Formwork Efficiency: Tips for Optimizing Time and Costs
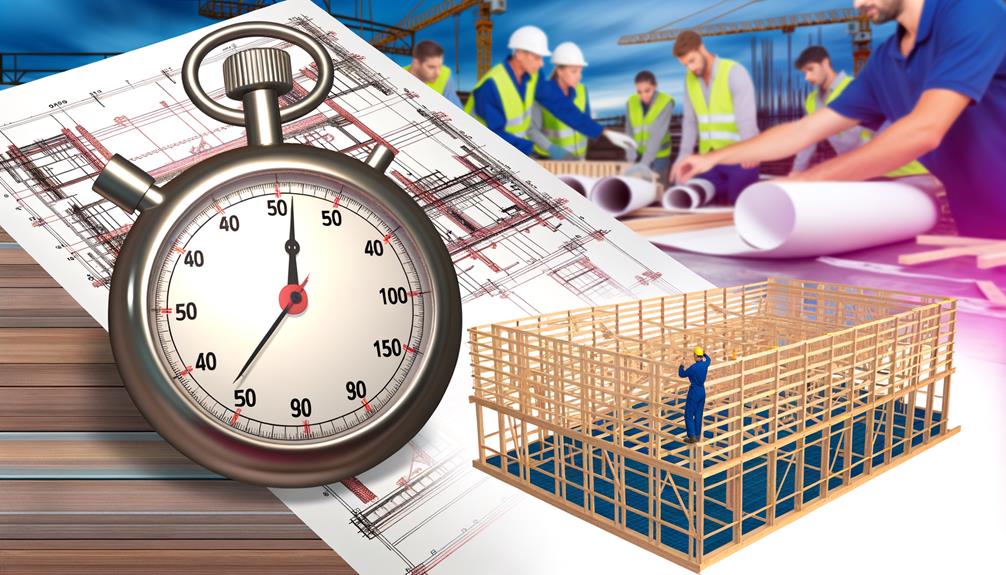
To optimize formwork efficiency, minimizing time and costs becomes essential. We suggest thorough planning and choosing high-quality, durable materials that match job conditions. Mechanization can enhance productivity while reducing manual labor. Worker training also plays a pivotal role, as it reduces errors and boosts efficiency. Prioritizing safety measures and controlling the concrete pouring process can prevent costly reworks. Standardizing systems can bring uniformity, whereas customization provides adaptability to specific project requirements. Curious about how to choose the right scaffolding system or the significance of IZB & ZTV solutions? There's plenty more to explore on this topic.
Understanding Formwork Efficiency
Delving into the domain of formwork efficiency, we find that its optimization isn't just beneficial but essential, as formwork-related costs can consume a staggering 50-60% of total concrete structure expenses. It's not a mere corner of construction budgeting we can overlook, but rather a substantial piece of the financial puzzle that demands attention.
One key aspect of formwork efficiency lies in the consistency of the process. By maintaining uniformity in formwork, we open doors for reusability and continuity. It's like playing a strategic game where each piece, each move, is interconnected. Every formwork panel reused is a win for our budget, a nod toward our sustainability goals, and a step closer to process continuity.
Mechanization of formwork systems is another game-changer. It's not only about embracing the latest construction technology, but about leveraging it to enhance efficiency and productivity on our job sites. Mechanized formwork systems can be the catalyst that propels us toward our project completion dates, keeping projects on track and budgets intact.
Moreover, the art of matching the formwork system to the job conditions can't be understated. It's like tailoring a suit – the better the fit, the more efficient the process. This consideration helps us avoid missteps, wasted resources, and unnecessary expenses.
Lastly, we find freedom through leveraging standardized off-the-shelf systems and specific formwork solutions. These tools allow us to optimize time and costs, giving us control over our construction narratives. Understanding formwork efficiency is about mastering these strategic elements, harnessing them to drive our projects toward success. This is our path to liberation from unnecessary costs and time delays.
