Formwork for Cold Weather Concreting: Precautions and Procedures
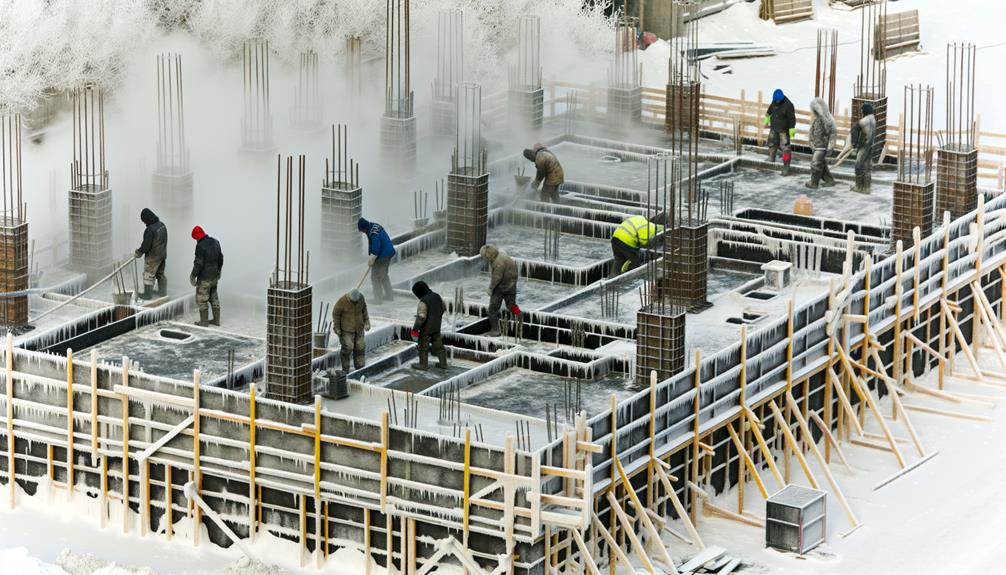
In cold weather concreting, we must take strategic precautions to ensure best results. Ensuring formwork surfaces are free from ice and snow prevents bonding issues. Using insulated formwork and heating systems helps sustain concrete temperature above 5°C. It's essential to constantly monitor and adjust the concrete mix design, keeping climatic conditions in mind. Tackling cold joints, maintaining cleanliness of surfaces, and using bond breakers are important. Advanced curing techniques bolster concrete strength. Ground Penetrating Radar (GPR) plays a pivotal role in structural assessment. Stick with us, we've got plenty more strategies to unfold!
Understanding Cold Weather Concreting
To fully grasp cold weather concreting, it's essential to understand that it involves placing and curing concrete in temperatures below 5ºC, a condition that significantly slows the development of concrete's strength. This slowdown is a pivotal factor in determining the longevity and integrity of constructions built in colder climates.
Different categories of cold weather include ambient temperatures below 5ºC, minor frost, and severe frost. Each category presents unique challenges for the concrete curing process. Minor frost, for example, can still allow the concrete to cure at a slower pace, while severe frost can completely halt the process, leading to structural weaknesses. It's our responsibility to anticipate these conditions and plan our construction processes strategically to mitigate potential risks.
Formwork removal timing in cold weather is another critical aspect that affects the strength and stability of the concrete. If we remove the formwork prematurely, the concrete may not have reached sufficient strength, making the structure vulnerable to the cold and potentially leading to structural failure. On the other hand, leaving the formwork in place for too long can impede construction progress. A delicate balance must be struck to secure structural integrity without slowing down the progress.
Protection measures like frost blankets and insulated formwork are necessary to prevent the freezing of fresh concrete. These measures provide much-needed insulation that helps maintain a steady temperature within the concrete, allowing it to cure effectively despite the cold exterior conditions. It's through these calculated, strategic decisions that we can free ourselves from the challenges posed by cold weather concreting.
Precautions for Successful Formwork
Moving on from understanding the challenges of cold weather concreting, let's now focus our attention on the necessary precautions we must take for successful formwork in these conditions.
First and foremost, we must guarantee that formwork surfaces are free from ice and snow. This is essential because any presence of these elements can cause bonding issues with the concrete, compromising the overall integrity of our project.
Next, we should consider using insulated formwork. This plays an important role in maintaining the concrete temperature above 5°C during placement. By doing so, we're ensuring that the concrete won't freeze before it has had a chance to properly set, thereby upholding the structure's stability.
In addition, we can't overlook the implementation of heating systems or enclosures. These serve as a protective measure for both the formwork and the concrete, shielding them from freezing temperatures that could potentially cause damage.
