Formwork Maintenance Guide: Extending Equipment Lifespan
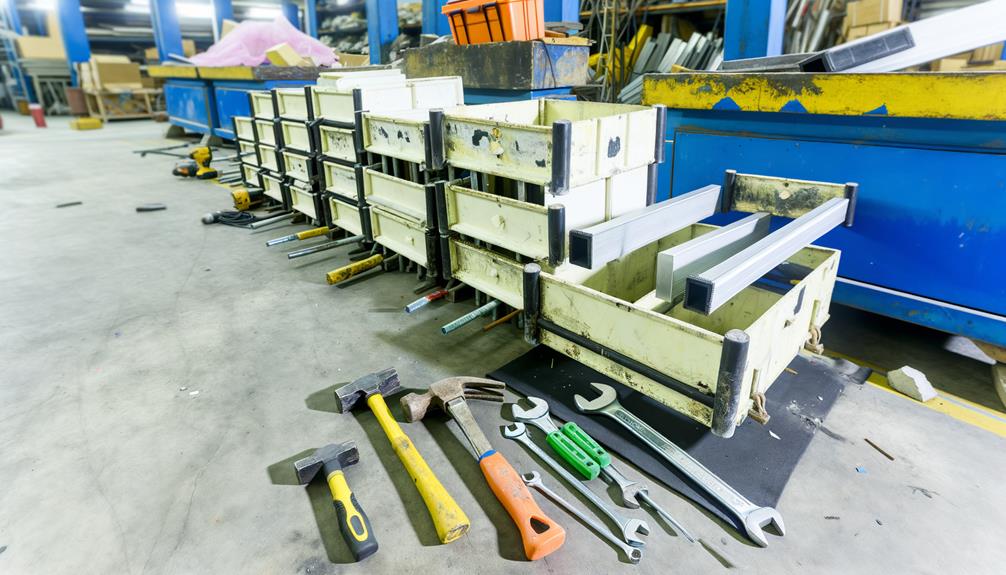
Extending the lifespan of your formwork equipment is easy with good maintenance practices. We recommend regular cleaning and inspections to identify potential damages early. Using form-release agents prevents debris interference and promotes smooth operations. It's critical to handle and store equipment correctly to avoid unnecessary wear and tear. Additionally, protective coatings and phenolic overlays can shield against environmental elements and admixtures. Sustainability also comes into play. Going for quality equipment and adopting eco-friendly methods can greatly reduce wastage and increase efficiency. Want to uncover the secrets to a longer-lasting formwork equipment lifespan? Buckle up, the future is here.
Understanding Formwork Equipment
Let's explore understanding formwork equipment, an essential component in creating sturdy, efficient, and long-lasting concrete structures. A deeper grasp of these tools will free us from the limitations of traditional construction methods, propelling us towards a future of innovative and efficient builds.
Formwork equipment includes panels, props, spindles, and accessories, all designed for creating temporary structures for concrete placement. These aren't just random elements thrown together; rather, they're part of a sophisticated system that supports the weight of fresh concrete, shapes it, and even aids in its curing and hardening process.
The materials used in formwork equipment, like steel, aluminum, plywood, or PVC, aren't chosen randomly either. Each serves a specific purpose, catering to varied construction needs and ensuring the right balance between durability and usability. Steel and aluminum are known for their strength, plywood for its lightness and cost-effectiveness, and PVC for its resistance to corrosion and chemicals.
Understanding not just the types of formwork equipment, but also their functions and the reasoning behind their material choices, is essential for successful concrete projects. It's not just about knowing; it's about applying that knowledge to create better, safer, and more efficient structures.
Looking to the future, we've to deepen our knowledge of formwork equipment. It's a stepping stone towards revolutionizing the way we build, breaking free from outdated practices. Let's embrace this change, and together, we can create a future of construction that's not just about erecting structures but about crafting architectural masterpieces.
Importance of Regular Maintenance
Understanding the intricacies of formwork equipment is just the first step; we also need to recognize the essential role regular maintenance plays in preserving the efficiency and longevity of these tools. Maintenance isn't a chore to be overlooked but an investment into the future, an assurance of seamless operation and extended lifespan.
We've all seen the consequences of neglect. A poorly maintained piece of equipment is a ticking time bomb, ready to disrupt work flow and burden us with costly repairs or replacement. But it doesn't have to be this way. We can take control, mitigate these risks, and promote a more productive, cost-effective future with regular maintenance.
Let's not forget the professional cleaning and repair services available to us. These experts have the skills and knowledge to make sure our equipment performs at its best. Utilizing these services isn't an expense—it's a smart move towards preserving our valuable assets.
