Formwork Material Selection: Wood Vs. Steel Vs. Aluminum Revisited
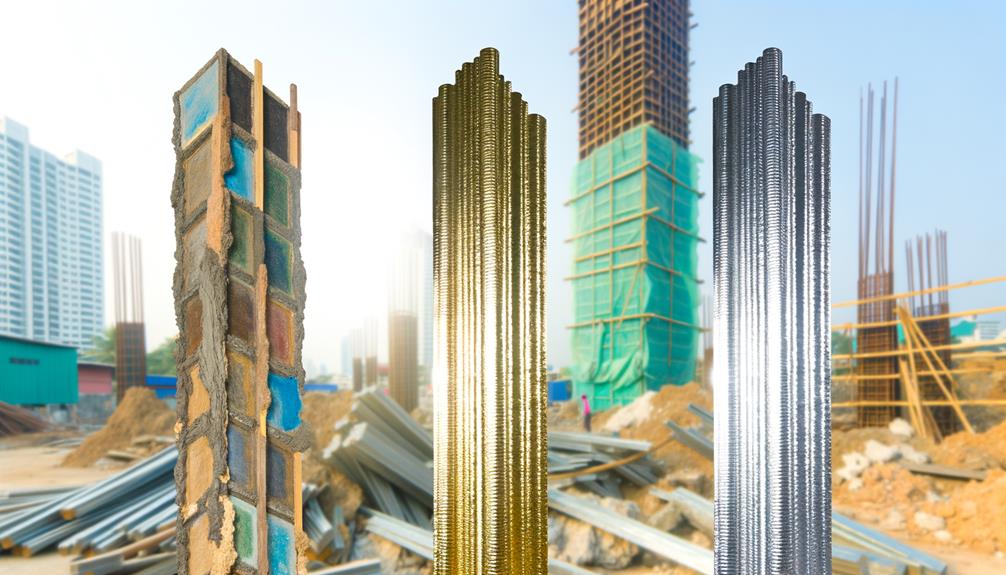
In selecting formwork material, one must consider the project's needs, budget, and environmental conditions. Wood is inexpensive and easily manipulated, great for smaller projects. However, it lacks the strength and durability of steel, which, while initially costly and labor-intensive, withstands harsh conditions well. It's essential for heavy-duty projects. Aluminum, though pricier upfront than both wood and steel, is lightweight, durable, and can be reused over 200 times, making it cost-effective in the long run. Continue with us to discover how these materials fare in a more detailed comparison.
Understanding Formwork Materials
Diving into the world of formwork materials, it becomes clear that the choice between wood, steel, and aluminum isn't just a matter of personal preference, but involves careful consideration of factors such as thickness, load-bearing capacity, durability, repetition usage, and installation procedures.
Wood, with its thickness ranging from 12 to 18 mm, can support loads between 25-30 kN/sqm. However, its durability falls short, requiring more upkeep than its counterparts.
Steel formwork, on the other hand, brings a notable improvement in durability. With a robust thickness of 55 mm, it handles loads from 30-60 kN/sqm. This increased strength, coupled with better longevity, makes steel a compelling choice. Yet, we can't overlook aluminum. With a sturdy thickness of 65 mm, it boasts the ability to support 50-70 kN/sqm loads, outperforming both wood and steel. Known for its strength and resistance to rust, aluminum's durability stands unrivaled.
When considering repetition usage, wood allows for 5-8 repetitions, while steel jumps to 100-120. Aluminum, impressively, allows for over 200, indicating its cost-effectiveness over time. The installation process is another pivotal factor. Wooden formwork's assembly and disassembly are labor-intensive, ramping up costs in the long run. Contrastingly, aluminum allows for quick setup and break down, saving both time and labor costs.
Wood Formwork: An Overview
Delving into the specifics of wooden formwork, we find that it's typically constructed using timber or plywood sheets, with thicknesses ranging from a modest 12 to 18 mm. This construction technique renders it a lightweight, cost-effective option despite higher labor and maintenance costs. Weighing in at around 10 to 12 kg/sqm, it's notably less cumbersome than its steel or aluminum counterparts.
