Formwork for Underground Structures: Challenges and Innovations
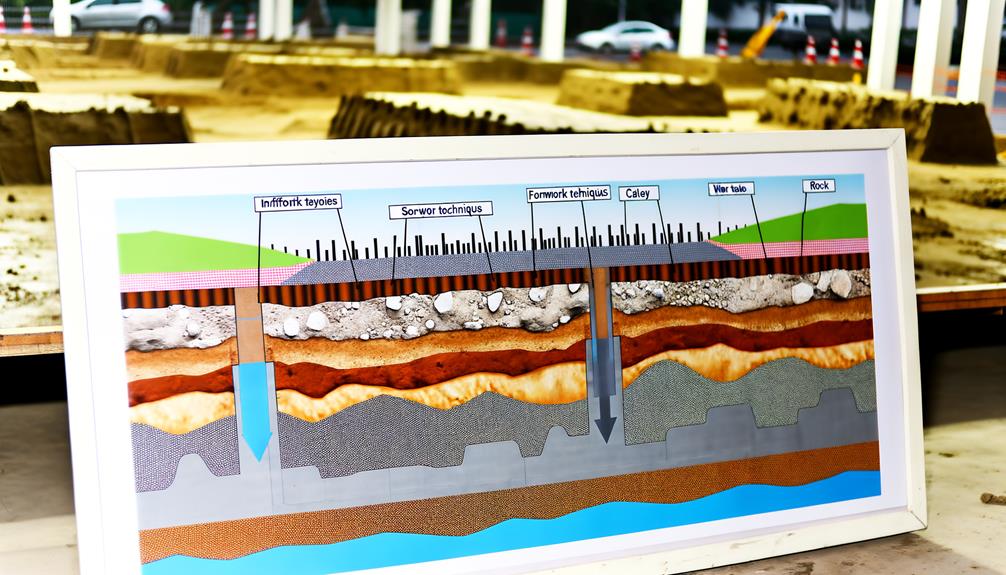
Formwork for underground structures presents unique challenges. Limited space requires innovative, compact designs and high humidity demands corrosion-resistant materials. We're seeing advanced solutions like 3D printed formwork and modular systems, ensuring precision and flexibility. Soil conditions influence support, necessitating an understanding of soil behavior. Challenges such as high water pressure are tackled with waterproof materials, robust reinforcements, and efficient drainage. We're witnessing a revolution in construction with digital formworks and reusable systems, offering cost-effectiveness and efficiency. This is just the tip of the iceberg—there's much more to explore in the domain of underground formwork innovation.
Understanding Underground Formwork Challenges
When addressing the unique challenges of underground formwork, such as limited space, high humidity, and complex geometry, it's vital that we design with precision and innovation to maintain structural integrity. The depth and intricacy of these structures require us to think outside the box, to develop formwork solutions that not only guarantee the safety and efficiency of concrete placement but also maintain structural integrity.
One significant challenge we face is the limited space. This constraint demands compact and efficient formwork design, which can be tricky to achieve while ensuring maximum safety and durability. We can't afford to compromise on these aspects, as they're crucial to the successful completion and longevity of the underground structures.
The high humidity is another hurdle. It can lead to corrosion of metal formworks, affecting their durability and reliability. As a result, we've been exploring innovative materials like plastic formworks, which aren't only lightweight but also corrosion-resistant. These innovations offer promising solutions to the humidity challenge, ensuring our formworks last longer and perform better even in the harshest of conditions.
The complex geometry of the structures we build underground adds another layer of complexity to our task. Traditional formwork methods often fall short in such scenarios. That's why we're excited about advanced technologies like 3D printed formwork. By creating customized formworks that perfectly fit our structures, we're overcoming this challenge and pushing the boundaries of what's achievable in underground construction.
Role of Soil Conditions in Formwork
In addition to the challenges we've discussed, the soil conditions play a significant role in the formwork of underground structures, greatly influencing the stability and support requirements. Different soil types like clay, sand, and rock each present unique considerations for formwork design.
