Formwork for Beam and Girder Structures: Design Insights
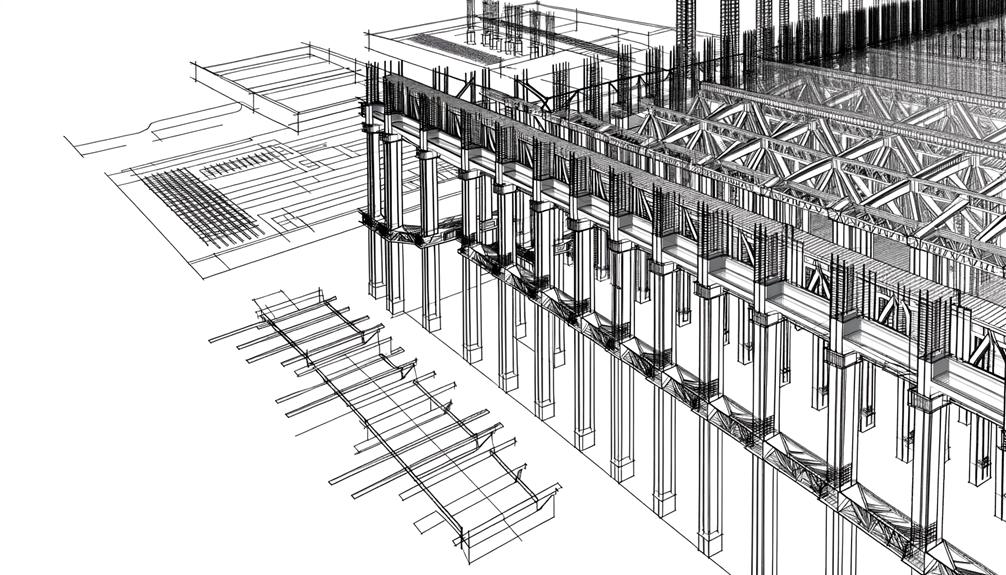
In designing formwork for beam and girder structures, we're primarily focused on selecting the right materials, understanding load-bearing capacity, and ensuring the structural integrity. Beams and girders offer excellent bending stress resistance, and their properties can vary based on the materials chosen, such as plywood, steel, or timber. Neglecting correct support intervals or making design errors can lead to severe consequences like overloading. However, with precise calculations, thorough analysis, and systematic dismantling processes, we can optimize formwork design and avoid potential pitfalls. Moving forward, we'll unwrap more about this fascinating subject.
Understanding Beam and Girder Structures
To fully comprehend the intricacies of beam and girder structures, we must first understand that beams and girders are indispensable elements in formwork systems, providing substantial structural support. These components, often referred to as H-Beams or I-Beams, are deftly designed with an I-section profile, allowing them to withstand bending stresses effectively. Take, for example, the P20 girder, it has a depth of 200mm, bending strength of 5 KNm, and shear strength of 11 KN. These metrics aren't arbitrary but meticulously calculated to optimize formwork design for various construction projects.
Girders offer a level of versatility that's unmatched. They're as comfortable in beam, slab, column, or wall formwork as fish are in water. This adaptability contributes significantly to high-quality and safe construction practices, often being the unsung heroes behind many architectural marvels.
But the power of girders extends beyond their physical strength and flexibility. They represent an innovative approach to construction, a forward-thinking mindset that isn't confined by traditional practices. By understanding and utilizing their potential, we aren't merely constructing buildings; we're crafting a future where our structures are stronger, safer, and more sustainable.
In essence, girders are more than just construction materials; they're catalysts for change, enabling us to break free from outdated methodologies and embrace a liberated approach to construction. We're not just discussing beams and girders here; we're talking about a paradigm shift in how we perceive and engage with the world of construction. Understanding beam and girder structures is the first step on this journey of liberation.
Material Selection for Formwork Design
Delving into the domain of material selection for formwork design, we find it's much like selecting the right tools for a finely crafted masterpiece, where considerations of load capacity, durability, and reusability become paramount. This isn't a one-size-fits-all process; it necessitates a nuanced understanding of the materials at our disposal, their strengths, limitations, and appropriate applications.
Plywood, for instance, is a popular choice due to its cost-effectiveness and versatility. It's able to withstand varying weights and is adaptable across different formwork designs. However, for heavy-duty applications, steel formwork becomes the go-to material. With its high strength and durability, it's equipped to take on the most demanding tasks, offering the reliability needed in large-scale projects.