Wooden formwork's load-bearing capacity is a commendable 25-30 kN/sqm, but it's not without limitations. While it's a wallet-friendly choice initially, it's worth noting that the long-term costs may add up due to its relatively lower strength and durability. Generally, wooden formwork supports 5-8 repetitions before showing signs of wear and tear, which may necessitate frequent replacements in larger, longer-term construction projects.
Another aspect that warrants attention is the labor-intensive nature of wooden formwork installation and dismantling. These processes can be time-consuming, adding to project timelines, which, in turn, can impact overall productivity and project costs. While it's certainly not a deal-breaker, it's an important factor to take into account when making decisions about formwork materials.
Advantages of Wood Formwork
Exploring the advantages of wood formwork, we find that its cost-effectiveness particularly shines in small projects with limited budgets. Unlike its steel and aluminum counterparts, wood formwork's initial investment is notably lower, providing an economical solution for smaller-scale construction endeavors.
Another advantage is its malleability and ease of manipulation on-site. Wood formwork can be cut, nailed, or shaped to fit the unique specifications of a project, giving freedom and flexibility to builders.
Despite its perceived lack of durability compared to steel or aluminum, wood formwork can actually be reused multiple times with proper maintenance. This reuse further enhances its cost-effectiveness, making it a viable option not just for one-off projects, but for those with a series of similar assignments in the pipeline.
To give a clearer picture of the advantages, we've put together the following table:
Advantage | Explanation | Impact |
---|---|---|
Cost-effectiveness | Lower initial investment compared to steel or aluminum | Ideal for small projects with limited budgets |
Malleability | Can be cut, nailed, or shaped on-site | Gives flexibility to builders |
Customizability | Can be tailored to fit unique project requirements | Avoids the need for costly custom-made metal formworks |
Reusability | Can be used multiple times with proper maintenance | Further enhances cost-effectiveness |
Accessibility | Widespread availability and ease of acquisition | Simplifies sourcing and logistics |
We believe in the liberation of choice, and understanding the advantages of wood formwork can empower you to make informed decisions tailored to your project needs. After all, the right choice of formwork material can significantly impact the success of your construction project.
Limitations of Wood Formwork
While wood formwork displays several advantageous qualities, it's important to also consider its limitations, especially its lifespan typically restricted to only 5 to 8 reuses due to inevitable wear and tear. This limitation, though seemingly small-scale at first, can accumulate substantial costs over time regarding material replacements and labor hours.
Furthermore, wood formwork's susceptibility to moisture damage, warping, and decay can greatly reduce its overall lifespan. These factors, coupled with its lower strength compared to steel and aluminum, make it less suitable for heavy-duty construction projects.
The need for frequent maintenance, repairs, and replacements further increases the operational costs associated with wood formwork. This is a significant drawback, particularly for large-scale or long-term projects where cost efficiency is a top priority.
Moreover, wood formwork is more prone to surface imperfections and deformations. These defects not only affect the quality of the work but also the finish of the concrete structures. This could lead to rework or additional finishing tasks, further increasing project costs and timelines.
Steel Formwork: An Overview
Turning our attention to steel formwork, we find it as a compelling choice for construction projects due to its remarkable thickness of 55mm and impressive load-supporting capacity ranging from 30 to 60 kN/sqm. This robustness, contrasted with the limitations of wooden formwork, can't be ignored. We're talking about a material that not only holds its own regarding strength but also showcases longevity and reliability with a range of 100 to 120 repetitions.
Of course, some might argue that the upfront cost of steel formwork is higher than that of wood. But we'd urge you to look beyond the initial cost and consider the long-term gains. Think about it; the superior durability and resistance of steel to harsh conditions mean fewer replacements, less maintenance, and ultimately, a more cost-effective solution in the long run. It's clear that the longevity of steel formwork translates to significant savings over time.
Now, we should note that while installation of steel formwork is generally easier than wood, it might require a tad more labor during setup. But isn't that a small price to pay for the balance it offers between strength and convenience?
Benefits of Steel Formwork
Expanding on the overview of steel formwork, let's emphasize the numerous advantages it brings to construction projects. Particularly, steel formwork's ability to support high loads makes it ideal for heavy construction. With a capacity ranging from 30-60 kN/sqm, it's sturdy enough to handle demanding projects without wavering.