To illustrate, consider the table below:
Soil Type | Formwork Consideration |
---|---|
Clay | Requires strong support due to high water content |
Sand | Needs secure bracing due to low cohesion |
Rock | Demands specialized drilling for formwork installation |
The characteristics of the soil, such as cohesion, angle of repose, and bearing capacity, must be taken into account during formwork design. These factors influence the choice of formwork materials and construction methods for underground projects. For example, clayey soil with high cohesion may require stronger support structures, while sandy soil with low cohesion may need more secure bracing.
Understanding soil behavior is critical for determining the appropriate formwork systems. This understanding guarantees structural integrity during construction and liberates us from the fear of unexpected failures. It allows us to design innovative formwork solutions that are not only safe but also cost-effective.
Addressing Limited Access Issues
Managing the challenges of restricted entry in underground construction, we've discovered that innovative formwork solutions are essential for efficient and safe processes. When underground access is limited, traditional formwork systems often fall short. It's here that the role of innovative, adaptable formwork solutions comes to the fore. Modular formwork systems, for instance, can facilitate construction in these challenging environments due to their unique flexibility and adaptability.
These systems offer a level of customization that caters to the specific needs of confined spaces. It's not just about ensuring that the construction process is efficient, but also maintaining the structural integrity of the building. Specialized formwork designs are developed with these specific challenges in mind, ensuring precise concrete placement even in areas with severely restricted access.
Yet, we're not stopping there. We're always looking for ways to push the envelope, to find better, more efficient methods of working within these constraints. That's why advanced formwork technologies, like plastic formwork, are gaining traction in the industry. Their lightweight and versatile nature allow for construction in narrow underground spaces where entry points are limited.
In essence, our efforts in the field of formwork innovation are aimed at liberating the construction process from the constraints of limited access. By providing customized solutions, we're ensuring safe and efficient construction of underground structures, regardless of the access issues posed by the project site. As we continue to innovate, we're confident that we can overcome these challenges and transform the way we approach underground construction.
Overcoming High Water Pressure
High water pressure presents another imposing challenge in underground construction, greatly impacting the stability and integrity of formwork systems. As we explore deeper underground, the pressure exerted by water increases substantially, posing a significant risk to the formwork structures we install. Hence, we must devise effective strategies to overcome this challenge and safeguard the success and safety of our projects.
To tackle high water pressure, we focus on four main strategies:
- We opt for waterproof formwork materials and seals, guaranteeing no water ingress and maintaining the structural strength of our formwork.
- We engineer formwork designs with robust reinforcement and sealing mechanisms. This approach helps our structures withstand the pressures exerted by water.
- We implement effective drainage systems and pumps to manage water levels. This reduces the impact on our formwork structures and allows us to maintain control over the underground environment.
- We conduct regular monitoring and maintenance of formwork components. This proactive approach lets us address water pressure-related issues promptly and ensures the safety and durability of our underground structures.
Innovations in Formwork Design
While we're successfully mitigating the challenges posed by high water pressure, let's also acknowledge the remarkable innovations that are redefining formwork design in our field. The use of 3D printing technology, for instance, is creating complex and precise formwork structures that were once considered unattainable. These structures are revolutionizing formwork construction for underground structures, thanks to advanced fabrication processes like material jetting and extrusion techniques.
We're now witnessing an emergence of digital formworks, characterized by their flexible and lightweight properties, enhancing efficiency and customization in our underground construction projects. These aren't merely concepts but practical, actionable innovations that are already making their mark in our field.
But it's not all about technology and digitalization. Sustainability and cost-efficiency are also driving innovation in formwork design. Reusable formwork systems, brought to life by leading innovators, are emphasizing these principles. They're offering cost-effective solutions that don't compromise on environmental responsibility, a balance that we've been endeavoring to achieve.
Our exploration into formwork design isn't confined to practical applications either. Experimental projects are pushing the boundaries of what's possible, exploring intricate patterns and textures to enhance construction methods in underground environments.
As we continue to overcome challenges, these innovations aren't just redefining formwork design, but also liberating our industry from conventional limitations. They're paving the way for a future where the underground construction is more efficient, more sustainable, and more innovative than ever before, promising an exciting future for all of us in the field.
Adjustable Modular Formwork Systems
In our pursuit of innovative construction techniques, we've embraced adjustable modular formwork systems, which provide precise customization and flexibility, revolutionizing the construction of underground structures. These systems allow for a tailored fit to match the unique dimensions of varying subterranean structures, offering an essential solution to the challenges of constructing in such environments.
