Formwork for Architectural Concrete Finishes
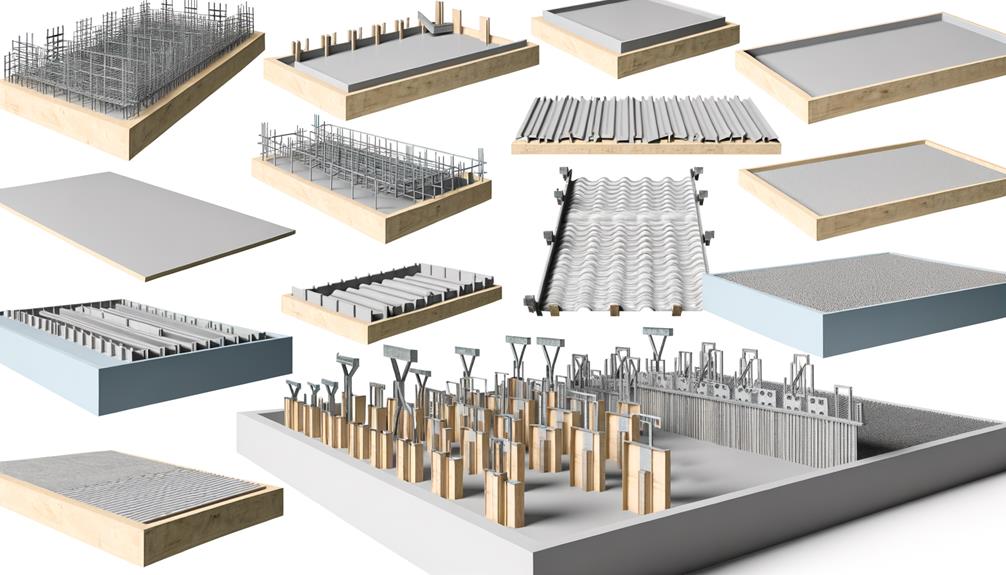
Formwork's pivotal in shaping architectural concrete finishes. It molds complex surfaces, gives concrete aesthetic versatility, and is a must for sophisticated finishes. Our choice of formwork material—like steel or exterior-grade plywood panels—affects the final appeal. We design formwork according to ACI 117 standards for quality and structural integrity. Special cement types and admixtures, chosen with precision, further refine the finish. After construction, prompt repair and rigorous clean-up maintain the finish quality. The journey from formwork selection to final concrete finish is intricate and artful, offering depths of detail just waiting to be explored.
Understanding Architectural Concrete
Exploring the domain of architectural concrete, we must first understand the crucial role that formwork plays, as it shapes the visual appeal and distinctive finishes that characterize these building structures. This isn't just about structural integrity; it's about the pursuit of beauty and uniqueness in design. It's about pushing boundaries and embracing the limitless potential of concrete as a medium of artistic expression.
Formwork technology is the canvas on which the masterpiece of architectural concrete is painted. Its significance lies in its ability to mold concrete into complex surface structures and textures, thereby allowing us to harness the aesthetic versatility of this robust material. The design precision required in formwork is profound, as it directly influences the final appearance of the architectural concrete.
To truly appreciate architectural concrete, we must explore the mastery of formwork technology. It's not just about constructing a mold; it's about envisioning and creating sophisticated finishes that elevate the visual impression of the structure. It's about transforming a common building material into a work of art, a demonstration of human creativity and craftsmanship.
This understanding liberates us from the conventional perception of concrete as a mere construction material. It broadens our perspective and stimulates us to think outside the box. Architectural concrete isn't a demonstration of the limitations of what we can build, but a bold statement of our potential to envision and create. It's more than a material; it's a dynamic palette for creation and innovation. Our grasp of formwork technology empowers us to fully exploit this potential and bring our architectural dreams to life.
Formwork Material Selection
Diving into the heart of formwork technology, we find ourselves faced with the pivotal task of selecting the right materials, a decision that will dictate not only the quality but also the aesthetic appeal of our architectural concrete masterpiece. We're not just talking about structural integrity here, but the very character of the final product. The choice of formwork material is a nuanced one, influenced by design requirements, desired surface finish, and project budget.