Along the same lines, it's essential to properly design and install our formwork in a way that can withstand the harsh conditions brought about by cold weather. This not only prevents damage but also ensures the formwork's functionality isn't compromised.
Protection Measures for Concrete
Protecting fresh concrete against the harsh cold is essential to prevent freezing, which can result in catastrophic failure. To guarantee the strength and resilience of the concrete, it's vital that we maintain its temperature at delivery above 5ºC. This isn't just a critical step, but a crucial factor that can greatly impact the concrete's strength development.
Choosing the right protection tools is equally important. We can't underestimate the significance of insulated formwork and frost blankets, which provide a shield against the biting cold. These materials work to insulate the concrete, creating a warm environment that fosters the necessary chemical reactions within the mixture.
However, protection isn't confined to the concrete alone. All surfaces that come into contact with the concrete, including sub-bases and equipment, must be free from ice and snow. We must make sure that these surfaces are prepped adequately to receive the concrete. This requires a meticulous and strategic approach, especially when dealing with large-scale projects.
In severe frost conditions, we need to ramp up our precautions. These situations demand a more aggressive approach to ensure the durability of the concrete. We can't afford to be complacent when the weather takes a turn for the worse. Instead, we must adapt, strategize, and make sure that our protective measures are up to the task.
Dealing With Ice and Snow
When handling ice and snow, we must guarantee that they're completely cleared from both formwork and rebar surfaces, as this step is essential to maintaining proper adhesion and preventing cold spots in the concrete. We can't stress enough the importance of this process, as neglecting it can lead to structural integrity issues and potential bonding problems with the concrete.
To achieve this, we should devise a strategic plan to regularly inspect and clean these surfaces. This is where a detail-oriented approach becomes vital, ensuring all areas, even the most inaccessible, are free of ice and snow.
Insulating formwork becomes a necessary measure to tackle ice and snow buildup. This step helps maintain a consistent temperature, preventing differentials that could adversely affect the curing process. The insulation should be of high quality and installed correctly to provide effective protection against the cold weather conditions.
In addition, using heating methods to warm formwork can alleviate the challenges of cold weather concreting. This proactive approach helps maintain the best concrete placement temperatures, enabling us to work efficiently even in harsh conditions. However, we must carefully control these methods to avoid overheating, which could lead to other problems.
Controlling Temperature Gradient
To prevent cracking and diminished strength in the concrete, it's essential that we actively manage temperature gradients, ensuring they don't fluctuate rapidly within the formwork. We must maintain a vigilant watch on the temperature differentials, as they can lead to compromised performance. One of our key strategies in this regard is insulation, which is a simple yet effective method of maintaining consistent temperatures during the curing process.
By wrapping our formwork in insulating materials, we create a consistent thermal environment for the concrete, preventing rapid cooling or heating of surfaces. The result? Peak strength and durability. But remember, it's not just about the insulation. We must also closely monitor the temperature within the formwork, using tools such as embedded temperature sensors to accurately gauge the gradient.
This level of detailed monitoring allows us to react swiftly to any changes, ensuring we maintain a stable temperature differential and prevent any potential cracking or strength reduction. It's a proactive approach, requiring constant vigilance and strategic adjustments, but one that assures the quality of our concrete structures.
Addressing Low Concrete Strength
Building on our understanding of temperature gradient control, we now turn our attention to another pressing concern – low concrete strength, which often plagues cold weather concreting. This shortcoming can result from freezing temperatures affecting the hydration and curing processes, leading to structural instability and compromised durability.
Cold temperatures slow down the early strength development of concrete, requiring special protective measures. Without these precautions, we're risking the integrity of our structures. Therefore, we need to be strategic and proactive in our approach. Let's explore some of the solutions that can mitigate this issue.
Firstly, we must consistently monitor and adjust our concrete mix designs to counteract the impact of low temperatures on concrete strength. This isn't just an important task, but a continuous process that demands our utmost attention and diligence. It involves analyzing the mix proportions and making necessary modifications while being mindful of the specific climatic conditions.
Secondly, we can't underestimate the role of proper curing methods. These aren't only essential to prevent low concrete strength issues but also to safeguard the overall durability of the structures. Conventional methods may not suffice in cold weather conditions. We must explore and implement advanced curing techniques that can effectively sustain the strength development process.
Lastly, protective measures like insulation and heated enclosures can safeguard our concrete from the harsh cold. By combining these strategies, we can effectively address the challenge of low concrete strength in cold weather concreting. Remember, our goal isn't just to build structures. It's to build durable, long-lasting, and safe structures that stand the test of time and weather.