Importance of Proper Planning
In the heart of optimizing formwork efficiency, proper planning stands as an undeniable cornerstone, capable of greatly slashing both material wastage and construction time. We can't stress enough the significance of meticulous planning in the domain of formwork systems. It's not just about choosing the right formwork based on load-bearing capacity and durability requirements, it's also about considering formwork reusability, site conditions, and labor availability.
A detailed, well-thought-out plan that takes into account all these factors can transform the construction process, making it more efficient and cost-effective. An ingenious formwork plan is like a road map, outlining the dimensions, shape, and layout of the project, and guiding us towards the destination of efficiency and cost savings.
We've seen firsthand how a well-designed formwork plan can lead to ideal slab construction, reducing the need for adjustments and modifications down the line. By minimizing the need for rework, we're able to save precious time and resources, thereby increasing overall productivity and profitability.
The beauty of proper planning is that it's an investment that pays off in spades. It requires an upfront effort, yes, but the rewards are manifold. We're talking about fewer construction errors, less material waste, reduced construction time, and ultimately, considerable cost savings. If we want to maximize our formwork efficiency, we can't afford to skimp on the planning process. It's what sets the stage for a smooth, efficient, and successful construction project.
Choosing the Right Materials
Selecting the right materials for formwork construction is like choosing the ideal ingredients for a recipe; it's a strategic move that guarantees the final product isn't just structurally sound, but also cost-effective and compliant with building codes. A well-selected material mix can make the difference between a successful project and a costly failure.
In our quest for formwork efficiency, let's consider the following essential elements:
- High-Quality Materials: Opt for durable and high-quality materials. They can withstand the pressure of the concrete, ensuring a smooth, defect-free slab surface. Yes, it's an initial investment, but it's one that pays off in the long run.
- Load-Bearing Capacity: Choose materials based on their ability to support the loads imposed during construction. The right choice here guarantees the best performance and longevity of your formwork system.
- Compliance with Project Specifications: Ensuring that your materials meet project requirements prevents wastage and additional costs. It also saves time, as you won't have to deal with materials that don't fit the bill.
- Adherence to Building Codes: Compliance isn't just about project specs. It's also about making sure your materials meet all relevant building codes. This step is non-negotiable and ensures the safety of your structure, workers, and future occupants.
Importance of Worker Training
Harnessing the power of skilled labor, we can't overlook the critical role that proper training in formwork techniques plays in streamlining construction processes. It's not just about having the right tools and materials, but about how to utilize them effectively. Familiarity with formwork system assembly and dismantling processes is essential to guarantee smooth operations.
Training, we believe, is the catalyst for enhanced efficiency, reduced errors, and improved productivity on construction sites. We're talking about the difference between a project that runs like a well-oiled machine and one that's riddled with delays and oversights.
Investing in worker training is an investment in the overall performance of your formwork system. The potential for time and cost savings is significant. Think about it: a well-trained worker knows the fastest, most effective ways to assemble and dismantle formwork. They can anticipate problems and troubleshoot on the fly, minimizing material wastage and reducing construction time.
What's more, training empowers workers. It equips them with the knowledge and skills to excel in their roles, fostering a sense of achievement and motivation. This, in turn, can boost morale and productivity on-site, and contribute to a positive, proactive work culture.
In the quest for formwork efficiency, we must remember: our workers are our most valuable asset. By prioritizing their training, we're not just optimizing our operations, but we're investing in their growth. It's a win-win situation. After all, a well-trained worker is a liberated worker, and a liberated worker is an efficient one. Let's make the most of this powerful resource at our disposal.
Safety Measures in Formwork
Safety measures in formwork construction aren't just a legal obligation, they're our first line of defense against accidents, delays, and costly rework. They represent an essential component of our strategy for optimizing time and costs in formwork construction. As we aim for liberation from inefficiencies, we're dedicated to implementing a proactive approach to safety.
Here are four key safety measures we aim to implement:
- Appropriate Personal Protective Equipment (PPE): We guarantee our workers are equipped with the right safety gear, including helmets, safety glasses, gloves, and high visibility clothing. PPE not only offers physical protection but also empowers our workers with the confidence to perform their tasks efficiently.