- Steel: Durable, reusable, and able to withstand heavy loads, steel is a reliable choice for formwork. It's excellent for creating smooth surfaces, but the cost can be prohibitive for some projects.
- Glass Fiber Reinforced Plastic (GFRP): GFRP is lightweight, resilient, and provides a unique finish. It's an innovative choice, but it requires expertise to handle properly.
- Exterior-Grade Plywood Panels: Versatile and cost-effective, these panels offer a good balance between performance and budget. The surface finish may not be as smooth as that of steel or GFRP.
- Non-Absorptive Materials: These materials, like high-density plastics, are perfect for achieving uniform, smooth finishes. They don't absorb moisture, ensuring a consistent cure for the concrete.
Material selection isn't about simply picking the most expensive or avant-garde option. It's about understanding the unique demands of each project, envisioning the final product, and making choices that bring that vision to life. The right formwork material not only meets practical needs but also serves as a canvas for our creativity, helping us to craft true architectural wonders.
Designing for Concrete Formwork
When we turn our attention to designing for concrete formwork, we must consider not only the selection of materials—be it steel, glass fiber reinforced plastic, or exterior-grade plywood panel—but also the alignment with ACI 117 standards, ensuring quality finishes and structural integrity. A meticulous approach is required, one that's driven by an unyielding commitment to quality and a keen eye for detail.
Face sheet deflection, for instance, is an essential factor. We must limit it to 1/400 of its span. This isn't simply a desirable attribute, but an indispensable requirement to maintain the structural integrity of our formwork. We can't afford any compromise when it comes to the stability of our structures.
Another equally critical aspect is the use of high-density, non-vapor transmitting form faces. These are recommended for architectural concrete formwork, and for good reason. They provide a smooth, impermeable surface, ensuring the formwork retains its integrity while delivering aesthetically pleasing, high-quality finishes.
Then there's the matter of concrete ties and bolts. These seemingly small components play a substantial role in formwork design. They need to be sized appropriately to withstand form design pressures, a crucial element for successful formwork construction.
In essence, designing for concrete formwork is an intricate dance of precision and practicality, of balancing aesthetics with structural integrity. It's a challenge we're more than capable of meeting, given our commitment to quality, our adherence to industry standards, and our willingness to embrace innovative and practical solutions. It's about embracing the constraints and turning them into opportunities for creativity and excellence. It's about liberation through meticulous design.
Cement Types and Uses
While we've been focused on designing the formwork, it's equally important to understand the role of cement types and their uses in architectural concrete. Cement isn't simply a binding agent; it's the backbone of our structures, the canvas for our designs, and the key to discovering new possibilities in architectural concrete finishes.
Let's explore deeper into this topic by discussing four key points:
- ASTM Compliance: The cement we use must conform to specific ASTM standards, such as C150, C595, C845, or C1157. Adhering to these standards guarantees the desired aesthetics and performance in our architectural concrete finishes. It's a commitment to quality that frees us from future structural issues.
- Special Cement for High-Quality Finishes: We need to ensure a consistent and adequate supply of special cement. This particular type of cement helps us maintain quality and meet project requirements, providing a solid foundation for our creative endeavors.
- Consistency and Reliability: A single, recommended source of cement should be selected for each project. This step guarantees the consistency and reliability we need to achieve the best results for our clients.
- Strict Adherence to Standards: Standards exist for a reason; they guide us in creating finishes that not only look great but also last. They help us strike a balance between form and function, aesthetics, and performance.
Understanding the types of cement and their uses is a significant step towards unleashing our creativity in architectural concrete design. It allows us to push the boundaries, to explore new possibilities, and to create concrete finishes that truly stand the test of time.
Importance of Admixtures
In our journey to create remarkable architectural concrete finishes, we can't overlook the critical role of admixtures. These components, often overlooked, are the unsung heroes of our craft, imparting specific properties to architectural concrete and enhancing its performance. They're the secret sauce, the magic ingredient, and the key to unleashing the full potential of concrete.