Yet, weight and corrosion can be a concern with steel. Here's where aluminum formwork shines. It's lightweight, corrosion-resistant, and perfect for repetitive use. It's like the featherweight champion of the formwork world, delivering strength without the bulk.
Now, let's not forget timber. An environmentally friendly choice, it's ideal for smaller projects with limited budgets. It's nature's gift to construction, blending affordability with sustainability.
Clearly, the choice of material in formwork design isn't a trivial matter. It's an intricate dance of balancing project needs with material properties. And it's this dance that determines the efficiency, safety, and success of our construction endeavors. As we liberate ourselves from traditional views, we find that the right material selection can be transformative, turning formwork from mere supports into the spine of our structural achievements.
Importance of Support Intervals
While we've considered the material choices in formwork design, let's now turn our attention to another equally significant aspect – the art of determining support intervals in beam and girder formwork. These intervals, typically determined based on the span length and load requirements of the structure, aren't mere technicalities. They serve as critical pillars of formwork stability and safety during the all-important phases of concrete pouring and curing.
Now, why the emphasis on support intervals? It's because they're the unsung heroes that distribute the load evenly, acting as guardians against structural failures or deformities. If you've ever marveled at a perfectly aligned concrete structure and wondered about the secret behind its precision, seek no further than judiciously calculated support intervals.
The spacing between supports isn't a random number pulled out of a hat. It's a thoughtful calculation, an art born from understanding the relationship between the formwork and the load it's destined to bear. The right balance ensures the formwork's structural integrity and alignment, providing a solid groundwork for the concrete members.
But the importance of support intervals doesn't stop at stability and alignment. They're also key drivers of efficiency and effectiveness in the formwork installation process. Properly calculated intervals streamline operations, saving time, resources, and ultimately, money.
Impact of Design Errors on Structures
Let's now explore how design errors can wreak havoc on the stability and safety of beam and girder structures, causing potential overloading, deflection, or even outright failure of the formwork system. It's not just about the immediate danger these errors pose during construction; they can also compromise the long-term performance and durability of the structure.
Incorrect calculations can lead to miscalculations of the load a structure can bear, resulting in overloading. This overloading can then trigger deflection, where the structure bends under the weight, failing to maintain its shape and integrity. Additionally, if the load distribution isn't adequately considered, localized failures can occur, compromising the entire structural integrity. It's like a chain reaction; one weak link is enough to jeopardize the whole structure.
Furthermore, these design errors can have lasting effects. They can't only affect the immediate construction phase, causing delays and increasing costs, but also impact the long-term performance of the structure. It's a forward ripple effect; a small error now can lead to significant problems down the line. Imagine a building or a bridge that, because of a design error, starts to crumble years after its construction. It's a frightening thought, isn't it?
That's why attention to detail, adherence to standards, and thorough structural analysis are essential in formwork design. We can't afford mistakes; the stakes are simply too high. The key to liberation from these potential hazards lies in diligence, precision, and a deep understanding of the design process and structural principles.
Ensuring Structural Integrity in Formwork
In the world of construction, ensuring the structural integrity in formwork is an essential necessity; it's the foundation upon which the safety and durability of beam and girder structures rest. It's not just about stability but also about creating structures that stand the test of time.
To guarantee the structural integrity of formwork, we must first comprehend the vital role that formwork design plays. It's not just a matter of putting materials together, but a calculated process informed by detailed calculations and analysis. This isn't a place for guesswork; it's a domain where precision and knowledge are the reigning monarchs.
To make you understand better, consider the following:
- The formwork must withstand maximum loads during concrete pouring. It's not just about holding the concrete in place, but also resisting the pressure exerted by it.
- Bracing and support elements aren't just mere additions, they're essential lifelines. They provide the necessary support to maintain the formwork's shape and alignment.
- The strength of formwork materials and construction techniques are of paramount importance. It's like building a fortress; the stronger your materials, the more impregnable the fortress.
- Formwork failure isn't just costly; it's a risk to safety. Thus, every aspect of the formwork process must be meticulously planned and executed.
Load-Bearing Capacity Considerations
Having discussed how important structural integrity is to formwork, it's only appropriate to explore the significant question of load-bearing capacity and its critical role in the design of beams and girders. This capacity, fundamentally, determines how much weight these structures can efficiently shoulder without compromising their stability.