- Regular Inspections: We conduct routine checks to identify potential hazards in our formwork systems. This includes evaluating the stability of the structures, checking for any damaged parts, and verifying proper installation of components.
- Immediate Corrective Actions: When safety issues are identified, we don't delay. We take immediate corrective measures to resolve the problem, thereby minimizing the risk of accidents and maintaining a safe construction environment.
- Safety Training: We believe in empowering our workers with knowledge about safety protocols and best practices. Through regular training sessions, we equip our team with the skills to identify risks and respond effectively.
Embracing these safety measures isn't just about complying with regulations. It's a strategic move towards efficient formwork construction. When safety is prioritized, we're not just protecting our workers, we're also avoiding delays and reducing the costs associated with rework. Essentially, safety measures are a catalyst for formwork efficiency.
Controlling Concrete Pouring
Diving headfirst into the heart of formwork construction, overseeing concrete pouring is a critical step we carefully monitor to guarantee the formwork system is filled evenly, minimizing defects and eliminating costly rework. We're not just pouring concrete; we're weaving a tale of precision and finesse.
Through careful monitoring, we detect and expel air pockets, making sure our canvas of concrete is free of defects. It's crucial to pour at just the right consistency, the perfect blend of liquid and solid. A little too soft, and the formwork may not hold; a tad too hard, and we risk incomplete filling. This is a dance of balance, where every step, every pour is calculated.
The slab formwork construction, the backbone of our efficient formwork, relies heavily on our ability to control the concrete pouring process. We're not merely builders; we're artists, painting with concrete, ensuring each layer is as smooth and defect-free as the last.
Our vigilant monitoring eliminates the risk of honeycombing, that bane of a smooth surface. We make sure the formwork is filled correctly, not just for the sake of filling, but to create a masterpiece that stands the test of time and load.
Proper concrete pouring techniques, our secret sauce, guarantee a defect-free and smooth slab surface. It's not just about pouring concrete; it's about controlling the flow, guiding the liquid stone into a symphony of strength and durability.
In this world of formwork construction, we're not just workers; we're the orchestrators of creation, transforming ordinary concrete into architectural marvels. And controlling concrete pouring? That's our crescendo, the climactic moment where precision meets purpose.
How to Minimize Rework
In our pursuit of excellence, we strategically utilize a plethora of methods to minimize rework, starting with meticulous formwork planning and design to ensure accurate dimensions and layouts. We believe this is the cornerstone of any successful construction project, aiming to eliminate potential rework due to errors in sizing or alignment.
Here are four strategic steps we take to reduce rework:
- Incorporate high-quality materials: We comprehend the significance of quality. By using premium materials, we decrease the likelihood of material failure or surface defects that can lead to costly and time-consuming rework.
- Invest in proper training: We believe that an educated workforce is a powerful one. We provide our workers with appropriate training in formwork techniques, preventing construction errors that might necessitate rework.
- Ensure safety: Accidents and incidents not only endanger lives but also result in rework and project delays. So, we enforce stringent safety measures to avoid any mishaps.
- Monitor the concrete pouring process: We keep a close watch on concrete pouring to prevent issues like air pockets and honeycombing. This attention to detail saves us from unnecessary rework later.
We know you're yearning for liberation from the inefficiencies that plague the construction industry. We're here to help you achieve that. By minimizing rework, we not only save time and money but also enhance our overall productivity and efficiency. Aiming for perfection may seem like a challenging task, but with strategic planning and careful execution, it's entirely within our reach.
Reducing Material Waste
Consistently working towards efficiency, we've perfected our strategies to greatly reduce material waste during formwork construction, primarily through precise measurements, accurate cuts, and efficient material handling practices. Our approach is innovative, detailed, and strategic, ensuring that we're not just cutting down waste, but also optimizing resources, saving time, and minimizing costs.