Additionally, steel formwork boasts superior durability. With a lifespan of 100-120 repetitions, it greatly outlasts wooden formwork. This resilience is a proof of its robust nature, guaranteeing it can withstand the rigours of construction sites.
Benefit | Description |
---|---|
Load Capacity | Steel formwork supports 30-60 kN/sqm, suitable for heavy construction. |
Durability | Outlasting wooden formwork with 100-120 repetitions. |
Weather Resistance | Steel formwork withstands harsh conditions, ensuring reliability. |
Ease of Installation | Steel formwork provides efficiency and convenience in the construction process. |
Cost-Effective | The strength and durability of steel formwork reduces maintenance needs, saving money in the long run. |
Another advantage lies in steel formwork's resilience to harsh weather and wear. This characteristic ensures it remains dependable in various conditions, whether under the scorching sun or in the pouring rain.
Installation is another area where steel formwork excels. It's easier to install than its wooden counterpart, enhancing efficiency and convenience during the construction process.
Drawbacks of Steel Formwork
Despite its numerous advantages, steel formwork isn't without its drawbacks, particularly regarding weight, labor requirements, susceptibility to rust, initial cost, and limited use. Weighing between 35 to 85 kg/sqm, it's notably heavier than other formwork options. This not only poses handling challenges but also increases the risk of injuries during installation.
Additionally, steel formwork can be labor-intensive to install. With project timelines and efficiency paramount, it's crucial to take into account that steel formwork might necessitate more hands on deck compared to its aluminum counterpart. This increased labor can lead to a rise in project costs, reducing overall cost-effectiveness.
Furthermore, we can't overlook steel's susceptibility to rust and corrosion over time. Despite its robustness, without proper maintenance, the longevity of steel formwork can diminish, once again adding to the overall cost and impacting the project timelines.
The initial cost of steel formwork also presents a significant challenge. It's generally pricier than wooden formwork, potentially making it a less economical choice for some projects, especially those with tight budgets.
Lastly, steel formwork's limited number of repetitions—typically around 100 to 120—restricts its use for multiple projects. This limitation may prove unfavorable, particularly for construction companies working on several projects concurrently.
Aluminum Formwork: An Overview
Shifting our focus to aluminum formwork, it's clear that this material offers a compelling alternative to steel, blending strength with lightweight construction. It's no surprise that more and more construction companies are turning to aluminum as their material of choice for formwork. Let's explore why.
- Strength and Weight: Aluminum formwork panels typically have a thickness of 65 mm, striking a balance between strength and weight that makes them ideal for large-scale projects. This thickness allows aluminum formwork to support high loads, handling between 50-70 kN/sqm.
- Durability and Longevity: The robust nature of aluminum formwork isn't just about its ability to withstand heavy loads. It also extends to its lifespan. Unlike other formwork materials, aluminum formwork can be reused over 200 times, offering excellent cost-effectiveness.
- Efficiency: The installation and dismantling of aluminum formwork is efficient and quick, presenting valuable time and labor savings. It's an element that can greatly enhance the speed of construction activities.
- Resistance to Rust: We can't overlook the fact that aluminum formwork is resistant to rust. This characteristic guarantees its durability and longevity, even in challenging environmental conditions.
Pros of Aluminum Formwork
Diving into the advantages of aluminum formwork, it's clear that its lightweight nature, clocking in at only 20-25 kg/sqm, greatly eases handling and transportation processes. This feature not only reduces the physical burden for workers but also notably cuts down on transportation costs. In a world where efficiency is valued, this lightweight characteristic is an undeniable benefit.
Moreover, despite its lightness, aluminum formwork is impressively strong. It can withstand high loads ranging from 50 to 70 kN/sqm, offering a reliable structure that guarantees safety and stability. This is vital in construction projects where the risk factor is high.