We must emphasize the necessity of avoiding admixtures containing calcium chloride to maintain the desired characteristics of the concrete. This seemingly insignificant detail can profoundly impact the final result, influencing the strength, durability, and overall aesthetic of the finish. It's in these finer details that we find our liberation, our ability to create without limitations, cementing our vision into reality.
The variety of admixtures available to us is vast, each designed to improve workability, durability, or appearance of architectural concrete. It's this versatility that allows us the freedom to tailor our work to specific project requirements, to achieve a unique expression of our craftsmanship. They're not just substances we mix into our concrete; they're tools we use to shape our world.
However, with great power comes great responsibility. The proper selection and use of admixtures are essential for meeting the requirements of architectural concrete specifications. It's not just about adding more or less; it's about understanding the symbiotic relationship between the elements, manipulating them to create a harmonious blend of strength, resilience, and beauty. This is the importance of admixtures in our craft, the essence of our work, and the heart of our vision.
Mixing and Transporting Considerations
Building on the importance of admixtures, we mustn't forget the role of proper mixing and transporting techniques in achieving superior architectural concrete finishes. The journey from raw materials to the final, polished concrete is a meticulous process, and every stage has the potential to either enhance or compromise the architectural integrity of the final product.
Now, let's focus on the critical considerations for mixing and transporting architectural concrete:
- Dedicated Clean Equipment: We've got to use clean equipment, exclusively for architectural concrete. This guarantees the quality standards we're aiming for are maintained and contamination is prevented.
- Delivery of Colored Concrete: It's paramount that colored concrete is delivered in full loads. This practice guarantees uniformity and consistency of color, a crucial aspect of our aesthetic objectives.
- Control of Proportion and Slump: Throughout the mixing and transporting process, we need to carefully control the proportion and slump of the concrete. This isn't just a technicality; it's an art form, a dance of precision that profoundly impacts our desired finishes.
- Uniform Delivery: Finally, uniformity in delivering designated architectural concrete isn't an option; it's a necessity. This is the way we guarantee the desired aesthetic outcomes.
In embracing these principles, we're not just following rules; we're embodying a vision of architectural excellence. We're contributing to a tradition of craft, precision, and beauty that elevates the mundane to the magnificent. This is more than concrete; it's a demonstration of human ingenuity and artistry.
Conveying and Placement Techniques
Ever reflected on how vital the process of conveying and placing architectural concrete is to achieving that exquisite finish we're aiming for? Understanding these techniques is essential to delivering the desired results.
A critical aspect of conveying architectural concrete is the careful supporting of transport and pump lines. Without such support, the efficiency of placement would be significantly compromised. Remember, we are pursuing perfection here; even the smallest mistake can mar the aesthetic appeal we aim for.
Prior approval from engineers or architects is also a fundamental consideration. We can't just start placing our concrete without ensuring we've got the green light from the experts. This ensures the integrity of both our design and our structure.
We must be mindful of splatter on the formwork faces as well. It's an often overlooked aspect, but it can impair the finish of our architectural concrete.
Here, let's have a look at some of the key points of conveying and architectural concrete placement:
Technique | Considerations | Impact |
---|---|---|
Supporting transport and pump lines | Efficient placement | Quality finish |
Prior Approvals | Ensures design and structure integrity | Professional standards |
Avoiding splatter | Prevents damage to finish | Aesthetic appeal |
Proper scheduling | Prevents delays | Timely project completion |
Avoiding segregation or horizontal movement | Maintains quality finish | Superior end product |
Formwork Stripping Procedures
Having thoroughly discussed the nuances of conveying and placing architectural concrete, we're now setting our sights on the equally significant process of formwork stripping procedures. This pivotal stage involves carefully liberating the concrete from its formwork confinement, a process that requires precision, patience, and a keen understanding of the material's behaviour.
- Timing is everything. The concrete has to be given ample time to set before the stripping process commences. This is to prevent damage to the surface and guarantee the concrete's structural integrity. Stepping in too early or too late can compromise the finished product, making timing a critical factor in this process.
- Systematic execution of the stripping process is a must. This involves:
- Releasing form ties
- Removing form panels
- Cleaning the formwork surfaces for reusability
Doing this systematically ensures the desired appearance and finish quality of the concrete is achieved.