To begin, we've learned the value of adjustable formwork systems. By adapting to fit the exact needs of a project, these systems help us guarantee ideal material usage and minimize leftovers. We're not just saving on materials here; we're also saving on time and labor, resulting in a more streamlined and cost-effective construction process.
Planning the formwork layout carefully is another strategy we've embraced. By minimizing the need for excess cutting or trimming, we're able to maximize our material utilization and reduce waste. It's a strategic move that's about more than just efficiency—it's about liberation from unnecessary costs and labor.
Lastly, we've made it a practice to regularly assess our material inventory and usage. This allows us to identify and address any potential wasteful practices promptly, ensuring that we're always improving and evolving in our quest for efficiency. It's a detailed, hands-on approach that keeps us accountable and ensures that we're always moving forward.
Collaborating With Contractors
Harnessing the power of collaboration, we work closely with contractors to gain a better understanding of project requirements and constraints, which in turn guides our selection and optimization of formwork systems. This partnership goes beyond mere cooperation and becomes a synergy of expertise, where shared knowledge and experience drive project success.
To visualize this collaborative process, consider these four strategic steps:
- Sharing Project Scope: We encourage open discussion about project specifications, including deadlines, quality expectations, and resource allocation. This transparency guarantees that both we and the contractors are on the same page about what needs to be achieved.
- Aligning Design and Construction: We actively involve contractors in formwork design discussions, ensuring that the final design aligns with construction realities. This approach minimizes potential rework and optimizes formwork usage.
- Identifying Challenges: Contractors' hands-on experience allows them to anticipate potential issues in formwork implementation. We value their insights and collaborate to develop preemptive solutions, avoiding costly delays.
- Streamlining Communication: We establish clear and efficient communication channels, promoting swift decision-making and fostering a responsive project environment.
The benefits of collaboration are tangible and significant. By working closely with contractors, we don't just enhance our understanding of project requirements; we create a dynamic project ecosystem where information flows freely, decisions are made promptly, and challenges are tackled strategically.
In this liberation-seeking era, we believe in breaking the silos and embracing collaboration. By doing so, we not only optimize formwork efficiency but also cultivate an innovative, detail-oriented and strategic project environment that's primed for success.
Benefits of Standardized Systems
Embracing standardized systems in formwork design and implementation reveals a wealth of benefits, fostering a seamless synergy between contractors and designers for efficient sizing, enhancing productivity through mechanization, and providing easy consistency. We can't understate the importance of this synergy. It's not simply about cooperation; it's about creating a powerful alliance where skillsets and resources converge to achieve peak output.
Mechanization, a key component of standardized systems, is a game-changer. It bolsters productivity by automating processes, reducing manual labor, and, consequently, cutting down on project timelines. It's a revolution in formwork design, propelling us into a domain of efficiency we've yearned for.
Moreover, standardized systems are synonymous with easy consistency. They offer a kind of uniformity that makes the implementation process smoother and more manageable. And with this consistency, we're able to streamline operations, eliminating the chaos often brought about by disarray.
Take the modular drop head systems, for example. By simplifying slab elevation changes, these systems reduce both material and labor hours. It's strategic, it's innovative, and it's a win-win for everyone involved. Similarly, panelized systems bring standardized panel shapes to the table. This eliminates the need for open framing and reduces crane picks, yet again saving time and resources.
In a world where time is money, standardized systems are your best investment. They provide an avenue for liberation from inefficiencies, empowering us to do more with less. So, let's continue to champion these systems, leveraging their strengths to elevate our formwork designs and implementations.
Customizing Your Formwork Solutions
While we've witnessed the advantages of standardized systems, there's also immense value in tailoring formwork solutions to meet specific job requirements, optimizing productivity and efficiency in the process. Customization, when strategically implemented, allows us to sidestep unnecessary adjustments and rework, in turn saving precious time and resources.
Let's delve into the benefits of personalizing your formwork solutions:
- Optimized Productivity: Customizing formwork to the specifics of a project eliminates the need for constant adjustments. By doing so, we're able to maintain a steady workflow, thereby maximizing productivity.