Now, let's take a look at the durability and cost-effectiveness of aluminum formwork:
Advantage | Explanation |
---|---|
High Durability | With over 200 repetitions possible, aluminum formwork outlasts its counterparts, making it a smart long-term investment. |
Rust Resistance | Aluminum formwork is resistant to rust, ensuring a longer lifespan and minimal maintenance. |
Quick Installation and Dismantling | The process is efficient, reducing labor costs and construction time. |
Cost-Effective | Despite a higher initial cost, the durability and efficiency of aluminum formwork make it cost-effective in the long run. |
Environmental Impact | Aluminum is more environmentally friendly than other materials due to its recyclability. |
We can't overlook the fact that aluminum formwork is a game-changer. Its advantages are not just about cost savings or efficiency, but also about creating safer, more sustainable construction sites. As we aim for liberation in our choices, aluminum formwork presents a compelling choice for our construction needs.
Cons of Aluminum Formwork
While we've highlighted the numerous advantages of aluminum formwork, it's important to also consider some of its potential drawbacks, particularly those related to cost.
- Initial Expense: Aluminum formwork can be more expensive initially compared to wood or steel options. This might be a deterrent for budget-conscious projects. While the long-term benefits might outweigh the upfront costs, the initial investment can be a hard pill to swallow for some.
- Not Suitable for All Projects: Due to its cost, aluminum formwork may not be suitable for all types of construction projects. Projects with a smaller scale or shorter duration mightn't be able to justify the investment in aluminum formwork.
- Higher Maintenance Costs: Maintenance costs for aluminum formwork might be higher than for steel or wood options. These can include cleaning, repair, and storage costs, which can add up over time.
- Cost-Effectiveness: The cost-effectiveness of aluminum formwork is more evident in projects with high repetitions and long durations. For projects that don't fit this mold, the financial benefits of aluminum formwork may not be realized.
Comparative Analysis: Wood Vs. Steel
In this section, we'll conduct a detailed analysis, comparing the pros and cons of wooden formwork against its steel counterpart, to help you determine which option best aligns with your project's unique requirements and budget constraints.
Wooden formwork, typically 12 to 18 mm thick, can withstand a load of around 25-30 kN/sqm, making it a viable choice for projects with limited repetitions. On the plus side, it's cost-effective, making it a budget-friendly option. However, its durability falls short when compared to steel, limiting its lifespan and cost-effectiveness over time.
On the other hand, steel formwork, with a thickness of 55 mm, can handle a load of 30-60 kN/sqm, offering superior durability for 100 to 120 repetitions. This makes it an advantageous choice for projects requiring multiple uses. Although it's heavier than wood, it provides superior strength and durability, enhancing the stability and safety of your construction project.
While steel formwork might be more expensive upfront, its resistance to wear and tear can save you money in the long run by reducing the need for frequent replacements, which can disrupt project timelines and increase costs.
Comparative Analysis: Wood Vs. Aluminum
Shifting our focus to the comparison between wood and aluminum formwork, it's evident that the latter's superior weight, strength, and durability position it as a standout choice for extensive construction projects. The characteristics of aluminum, such as its strength and resilience, make it a more reliable material over wood, especially for grand-scale constructions.
Let's explore the specifics:
- Weight: Aluminum formwork weighs in at 20-25 kg/sqm, double that of wooden formwork, which is typically 10-12 kg/sqm. This gives aluminum a stability advantage, particularly in large-scale projects.
- Loading Capacity: Aluminum can handle loads of 50-70 kN/sqm, far surpassing wood's capabilities. This means aluminum can support more weight without bending or breaking.
- Repetitions: Aluminum formwork can be used for over 200 repetitions, while wooden formwork tops out at 5-8. This longevity makes aluminum a cost-effective choice in the long run.
- Durability: Aluminum is known for its strength and resistance to rust, unlike wood. This makes it a more robust and long-lasting option, withstanding the rigors of construction better.
Not only does aluminum offer superior physical properties, it also allows for easier and quicker installation and dismantling, saving time and labor costs. It's a liberating choice, freeing you from the constraints of wood's limitations.
Comparative Analysis: Steel Vs. Aluminum
Turning our gaze towards steel and aluminum formwork, we find a fascinating contrast in weight, load capacity, repetitions, and durability, with each material presenting unique advantages and limitations. Steel, weighing in between 35 to 85 kg/sqm, is notably heavier than its aluminum counterpart, which ranges from 20 to 25 kg/sqm.