Tackling Cold Joints Issues
While addressing low concrete strength, we must also tackle another common problem in cold weather concreting – the issue of cold joints. Cold joints occur when fresh concrete is placed against hardened or cured concrete. Neglecting this issue can lead to structural weakness, compromising the integrity of the entire project.
To effectively tackle cold joint issues, we must consider a strategic approach. Here, preparation is key. Proper preparation of the joint surfaces is critical to prevent cold joint formation. This involves ensuring that the hardened concrete surface is clean and free from any materials that could hinder the bonding process.
Nevertheless, even the most thorough preparation doesn't always guarantee a perfect bond. To further improve cold joint performance, we can employ other techniques, such as:
- Utilizing bond breakers: These substances prevent adhesion between the new and old concrete, allowing independent movement and reducing the risk of cracks.
- Applying joint sealing compounds: These materials fill the gap between the old and new concrete, helping to create a stronger bond.
- Adapting construction practices: Techniques such as continuous pouring can significantly minimize cold joint issues.
Addressing cold joint issues is a liberating approach in cold weather concreting. This not only enhances the strength and durability of our structures but also empowers us to take on construction projects during the colder months with confidence. With these strategies, we're no longer at the mercy of the weather but instead, harnessing it to our advantage. Let's apply them and take our cold weather concreting to greater heights.
Utilizing GPR in Structural Assessment
In the domain of structural assessments, especially in cold weather conditions, we've found Ground Penetrating Radar (GPR) to be an indispensable tool for inspecting and evaluating concrete structures. This non-destructive testing method uses electromagnetic waves to detect rebar, voids, and anomalies within the concrete.
Let's simplify the advantages and common uses of GPR with a handy table:
Advantages of GPR | Common Uses of GPR |
---|---|
Non-destructive method | Bridge inspections |
Provides detailed information | Road assessments |
Offers real-time imaging | Structural evaluations in cold weather |
GPR provides us with critical data about concrete thickness, reinforcement layout, and potential defects. Its real-time imaging capability gives us a live peek into the subsurface structures, making it a valuable tool for proactive structural assessments.
In our quest for liberation from the conventional constraints of structural assessment, GPR empowers us with the ability to detect and address issues before they escalate. It allows us to strategize our approach, making our work more efficient and effective.
For instance, when dealing with cold weather concreting, GPR helps us identify cold joints, ensuring seamless continuity in the concrete structure. It's a tool that not only enhances our work but also contributes to building safer and more reliable structures.
Frequently Asked Questions
What Precautions Are Required for Cold Weather Concreting?
We've got to keep our concrete above 5ºC when it's delivered for cold weather concreting. Using frost blankets and insulated formwork protects our fresh concrete from freezing. It's essential we clear formwork, sub-bases, and equipment from ice and snow to avoid damage.
In severe frost, we may need to delay concreting or use heated concrete. We can't forget that effective curing practices are important for maintaining our concrete's durability in cold weather.
What Is the British Standard for Cold Weather Concreting?
We've found that the British Standard for cold weather concreting is BS 5838. It's a vital guide that lays out procedures and precautions for concreting in low temperatures.
We can't stress enough how important it's to follow these guidelines. Not only does it guarantee the quality and durability of the concrete, but it also helps to mitigate risks associated with cold weather concreting.
We're all for liberation, but in this case, compliance is key.
What Should Be Done Before Placing Concrete in Formwork?
Before we pour concrete, we've got to make certain our formwork is free from ice, snow, and other contaminants.
We'll monitor the formwork's temperature to prevent concrete from freezing. Using insulated formwork or heating elements, we maintain the temperature above freezing.
We ensure our formwork is secure and aligned, avoiding misshaping or leakage. In extreme cold, we'll utilize frost blankets or temporary enclosures.
It's all about the prep work.
What Is the Problem in Cold Weather Concreting?
We've identified that cold weather concreting presents challenges like freezing of water in fresh concrete and slowed strength development. This affects the concrete's durability and stability.
It's vital that we keep the concrete above 5°C for at least 48 hours to avoid freezing damage. We also need to carefully time the removal of formwork during cold weather and utilize protective measures like frost blankets and insulated formwork.
Conclusion
In managing cold weather concreting, we've discovered the importance of careful formwork, protective measures, and temperature control.
We've also tackled low strength issues, cold joint problems, and the value of GPR.
By taking precautions and following strategic procedures, we can successfully pour concrete even in the harshest winter conditions.
It's all about understanding the challenges and using smart, innovative strategies to overcome them. Let's keep building, no matter the weather.