- Cost-effectiveness: When we tailor our formwork to fit the needs of a project, we're being economical. We avoid wastage and reduce the need for additional materials, leading to significant cost savings.
- Efficient Construction Process: Customization enhances the overall efficiency of the construction process. Tailored solutions facilitate seamless operations, reducing the likelihood of delays and hitches.
- Job-Specific Adaptability: Every construction project is unique, and so should be the formwork system. Customized solutions offer the flexibility necessary to adapt to varying job conditions, ensuring success.
In essence, customizing your formwork solutions is like fitting a unique piece into a puzzle; it seamlessly integrates into the project, enhancing productivity and cost efficiency. It's a strategic move that offers liberation from the constraints of standard systems, adapting to the unique requirements of each job. So let's shift our focus, let's customize our formwork systems, and optimize our construction processes, saving time and money while delivering quality work.
Mechanization in Formwork Systems
Delving into the domain of mechanization in formwork systems, we discover a powerful tool that greatly enhances productivity and efficiency. This technological revolution isn't only reshaping the construction industry, but also liberating us from traditional labor-intensive practices.
Through the use of mechanization, we're able to enjoy significant productivity gains. The presence of robotic assistance replicates exact processes consistently, ensuring that every piece of formwork is a perfect fit. It's exactly this type of precision that optimizes our time on the job, reduces waste, and ultimately, saves us money.
The beauty of mechanization doesn't stop at standardization. It extends to our ability to customize solutions, tailoring formwork to specific job requirements. This means we can adapt to any situation that arises, making us more versatile and efficient.
But the real game-changer? The drastic reduction in labor input. By utilizing mechanized systems, we're able to streamline operations and reduce the physical demand on our workforce. This not only improves safety on the job site, but also enhances our overall efficiency.
Coming to grips with mechanization in formwork systems isn't just about embracing the future. It's about recognizing the value of technology and its potential to liberate us from traditional constraints. As we continue to innovate and strategize, we're not just building structures, we're building a more efficient and productive future.
Choosing the Right Scaffolding System
Traversing the intricate world of scaffolding systems, we recognize that choosing the right one is paramount to enhancing project efficiency and safety. The right system can substantially reduce construction time and costs, while guaranteeing smooth slab construction and defect-free surfaces. It's not just about picking any scaffolding system; it's about selecting the one that aligns perfectly with your project's unique requirements.
- Consider the vital capacity: A scaffolding system must comfortably bear the weight of workers, materials, and equipment. Overloading can lead to disastrous consequences, so we mustn't underestimate this important factor.
- Evaluate the long-lasting: The lifespan of a scaffolding system directly affects the project's overall cost. The more durable the system, the more it can withstand harsh conditions without compromising safety or efficiency.
- Look at the ideal reusability: A system that can be reused across multiple projects saves money in the long run. It's not just a cost-effective choice but an eco-friendly one too.
- Check the quality of materials: High-quality materials ensure efficient and safe scaffolding system performance. Inferior materials might be cheaper initially, but they could lead to higher maintenance costs or even safety hazards.
Choosing the right scaffolding system isn't just a matter of ticking boxes. It's about understanding the complexities and intertwining these factors to create an ideal balance. It's about liberation from constraints and inefficiencies that hinder your project's progress. So, let's step into the world of scaffolding systems with a strategic mindset and a keen eye for detail. Let's make smart, informed decisions that enhance efficiency, reduce costs, and guarantee safety.
Influential Cost Parameters
Exploring the intricate financial landscape of formwork systems, we need to analyze the impactful cost parameters that can greatly sway the overall expenditure. It's vital to realize that purchasing prices play a major role in the total cost. The choice between crane or manhandled systems also plays a pivotal role in the financial equation. Weighing the benefits of each against the cost is crucial for efficient budget management.
The quality and durability of formwork components can't be overlooked. Investing in high-quality materials might seem steep upfront, but it's a strategic move. Over time, superior quality reduces replacement costs, ultimately proving to be cost-effective.