And then, there are preventive measures like using concrete release agents—PERI Bio Clean and PERI Plasto Clean, for instance—that enhance longevity. They don't just guarantee an easy release of concrete from our formwork surfaces, but also protect our equipment from undue wear and tear.
Lastly, let's not underestimate the smooth operation of prop and spindle threads. Regular maintenance ensures we're never caught off guard with a malfunctioning prop or spindle.
In the quest for liberation, maintenance is our ally. It frees us from unexpected disruptions, unnecessary expenses, and premature equipment failure. So, let's embrace it, not as an obligation, but as a pathway to a more efficient, cost-effective future.
Stripping Techniques for Formwork
Often, we find ourselves grappling with the task of formwork stripping, a process that, if not done properly, can cause substantial damage to our valuable plywood forms. Stripping techniques have evolved, and innovative methods are now available that can preserve the integrity of our forms, prolonging their lifespan and saving us time and money.
Let's explore some techniques that we can adopt in our quest for liberation from the woes of plywood form damage.
- Avoid the Use of Metal Bars: It's critical to resist the temptation of using metal bars for stripping. Although it may seem efficient, it can cause irreparable harm to the plywood.
- Utilize Wood Wedges: Wood wedges are a game-changer in formwork stripping. They effectively protect the integrity of the plywood forms, ensuring a smooth stripping process.
- Leverage the Strength of Plywood: We must remember that plywood, by its very construction, resists edge splitting. This inherent strength should be harnessed during the stripping process to minimize damage.
- Opt for Large Panel Sizes: Large panel sizes can significantly reduce the time needed for stripping formwork. By embracing this future-focused approach, we enhance efficiency and productivity.
Cleaning and Repairing Guide
Exploring the realm of formwork maintenance, it's crucial we address the importance of professional cleaning and repairing, which can greatly prolong the lifespan and efficiency of our equipment. As we navigate this critical task, we can't overlook the significance of visual inspections. They're our first line of defense in identifying damage that might hinder performance. By spotting issues early, we can guarantee prompt repairs, keeping us ahead of the curve.
Jet washing our equipment is a recommended practice, especially if we've applied a release agent before the concrete cures. This method effectively removes debris, preventing it from interfering with future operations. In the pursuit of peak performance, it's essential that we earmark damaged panels for replacement. By doing so, we maintain the integrity of our formwork, ensuring longevity and reliability.
Professional cleaning and repair services aren't just a luxury; they're a necessity. These services utilize specialized machinery housed in depots to facilitate a range of cleaning and repairs, from minor adjustments to major overhauls. Leveraging these resources, we can keep our equipment in top shape, paving the way for a more efficient, cost-effective operation.
As we march towards a future where efficiency is king, our commitment to proper maintenance practices, including professional cleaning and repairs, will be our guiding light. We're not just maintaining equipment; we're safeguarding our productivity and paving the way for liberation from unnecessary costs and downtime. So, let's embrace these practices, knowing they're key to extending our equipment's lifespan and enhancing our operation's performance.
Applying Form-Release Agents
As we continue our journey towards efficient formwork maintenance, let's now focus on the application of form-release agents such as PERI Bio Clean and PERI Plasto Clean, key enablers in the easy removal of concrete overspill. These agents not only make our work easier but also contribute greatly to prolonging the lifespan of our formwork equipment.
Through innovative and targeted application of these release agents, we can reduce porosity and cavity formation on the formwork, and even prevent rusting. Remember, it's not just about the present; we're setting up for the future, ensuring smoother operations down the line.
- Identify the Right Agent: PERI Bio Clean is ideal for metal formwork while PERI Plasto Clean is best for polymer-based products like DUO. Choosing the appropriate agent will ensure maximum effectiveness.
- Apply Before Curing: This prevents concrete discoloration and assists in demoulding, saving us time and energy in the long run.
- Use Specific Agents: This is important for the smooth operation of prop and spindle threads. It's one of those small steps that make a big difference.
- Regular Application: Don't wait until you notice a problem. Keep applying the agents as part of your regular maintenance routine.
Handling Tips for Formwork
While taking care of our formwork equipment, it's crucial that we don't overlook the importance of proper handling to prevent chipping, denting, and corner damage on our concrete forms. This is where our handling tips for formwork come into play, ensuring we utilize our equipment in a manner that extends its lifespan.
Stacking panels flat, face-to-face, and back-to-back is the ideal way for safe hauling. This method not only keeps the panels in a safe and secure position but also ensures that the weight is evenly distributed, reducing the risk of damage during transportation.
Cleaning forms immediately after stripping is another critical step in formwork handling. It's not just about keeping the formwork clean, it's about preserving the integrity of the formwork's surface. By cleaning and then stacking the panels face-to-face, we minimize the risk of scratches or other surface damages that can affect the final concrete product.