- Adherence to manufacturer guidelines and industry best practices is non-negotiable. These guidelines are designed to secure safe and effective formwork stripping. They provide a roadmap for achieving the best results and mitigating potential risks.
- Finally, never underestimate the importance of cleanliness. Once the formwork has been stripped, ensuring it's properly cleaned and prepared for reuse not only prolongs its lifespan but also guarantees excellent results in future applications.
In essence, formwork stripping isn't just a step in the process—it's an art that requires skill, knowledge, and attention to detail. By following these procedures, we can liberate our architectural concrete from its formwork, revealing a masterpiece that stands as a proof of our craftsmanship and the timeless beauty of concrete.
Curing the Architectural Concrete
Delving into the following essential stage, we're shifting our attention to the art of curing architectural concrete, a process that greatly enhances the strength and durability of the finish while shaping its aesthetic appeal. This isn't just a technical process; it's an artistic endeavor, a dance of chemistry and craftsmanship that brings out the beauty of our work.
Curing methods aren't one-size-fits-all. They range from moist curing, which involves keeping the concrete surface wet to prevent premature drying, to the application of curing compounds that form a protective layer. We also have membrane curing, another technique that prevents surface drying. Each method has its own merits, and we choose the one that best suits the specific requirements and conditions of our project.
Time, too, plays an indispensable role in curing. It's not about rushing the process; it's about giving the concrete the time it needs to reach its full potential. The proper curing time is key to achieving the desired properties and appearance of architectural concrete. We can't stress enough the importance of patience in this stage.
Temperature and humidity control are other critical factors we consider. They must be meticulously managed for ideal results. We're not just following a recipe; we're creating a controlled environment that allows the concrete to mature beautifully.
In all these, we uphold industry standards and guidelines. This isn't about cutting corners; it's about ensuring the long-term performance of our architectural concrete finishes. We're committed to delivering excellence, not just in aesthetics but also in quality and durability.
Repairing and Cleaning Up
After the curing process, we swiftly shift our focus to repairing and cleaning up the formwork, a critical step in preserving the quality of our architectural concrete finishes. While the curing phase is indeed vital, it's only part of the journey. We acknowledge that our dedication to quality doesn't end there.
We've embraced a thorough approach to repairing and cleaning up, a routine that's as detailed as it's liberating. It's a process designed not just to maintain, but to potentially enhance the quality of our finishes.
- Prompt Damage Repair: In the face of any damage to the formwork, we don't hesitate. We're quick to patch, seal, and reinforce, ensuring no compromise on the finish quality. Our prompt action is a reflection of our commitment to preserving the integrity of our architectural concrete finishes.
- Rigorous Clean-Up: We're not just about fixing; we're about tidiness too. We meticulously remove any formwork debris, ensuring a smooth surface for the subsequent concrete pour. It's not just about aesthetics; it's about maintaining the perfect conditions for our work.
- Thorough Debris Removal: We go the extra mile in making sure that all concrete residue, dirt, and debris are completely removed. It's a non-negotiable in our process, a dedication to precision that's unwavering.
- Regular Maintenance: Beyond repair and clean-up, we uphold a regime of regular upkeep. It's a reflection of our vision of long-term quality and sustainability.
Treatment Methods for Architectural Concrete
In the domain of architectural concrete, we endeavor to apply various treatment methods, including acid etching, sandblasting, polishing, staining, and sealing, to not only preserve but also to elevate the aesthetic and functional quality of our finishes. We aim to transcend the conventional perception of concrete and transform it into a canvas for artistry and innovation.
Our acid etching technique is more than a process—it's an alchemy that infuses surfaces with a unique texture. We harness the power of chemistry, allowing acid to react with concrete and create a bespoke tactile experience.
Next, we turn to sandblasting, which is a method of stripping away the superficial, revealing the raw beauty of the aggregate beneath. It's a celebration of authenticity, of honoring the inherent qualities of our material.
Polishing, on the other hand, is a pursuit for perfection. We grind the concrete to a lustrous sheen, smoothing out imperfections and creating a surface that's not just glossy, but also resilient. It's a confirmation of the durability of our work, and an affirmation of our commitment to quality.