However, don't be misled by this weight difference. Despite being lighter, aluminum formwork confidently handles higher loading capacities. It can withstand between 50 to 70 kN/sqm, while steel formwork can typically bear only 30 to 60 kN/sqm. Aluminum's resilience and strength are highlighted by its ability to disprove any notions that its lighter weight equates to lower endurance.
Yet, steel doesn't back down without a fight. With a lifespan extending to 100 to 120 uses, it outlasts aluminum formwork, which typically can only be used for over 200 repetitions. This increased durability of steel formwork provides a compelling argument for its use, particularly in projects demanding long-term, repeated use.
In terms of resistance, aluminum formwork takes the edge. It's more resistant to corrosion and rust, making it ideal for long-term use in harsh environments. Additionally, aluminum formwork installation and dismantling are more efficient and less labor-intensive, offering cost and time savings during construction projects.
Factors Influencing Material Selection
We've analyzed the performance characteristics of wood, steel, and aluminum formwork, and now we'll examine what factors might sway a project manager's decision when choosing between these materials. The choice isn't always clear-cut; it's a detailed decision influenced by several key aspects.
Understanding these variables can empower you to make a more informed and cost-efficient choice, liberating you from potential project setbacks. Let's explore these factors:
- Project Budget: Cost is often the main consideration. Wooden formwork offers a cost-effective solution for low-budget projects, while steel and aluminum formwork may provide long-term savings for high-budget projects through durability and reusability.
- Required Repetitions: The number of times a formwork system will be used can dictate the material choice. Steel and aluminum formworks, with their superior durability, are ideal for projects requiring multiple repetitions.
- Strength and Weight: The ability to bear loads and ease of transportation are important. Steel, known for its high load-bearing capacity, is suited for heavy-duty tasks. Meanwhile, aluminum's lightweight nature facilitates easy handling and speedy construction.
- Ease of Installation and Dismantling: This impacts labor costs and project timelines. Aluminum, being lightweight and easy to handle, can greatly expedite the construction process.
Of course, there's no one-size-fits-all solution. Therefore, we urge project managers to thoroughly evaluate these factors in conjunction with specific project needs and constraints. By doing so, we're confident that you'll make the best formwork material selection.
Frequently Asked Questions
Is Aluminium Formwork Better Than Timber Formwork?
We'd argue that aluminum formwork is indeed superior to timber. It's lighter, yet supports higher loads. It can be used over 200 times, outlasting timber's 5-8 uses. Aluminum resists rust and wear, offering greater durability.
Plus, its easy installation and fast removal save us time and labor. So, for a sustainable, efficient solution, we're backing aluminum. It's not just a choice, it's a smart investment for our future construction projects.
Is Aluminum Formwork Better Than Steel Formwork?
We believe aluminum formwork is superior to steel.
It's lighter, making it easier to manage on site. Its high load-bearing capacity allows for greater flexibility in our projects.
More resistant to corrosion, aluminum lasts longer, providing durability that's cost-effective in the long run.
Finally, it offers a better finish quality, resulting in smoother concrete surfaces.
What Is the Best Material to Use for Formwork?
We've found that aluminum is the best material for formwork. It's strong, durable, and resistant to rust. It outperforms wood because it lasts longer and is more cost-effective in the long run.
While steel is also a good choice, it can't match aluminum's efficiency and rust resistance. So, if you're looking for a long-lasting, efficient material for your formwork, we'd recommend aluminum.
Why Do We Consider Steel Formwork Is Better Than Steel Formwork?
We believe steel formwork is superior to wood.
It's stronger, supports higher loads, and is more durable. It can withstand many more uses, making it ideal for long-term projects.
Steel is also more resistant to damage and easier to install and dismantle, saving us time on site. Though it might cost more initially, its longevity makes it a cost-effective choice.
Conclusion
To sum up, we find no one-size-fits-all answer in the wood vs. steel vs. aluminum formwork debate. Each material has its strengths and limitations.
It's crucial to ponder factors like cost, durability, reusability, and adaptability to site conditions.
We'd argue for a project-specific approach, selecting the material that best matches your particular needs. Ultimately, smart formwork material selection can have a profound impact on the efficiency and success of your construction project.