular inspections can identify problems early, allowing for timely correction. This includes confirming the right alignment and proper connections, as well as checking for adequate bracing.
- Timely Corrections: Once an error is spotted, immediate action is required. Delaying corrections not only prolongs the construction process but also raises safety issues and could potentially escalate the problem.
- Proper Communication: Clear and open communication among the construction team is essential. Everyone should understand their roles, responsibilities, and the importance of accuracy in formwork construction.
Additionally, implementing quality control measures and regular monitoring can prevent formwork errors. Addressing these errors promptly and systematically is crucial to ensure the overall success of the project. This approach liberates us from the shackles of unnecessary errors and delays, paving the way for a smooth, efficient, and safe construction process.
Innovations in Formwork Technology
In the realm of concrete construction, we're witnessing a surge of innovation as 3D printing technology and other advancements revolutionize formwork, providing precise, efficient solutions for even the most intricate structures. This cutting-edge technology is leading to the fabrication of intricate formwork designs with unmatched accuracy and speed, thereby transforming the way we approach concrete construction.
We're also exploring unconventional formwork materials such as resin-bonded sand and ice for crafting intricate concrete shapes. These materials introduce a new level of flexibility and creativity, allowing us to overcome previous design limitations. Their use represents a bold step towards freeing the construction industry from traditional constraints.
Significant advancements are also noticeable in insulation techniques. The emergence of Insulating Concrete Forms (ICFs) is a confirmation of this progress. ICFs not only simplify the formwork process but also enhance thermal insulation and energy efficiency, offering a sustainable alternative to conventional methods.
CNC milling is another innovation we're harnessing to create unique formwork solutions. This technology allows us to cater to challenging concrete shapes, bringing life to designs that were once considered unattainable.
Lastly, our dedication to sustainability is propelling us to research environmentally friendly formwork materials. This pursuit aligns with our vision of an efficient and eco-friendly concrete construction industry, setting a new standard for future projects.
In essence, these innovations in formwork technology are pushing the boundaries of what's achievable, ushering in an era of creativity, efficiency, and sustainability in concrete construction. As we continue to evolve, we look forward to the freedom that these advancements promise.
Frequently Asked Questions
What Are the Different Types of Concrete Formwork?
We've explored various types of concrete formwork. Traditional systems use timber, steel, or plywood.
For complex shapes, flexible formwork like fabric or digitally fabricated systems are ideal.
We're seeing recyclable systems, using eco-friendly materials like CNC-milled sand, gaining popularity.
Aluminum, providing a smooth concrete finish, works great for curved structures.
What Type of Formwork Material Which Is Used for Small Concrete Structures or for Complex Portions of the Structure?
We often utilize timber formwork for small structures due to its cost-effectiveness and flexibility. For complex portions, plywood offers strength and versatility. Metallic formwork, like steel and aluminium, is ideal for intricate shapes, while plastic panels are great for repetitive tasks.
We're not limited to one type – combinations of these materials can be used to meet specific needs. It's all about choosing what's best for the project at hand.
What Is Formwork for Special Structure?
We perceive formwork for special structures as customized molds designed to support uniquely shaped concrete elements.
It's not just about creating molds, but precision in engineering and craftsmanship to withstand the concrete's weight during construction.
Sometimes, we use advanced materials like fiberglass or carbon fiber for efficiency.
We also consider load distribution and alignment accuracy.
It's an innovative process that brings architectural visions to life.
What Are the Classification of Formwork Based on Shape?
We've identified two main classifications of formwork based on shape: traditional and flexible. Traditional formwork is utilized for standard shapes like columns, beams, and slabs.
On the other hand, flexible formwork adapts to complex geometries and irregular structures, offering custom solutions.
Conclusion
In summary, we've seen that formwork is essential in crafting complex concrete shapes. As we've observed in our case studies, the choice of formwork system – traditional, flexible, or recyclable – can greatly impact the final product.
Looking ahead, we predict new innovations and trends will continue to shape the formwork construction field. To avoid costly errors, it's important to understand the materials and design techniques.
Let's keep exploring and innovating in this captivating field.