For plywood panels, it's crucial to store them in a shaded area away from sun and rain or cover them loosely. This simple yet effective measure can greatly reduce the risk of warping or other weather-related damages.
To assist in proper handling, we recommend the use of plywood stack handling equipment and trailers. These tools are designed to secure the transportation of concrete forms, minimizing the potential for accidental damage.
Here's a quick table summarizing our handling tips:
Handling Tips | Reason | Outcome |
---|---|---|
Stack panels flat, face-to-face | Even weight distribution | Less potential for damage |
Clean forms immediately after stripping | Preserve surface integrity | Minimize risk of scratches |
Store plywood panels in shade or covered loosely | Avoid weather-related damages | Less warping |
Use handling equipment and trailers | Secure transportation | Minimize accidental damage |
Proper Storage Techniques
After mastering the handling of formwork, let's shift our focus to storage techniques that can further extend the lifespan and maintain the performance of our equipment. Proper storage isn't just about finding a place to stash our equipment, it's about creating an environment where our tools can rest, recover, and be ready for the next job.
- Location is Key: Store our formwork equipment in a cool, dry place, away from harsh chemicals. This environment prevents damage and maintains the longevity of our tools. A clean, controlled storage area is the first step towards preservation.
- Stack with Care: When it comes to stacking equipment, we must be mindful. Use spacers to guarantee even weight distribution and avoid deformation. It's not just about saving space, it's about protecting our equipment from unnecessary strain.
- Oil for Protection: A light coat of oil, like PERI Clean, prevents rusting during storage. This simple step can be the difference between usable and unusable equipment when we need it most.
- Airflow Matters: Finally, don't forget about airflow. Adequate air circulation around stored equipment is essential to maintain peak performance and lifespan.
We're not just storing equipment, we're safeguarding our investment. Proper storage techniques extend service life, maintain durability, and ensure our tools are ready to perform when we need them. It's a future-focused approach that liberates us from constant replacements and repairs. So, let's embrace these techniques, treat our equipment with care, and guarantee a longer, more productive life for our formwork tools.
And remember, the next step in formwork maintenance is the application of protective coatings – but that's a topic for another day.
Application of Protective Coatings
Delving into the domain of protective coatings, we uncover yet another key to extending the life and enhancing the performance of our formwork equipment. These coatings act as an impenetrable shield, guarding our tools against moisture, chemicals, and abrasion. It's a liberating solution that not only boosts longevity but also slashes the need for frequent repairs and replacements.
Well-applied coatings greatly mitigate wear and tear, ensuring our formwork surfaces remain robust and resilient. Field-applied coatings, such as lacquers, offer water resistance and a sturdy defense against environmental elements, together fostering a future where our equipment outlasts expectations.
Remember, it's not just about applying any coating, but the right one. We've tabled below three top-rated coatings and their unique benefits:
Coating Type | Benefit 1 | Benefit 2 |
---|---|---|
Lacquer | Enhances Water Resistance | Shields against environmental elements |
Polyurethane | High Abrasion Resistance | Excellent Chemical Resistance |
Epoxy | Superior Durability | High Impact Resistance |
Influence of Admixtures on Forms
Exploring the intricate terrain of admixtures in our concrete mixes, we find that these powerful additives can greatly impact formwork removal schedules and surface longevity. Their applications are as diverse as they're transformative, but they also bring about potential challenges for formwork maintenance.
These additives, while enhancing concrete performance, can alter setting times, leading to a recalibration of formwork removal schedules. This necessitates a forward-thinking approach to work scheduling, liberating us from conventional timelines and pushing us to innovate.
Silica fume admixtures, for instance, increase concrete abrasiveness, posing a threat to the lifespan of formwork surfaces. Here is where the future-focused planning comes into play. We must proactively counter these effects by incorporating elements like phenolic overlays, known for their resistance to alkaline solutions and abrasion.
To better understand the influence of admixtures on forms, let's explore into four areas:
- Altered Setting Times: Admixtures can speed up or slow down concrete setting times, affecting when formwork can be safely removed.
- Increased Abrasiveness: Certain admixtures like silica fume can increase concrete's abrasiveness, shortening formwork lifespan.
- Chemical Effects: Some admixtures may chemically react with formwork materials, leading to decreased lifespan of forming panels.
- Countering Measures: Phenolic overlays can be used as a protective layer against the adverse effects of admixtures.
Role of Concrete Foundations Association
While admixtures play a significant role in formwork, it's also important to highlight the immeasurable contributions of the Concrete Foundations Association in advancing our industry. Their drive towards energy-efficient technologies is a proof of their dedication to a future-focused approach. In 2020, their Above Grade Residence project received accolades for its innovation, a shining example of their forward-thinking initiatives.