Adjustable modular formwork systems offer a multitude of benefits:
- Customization: These systems permit accurate adjustments catering to the unique shapes and sizes of underground structures. It's about liberating ourselves from the constraints of traditional forms.
- Flexibility: The dynamic nature of these systems accommodates alterations in design seamlessly, enhancing our ability to adapt and innovate.
- Efficiency: The adjustable features expedite the construction process, saving valuable time and resources. It's a leap forward in our quest for speed and efficiency.
- Sustainability: By minimizing material wastage and improving construction accuracy, we're making strides towards sustainable construction practices.
We're moving away from the rigidity of traditional formwork methods, choosing instead to harness the versatility and adaptability of adjustable modular formwork systems. It's a game-changer, enhancing accuracy and efficiency while minimizing wastage. It's more than just an innovative approach; it's a revolution in the construction of underground structures, offering the liberty to customize and adapt with ease and precision. With this, we're not just building structures; we're paving the way for a more flexible, efficient, and sustainable future in construction.
Utilizing Self-Compacting Concrete Mixes
Have you ever wondered about the role of self-compacting concrete mixes in revolutionizing underground construction? We're here to shed some light on this innovative technique. These mixes aren't just designed to flow and fill formwork without the need for vibration or manual compaction – they're transforming how we approach construction in tight, hard-to-reach spaces.
Self-compacting concrete mixes are packed with high levels of fines and superplasticizers. These essential components make sure the mix has the right flow and consolidation to fill formwork neatly and efficiently.
Advantages | Component | Use in construction |
---|---|---|
Reduces labor requirements | High levels of fines | Guarantees proper flow |
Speeds up construction | Superplasticizers | Assists consolidation |
Ideal for complex formwork | Self-leveling properties | Navigate congested reinforcement |
High-quality finishes | Minimized honeycombing/voids | Improves overall construction quality |
The beauty of self-compacting concrete doesn't stop there. It's not just about reducing labor requirements and speeding up construction. It's about enabling us to tackle more intricate, complex formwork designs in confined spaces. This is particularly useful in underground structures where space can be limited.
Also, self-compacting concrete minimizes the risk of honeycombing and voids. This leads to higher-quality concrete finishes in underground projects, enhancing both the aesthetics and structural integrity of the final product.
Advanced Reinforcement Techniques in Formwork
Expanding on the robustness provided by self-compacting concrete mixes, we can further enhance the structural integrity of our underground structures with advanced reinforcement techniques in formwork. These techniques provide not only added structural strength but also innovative solutions for accelerated construction, real-time monitoring, and increased resilience against environmental factors.
To explore further into these advanced techniques, let's investigate the following:
- The utilization of high-strength materials like carbon fiber and fiberglass, which offer unparalleled structural support.
- The innovation of prefabricated reinforcement cages and grids, allowing for quicker installation and saving valuable construction time.
- The application of techniques such as post-tensioning and prestressing, increasing the load-bearing capacity of formwork structures significantly.
- The integration of smart sensors and monitoring systems, providing real-time strength and stability assessments, ensuring the safety and longevity of the structure.
Each of these methods showcases how far formwork technology has come, and how it continues to revolutionize the construction industry. They enable us to construct underground structures that aren't only stronger and more durable but also smarter.
Not only do these advanced reinforcement techniques make the formwork more robust, but they also free us from traditional constraints, giving us the opportunity to construct more daring and innovative underground structures. This is an exciting era in construction, one where technology and innovation combine to create structures of incredible resilience and integrity. In this enthusiasm lies the future of formwork, a future we're excited to embrace.
Formwork Materials and Durability
Delving into the world of formwork materials and their durability, we're seeing a notable shift towards the use of plastic formwork, particularly in the construction of underground structures. This change is driven by the superior qualities of plastic, which is lightweight, corrosion-resistant, and perfectly suited to the humid conditions typically associated with underground environments.
What sets plastic formwork apart is its resistance to moisture-induced degradation. Unlike traditional materials, plastic prevents rusting and performance changes due to moisture, ensuring the durability of the structure. This is an important advantage in underground construction, where dampness is a persistent challenge.