Lastly, we employ staining and sealing – staining for adding a vibrant play of colors, and sealing to safeguard our creations from stains, water damage, and the harsh rays of the sun. The sealant doesn't just protect—it enhances color and sheen, creating a finish that's both durable and beautiful.
We believe in the liberation of architectural concrete from the mundane, elevating it to a medium that embodies our creative vision. Our treatment methods aren't just techniques, they're a declaration of our dedication to pushing the boundaries of what's possible with architectural concrete.
Case Studies in Architectural Concrete
Let's explore some intriguing case studies that demonstrate the powerful influence of architectural concrete, starting with the exceptional use of matrix formwork technology in the Reiterstaffel Offices in Cologne. This innovative building project incorporated 325 prefabricated concrete elements, each meticulously designed and installed to showcase the full potential of matrix formwork applications.
HERING's unique approach to matrix formwork is truly revolutionary. They design individual formwork to meet unique aesthetic finishes based on specific project requirements. This tailored approach opens up new horizons for the architectural design, giving architects the freedom to create without boundaries.
Matrix formwork technology has an impressive capacity for realizing complex surface textures and intricate designs on concrete facades. Here are the key benefits:
- Detail Precision: With matrix formwork, it's possible to achieve a level of detail that was previously unattainable.
- Unique Aesthetics: The technology allows for the creation of bespoke concrete façades that are both visually stunning and structurally robust.
- Innovation: Architects and designers can now push the boundaries of what's possible with concrete finishes.
- Versatility: The technology can be applied to a wide range of architectural projects, from commercial to residential.
In essence, matrix formwork technology adds a distinctive touch to architectural concrete finishes, elevating the visual appeal of structures. It revolutionizes surface design possibilities, setting new standards for aesthetic excellence in construction. This breakthrough in architectural technology liberates us from the constraints of traditional design, offering endless possibilities for creative expression in the world of architectural concrete.
Frequently Asked Questions
What Are Four 4 Types of Concrete Surface Finishes?
We're exploring four types of concrete surface finishes.
First, there's formed concrete, made with molds for unique textures.
Then, we've form lined concrete, using patterns for design imprints.
Third, exposed aggregate finishes reveal the natural beauty of embedded materials.
Finally, troweled finishes offer a smooth, polished look.
Understanding these finishes empowers us to create diverse, enchanting spaces.
Let's liberate our creativity and reshape our understanding of concrete's potential.
What Is Architectural Concrete Finish?
We're discussing architectural concrete finishes, which are the final surface appearances of concrete in structures. They're not only functional but aesthetically appealing, transforming mundane surfaces into works of art.
They include formed concrete, form lined concrete, and exposed aggregate finishes among others. Our focus is to attain high-quality finishes, meeting design requirements and project specs.
We believe in the power of well-executed architectural finishes to liberate design potential.
What Is the Best Formwork for Concrete?
We're often asked, 'What's the best formwork for concrete?' Well, that depends on your needs. Steel and glass fiber reinforced plastic are tough and durable, but can be pricey. Exterior-grade plywood is more budget-friendly and easy to work with.
But remember, quality matters too. Your formwork should be high-density and non-vapor transmitting. And don't forget about the right form ties and bolts! They've got to be strong enough to handle the pressure.
What Are the Different Types of Concrete Formwork?
We're exploring various types of concrete formwork. Steel is durable and ideal for high-quality finishes. Glass fiber reinforced plastic offers flexibility for intricate designs. Exterior-grade plywood is a cost-effective choice. Non-absorptive materials help avoid surface blemishes.
However, all chosen materials must meet specific standards to achieve the desired results. It's a diverse field, and we're excited to investigate further into it.
Conclusion
To sum up, we've analyzed the importance of formwork in achieving high-quality architectural concrete finishes.
We've delved into material selection, design, cement types, admixtures, curing, and treatment methods.
We've also shed light on repair and cleanup processes.
By examining case studies, we've envisioned the infinite possibilities this material offers.
Let's continue to innovate, push boundaries, and create awe-inspiring structures using architectural concrete.