This capacity is a function of multiple factors, dominated by the material strength and the cross-sectional design of the beams and girders. For instance, concrete beams and girders, which are designed to resist bending stresses and shear forces, exhibit different load-bearing capacities than their steel counterparts. The properties of the materials used are, hence, a crucial determinant of the overall load capacity.
The size and configuration of the beams and girders also play a significant role in their load-bearing capacity. Larger cross-sections typically mean greater load-bearing capabilities, but the configuration of the beam or girder can also impact this. The geometry of the formwork can influence how the load is distributed across the structure, affecting the total weight it can bear.
In the end, engineers calculate load capacities based on these factors. These calculations aren't just theoretical exercises but are essential to the practical application of these structures in construction. They guarantee that the designed structures can comfortably carry the loads they're subjected to, without risk of failure.
Understanding the load-bearing capacity is, thus, not an optional exercise, but a critical element in the design of beams and girders. It's a liberating knowledge that empowers us to design and build structures that aren't only aesthetically pleasing but also structurally sound and safe.
Efficient Dismantling Processes in Formwork
Delving into the domain of efficient dismantling processes in formwork, we uncover the pivotal nature of systematic component removal, integral to preventing damage and optimizing reuse potential. The dismantling process isn't merely about taking apart the formwork; it's about doing it with finesse, maintaining the integrity of the components, and preparing them for their next role in construction.
This process draws heavily on efficient planning and coordination, ensuring a smooth change from being an integral part of a structure to being disassembled, inspected, and prepped for reuse. The choice of formwork system also plays a significant role. Systems with easy-to-operate mechanisms can drastically speed up the dismantling process, saving both time and costs.
Let's look at four key insights that can make the dismantling process more efficient:
- *Systematic Component Removal*: This methodical approach prevents damage and enhances reuse potential.
- *Effective Planning and Coordination*: This safeguards safety and enhances overall process efficiency.
- *Utilization of User-friendly Systems*: Systems with easy-to-operate mechanisms expedite the dismantling process.
- *Adherence to Manufacturer Guidelines*: This enhances safety and efficiency during dismantling.
Inspection of formwork components before dismantling ensures they're in good condition for reuse. Following the manufacturer's guidelines for dismantling procedures not only safeguards safety but also boosts efficiency.
In essence, efficient dismantling isn't just about disassembly; it's an art that liberates formwork components from one project, keeps them ready for the next, and thereby contributes to a sustainable construction process.
Frequently Asked Questions
How Do You Calculate Formwork for a Beam?
We calculate the formwork for a beam by finding the surface area. First, we measure the beam's length, width, and height. Then, we determine the beam's perimeter and multiply it by the length.
We don't overlook any extras like chamfers or fillets. This gives us the formwork area. We're careful to measure accurately to avoid waste, as formwork material isn't cheap.
It's crucial to be precise and efficient in our calculations.
What Are Four Principles of Good Formwork?
We believe a well-designed formwork abides by four principles.
Initially, it's structurally stable, bearing the weight of fresh concrete and construction.
Next, it guarantees accurate dimensions and finishes.
Thirdly, it's user-friendly, easy to assemble, dismantle, and reuse.
Finally, it meets safety regulations, providing a secure on-site environment.
These principles don't just create efficient formwork, they liberate us from unnecessary costs, safety hazards, and wasted time.
What Is the Importance of Beam Formwork?
We grasp the importance of beam formwork. It's the backbone of our construction, shaping and supporting beams while concrete sets. It's critical for accurate reinforcement placement and beam alignment.
This formwork must bear the weight of not just the concrete, but any additional construction loads. When designing it, we've got to take into account beam dimensions, load capacity, and installation ease.
It's more than just a mold; it's a key player in our building's overall structural integrity and stability.
What Is the Design Principle of Formwork?
We're designing formwork to support concrete's weight during pouring and curing. Our focus is on load-bearing capacity, stability, and installation ease. We're ensuring proper alignment, dimensions, and finishes, aiming to minimize wastage and labor costs.
We're integrating safety measures to prevent mishaps. We're empowering ourselves with efficient, safe structures. Our design principles aren't just about building, they're about creating a more liberated, efficient, and safer construction environment.
Conclusion
In wrapping up, we've unpacked the intricacies of beam and girder formwork design. We've highlighted the importance of material selection, support intervals, and load-bearing capacity.
We've underscored the detrimental effects of design errors and the need for structural integrity. Finally, we've emphasized efficient dismantling processes.
As we move forward, let's utilize these insights to develop more effective, resilient formwork designs, ultimately strengthening our structures and ensuring their longevity.