The Association isn't just about innovation, though; they're also advocates for sustainability. They've thrown their weight behind numerous initiatives to reduce the environmental footprint of construction. We're talking about a greener future, where our projects leave a minimal impact on the environment. It's an inspiring vision, and one that we wholeheartedly support.
In addition to their environmental efforts, the Concrete Foundations Association is a valuable resource for our industry. They provide indispensable support for advancements in concrete technology, helping us to elevate our work and extend the lifespan of our equipment.
They also understand the importance of quality forms. Their focus on promoting high-quality forms and fostering collaboration with industry partners helps us mitigate shortages and ensure construction continuity. This commitment to quality and collaboration empowers us to deliver the best for our clients, and for the world.
Sustainable Construction Practices
As we shift our focus to sustainable construction practices, it's clear that these eco-conscious methods aren't just good for the planet, they're also beneficial for our bottom line. Sustainable construction in formwork maintenance means less waste, more environmental responsibility, extended equipment lifespan, and ultimately, cost savings.
Here are four key methods we've identified to enhance your sustainable construction practices:
- Regular Cleaning and Inspection: The more frequently we inspect and clean our equipment, the longer it lasts. This reduces the need for frequent replacements, minimizing waste and saving money.
- Professional Repair Services: By utilizing professional repair services, we guarantee our equipment is handled with care and expertise, enhancing its longevity and sustainability.
- Waste Reduction: We must aim to reduce waste wherever possible. This includes recycling or reusing materials, reducing the amount of new materials needed and the waste going to landfill.
- Investing in Quality Equipment: Quality equipment may cost more upfront, but it lasts longer. This reduces the frequency of replacements and contributes to sustainability.
We're in a time of great change and the construction industry must adapt. By integrating these sustainable practices into our formwork maintenance routine, we're not only investing in the future of our planet, but also optimizing our return on investment. This isn't just about survival, it's about thriving in an ever-evolving industry. Let's break free from old, wasteful habits and embrace a future that's sustainable, profitable, and liberating.
Frequently Asked Questions
What Are the Potential Hazards of Not Properly Maintaining Formwork Equipment?
If we don't maintain formwork equipment properly, we're risking worker safety. Damaged or worn out gear can lead to accidents, injuries, even fatalities. There's also the risk of project delays, additional repair costs, and lower quality work.
We're all about fostering safer, more efficient work environments, so let's make sure we're taking care of our tools. Remember, our goal is liberation from these preventable hazards. Together, we can make our worksites safer, more productive places.
Are There Special Training or Certifications Required to Maintain Formwork Equipment?
We're often asked if special training or certifications are needed to maintain formwork equipment. While it's not legally required, we strongly recommend it. Proper training guarantees you're up-to-date with the latest techniques and safety standards. It also extends the equipment's lifespan, saving us money in the long run.
Let's think about our future, invest in knowledge now to avoid costly repairs later. We're all for liberating ourselves from unnecessary costs and potential hazards.
How Does the Cost of Regular Maintenance Compare to the Cost of Replacing Damaged Formwork Equipment?
We've found that regular maintenance costs are notably lower than replacing damaged formwork equipment. By keeping up with routine checks and repairs, we're not only extending the lifespan of our gear, but we're also saving money in the long run.
It's like the old saying goes, 'An ounce of prevention is worth a pound of cure.' We're investing in our future by taking care of our equipment today.
Are There Specific Brands or Types of Form-Release Agents That Are Recommended for Certain Types of Formwork Equipment?
We're often asked if certain brands or types of form-release agents are recommended for specific formwork equipment. Indeed, it's not a one-size-fits-all situation. Different materials require different agents for best results.
We're always researching and testing new products to provide the top recommendations. We're committed to empowering you with knowledge that'll extend your equipment's lifespan, saving you time and money.
What Are the Environmental Impacts of Not Properly Maintaining and Disposing of Formwork Equipment?
We're all aware that improper maintenance and disposal of formwork equipment can lead to severe environmental consequences. It's not just about equipment lifespan, it's about our planet's health.
Landfills swell with unrecycled materials, and toxins can leach into our soil and water. We're looking to a sustainable future, where we reduce, reuse, and recycle our resources.
Our shared responsibility is to make sure we're not contributing to environmental degradation.
Conclusion
To summarize, we've explored the significance of maintaining formwork, prolonging its lifespan with stripping techniques, cleaning, and protective measures.
We've emphasized the crucial roles of form-release agents, admixtures, and the Concrete Foundations Association.
We're confident that, by embracing these sustainable construction practices, we can indeed propel our industry towards a more efficient, durable, and eco-friendly future.
Let's continue to innovate our workspaces, transforming them one formwork at a time.