We're also noting the role of plastic formwork in promoting sustainability. Its recyclability aligns with today's eco-conscious ethos, offering a greener alternative to traditional formwork materials. This environmental friendliness further enhances the appeal of plastic formwork, contributing to its increasing popularity.
A higher turnover rate is another benefit we observe with plastic formwork. Its durability means it can be reused multiple times, translating to cost efficiency. The construction industry is recognizing this benefit, with plastic formwork steadily gaining traction.
Industry leaders like Suzhou TECON are at the forefront of this shift, championing the use of plastic formwork for its durability and efficiency. Their endorsement is a strong indication of the material's potential, hinting at a future where plastic formwork becomes the norm in underground construction.
Thus, the evolution of formwork materials marks a significant stride in construction technology, offering increased durability, cost-effectiveness, and sustainable solutions. As we continue exploring this field, we're excited to see where these innovations will lead us.
Future Trends in Underground Formwork
Turning our attention towards the future trends in underground formwork, we're witnessing a growing adoption of advanced systems like plastic formwork that are reshaping the landscape of underground construction projects. This shift is driven by innovations in formwork technology that aren't only overcoming the challenges of underground construction but also offering new levels of efficiency.
Plastic formwork is particularly promising. It enables a faster construction pace and addresses the limitations of traditional molds in underground structures. Companies like Suzhou TECON are at the forefront of this trend, promoting plastic formwork products to cater to the growing demand for efficient underground construction solutions.
Key future trends in underground formwork emphasize:
- Sustainability: The industry is moving towards greener, more sustainable materials that reduce environmental impact.
- Speed: Fast-track construction is becoming the norm, requiring formwork solutions that can keep up with the pace.
- Adaptability: As construction needs evolve, formwork must be flexible and adaptable to meet these changing demands.
- Innovation: There's a strong push for innovative solutions that can overcome the unique challenges of underground construction.
These trends indicate a future where underground formwork is more efficient, adaptable, and sustainable. They represent a liberation from the constraints of traditional construction methods, opening up new possibilities for underground structures. As we move forward, it's clear that the future of underground formwork is bright with promise and potential.
Frequently Asked Questions
What Are the Innovations in Formwork?
We're seeing incredible advancements in formwork. Plastic formwork solutions are enhancing efficiency, while 3D printing is allowing us to create tailor-made formworks.
We're also adopting innovative techniques for more sustainable practices. We're improving material use efficiency and exploring advanced fabrication methods. Cutting-edge processes like material jetting and extrusion are truly revolutionizing how we design and construct formworks.
It's an exciting time in our field.
What Are the Disadvantages of Tunnel Formwork?
We've noticed that tunnel formwork has some drawbacks. Its lack of adjustability to non-standard shapes complicates design and construction. This inflexibility also leads to difficulty in managing variations in tunnel alignments.
Specialized equipment and expertise are often needed, increasing costs and time. Any inaccuracies can cause structural issues and delays, adding to expenses. The rigidity of these systems limits design changes, hampering project flexibility.
What Is the Problem of Formwork?
We've found that the main problem with formwork lies in managing its complex geometry, especially in underground structures. It's a challenge to guarantee secure connections and appropriate vertical adjustments. We must fill gaps effectively for successful concrete pouring.
Additionally, we're tasked with providing safe access for workers and dealing with issues such as concrete leakage and debris accumulation. It's not easy, but we're constantly innovating to overcome these hurdles.
What Are the Applications of Tunnel Formwork?
We're using tunnel formwork extensively in different construction scenarios. It's pivotal for creating tunnels, subways, and other underground structures. It guarantees precision and efficiency in these builds, shaping the concrete during the casting process.
This formwork can handle the high pressures underground, maintaining structural integrity and safety. Innovations in this field are opening up new possibilities, making our work more effective and our structures more robust.
Conclusion
We've explored the unique challenges of underground formwork, from soil conditions to high water pressure. Innovations like self-compacting concrete mixes and advanced reinforcement techniques are changing the game, improving durability and efficiency.
As we look to the future, we're excited by the potential of new materials and designs in formwork. The scope for innovation is vast, and we're certain these advancements will propel the construction industry forward in remarkable ways.