Maintenance costs, which include cleaning and storage expenses, are often underestimated. Regular upkeep ensures smooth operations, thereby avoiding costly work stoppages. Strategically planning storage can minimize the space required, reducing rental or purchase costs for storage facilities.
Lastly, we can't ignore transportation costs, heavily influenced by the volume of the formwork system components. Efficiently designed formwork systems that allow for better stacking and compactness can greatly reduce these costs.
It's evident that multiple parameters influence the overall cost of formwork systems. Each parameter intertwines with the other, creating a complex web of cost considerations. Understanding and strategically planning around these can lead to substantial cost savings. Remember, it's not about cutting corners, but about wisely allocating resources where they matter most. In this way, we can optimize our formwork systems, giving us the financial liberation we desire.
Optimizing formwork efficiency is all about looking beyond the initial price tag and delving deep into the influential cost parameters. The goal is to achieve cost-effectiveness without compromising on quality or safety.
Benefits of IZB & ZTV Solutions
Diving headfirst into the world of IZB and ZTV solutions, we find a treasure trove of benefits, particularly in the domain of independent evaluation of formwork system productivity. These solutions not only empower producers to check and assess the effectiveness of their systems, but they also provide a clear pathway to project cost optimization.
As we navigate this exciting landscape, we can identify four key advantages:
- Independent Evaluation: IZB offers an impartial assessment of formwork system productivity. This objective check guarantees that producers stay on top of their game, enhancing efficiency and productivity.
- Time Reference Values: Through thorough studies, IZB determines working time reference values. This means that you're not left guessing about the time it should take to complete a job. It's a strategic approach that eliminates uncertainty.
- Performance-Based Wages: The Federal Committee sets just values for performance-based wages. This creates a level playing field, allowing for competitive pricing and fair compensation.
- Neutral Advice: Main and subcontractors can optimize project costs with unbiased advice from IZB and ZTV. This advice enables strategic decision-making and cost-saving measures.
Embracing the benefits of IZB and ZTV solutions, we're not just streamlining our operations, we're liberating ourselves from inefficiencies. We're strategically positioning ourselves to deliver quality, efficiency, and value, all while ensuring that our workforce is fairly compensated. So, let's dive deeper into these solutions, and reap the rewards that they offer.
Frequently Asked Questions
How Can I Reduce the Cost of Formwork?
We've got several ways to lower formwork costs.
First, we're selecting materials that balance quality and price. We're also optimizing labor costs via productivity gains. We're making sure we reuse our formwork as much as possible. And, we're planning well to avoid unnecessary waste.
What Are Four Principles of Good Formwork?
We believe the four principles of good formwork are safety, efficiency, cost-effectiveness, and quality.
We're committed to designing formwork that guarantees worker safety, optimizes construction time, and is cost-effective.
We can't overlook the importance of using quality materials and skilled labor as well.
By adhering to these principles, we'll achieve smooth concrete surfaces and overall project success.
Let's liberate ourselves from unnecessary costs and risks, and embrace these principles.
Which Formwork Takes More Time?
We've found that formwork with complex designs, intricate shapes, and details often takes more time to set up. Additionally, systems requiring frequent adjustments or customization for specific project needs can add to the clock. High-rise structures, curved or sloped surfaces also require more time for accurate assembly and alignment.
It's a challenge, but we're always seeking innovative strategies to overcome these hurdles and boost efficiency.
Which Type of Formwork Is More Economical?
We've found that modular drop head systems are usually the most economical. They simplify slab elevation changes and boost productivity which saves us time and money.
Also, using standardized off-the-shelf systems offer cost benefits through easy consistency.
Additionally, panelized systems cut down on material and labor hours.
Conclusion
To sum up, we've seen that formwork efficiency is a game-changer. With proper planning, right materials, skilled workers, and safety measures, we can optimize time and costs.
Embracing mechanization and the right scaffolding system further enhances productivity.
Paying attention to cost parameters and implementing IZB & ZTV solutions can yield substantial benefits.
Let's revolutionize our approach to formwork and create structures that are efficient, safe, and cost-effective.