Formwork for Circular Concrete Structures
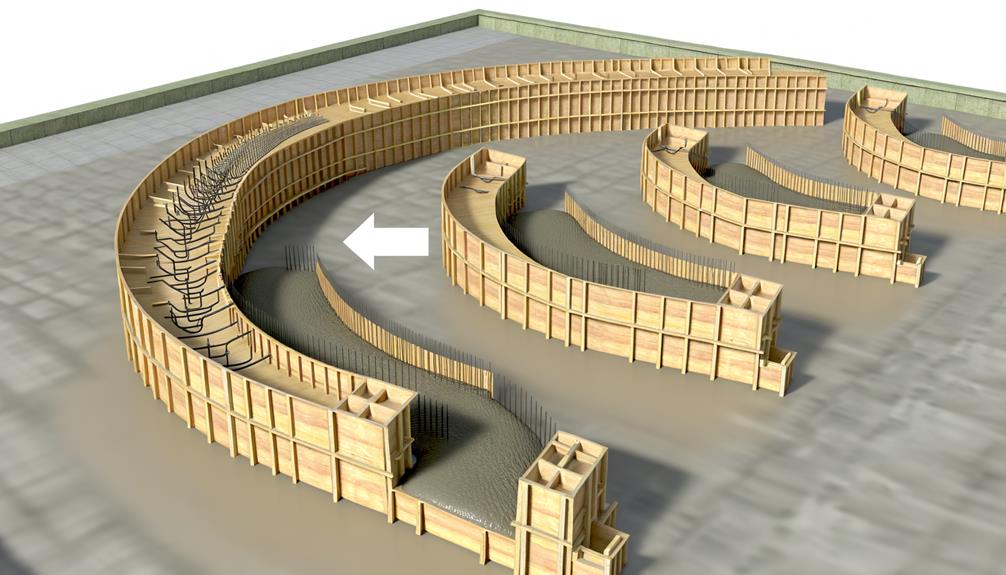
When tackling circular concrete structures, we turn to specialized formwork systems like MEVA's Radius or Circo. They are adjustable and adaptive, giving us the structural integrity and accuracy we need. It's essential to choose the right formwork, as it directly impacts the project's timeline, quality, and overall cost. Systems like these, coupled with expert guidance, can dramatically minimize project duration and labor. What's more, they often result in superior-quality surfaces important for both architectural and infrastructure projects. However, there's much more to learn and understand about this versatile process. Dig deeper, and we promise you won't be disappointed.
Understanding Circular Concrete Structures
Diving straight into the core of circular concrete structures, it's crucial to grasp that these extraordinary architectural wonders necessitate the use of specialized formwork to uphold their curved shape throughout the building process. These aren't just your average flat walls but a variety of structures including curved walls, circular columns, and other distinctive architectural features.
To craft these circular structures, formwork systems must be more than just supportive; they must be adaptable, adjustable, and capable of producing high-quality concrete finishes. The curvature of the structure calls for a formwork system that can adjust to its shape while preserving the structural integrity of the concrete. It's not only about holding the concrete in position; it's about molding it, directing it, and ensuring it solidifies into the precise form that the architect envisioned.
Circular formwork systems like MEVA's Radius and Circo are at the forefront of providing effective solutions for curved walls and columns. They aren't just tools, but the catalysts that enable the potential of concrete to take on shapes that challenge traditional architectural standards.
However, it's not just the system itself that's crucial. The design and materials of the formwork play a critical role in achieving the desired curvature and structural integrity in circular concrete constructions. Accuracy is paramount here; even the smallest deviation can change the final form of the structure.
Importance of Formwork Selection
In the domain of circular concrete construction, the choice of the appropriate formwork isn't just a decision, but a vital factor that can guide the course of the entire project, greatly influencing execution timelines and the overall quality of the structure. It's not an exaggeration to say that the selection of formwork can make or break a project.
Formwork selection is pivotal in producing curved or circular concrete structures with superior-quality surfaces, essential in both architectural and infrastructure projects. Whether we're dealing with the construction of circular columns for bridges, buildings, or piling applications, the right formwork is the key to creating structures that not only meet design specifications but also stand the test of time.
The beauty of circular formwork systems such as those offered by MEVA lies in their versatility and adaptability. Systems like Radius and Circo provide the means to shape concrete structures with high-quality finishes, melding form with function in a way that enhances the aesthetic appeal of the structure while ensuring its durability and strength.
Selecting the appropriate formwork isn't just about aesthetics and quality, though. It's also about efficiency. The right formwork system can minimize project duration, costs, and labor, leading to a more streamlined and efficient construction process. This is why we can't afford to underestimate the importance of expert guidance in formwork selection. MEVA, for instance, provides such guidance, helping us navigate the intricacies of unique construction needs.
In short, formwork selection is a critical step in circular concrete construction, one that demands careful consideration and expert guidance.
Features of RUNDFLEX Wall Formwork
Shifting our focus to specific formwork systems, let's examine the features of RUNDFLEX Wall Formwork, renowned for its versatility and efficiency in circular concrete construction. This system stands out due to its pre-assembled units, which come equipped with a BFD Alignment Coupler, dramatically reducing installation effort and time. We can't overlook the system's flexibility, which allows for the adjustment of wall internal radii of 1.00 m and larger. This feature proves particularly advantageous in projects demanding versatility.
An intrinsic simplicity in the adjustment procedure further enhances the system's efficiency. By using templates and spindles, quick and efficient adjustments are possible, thereby accelerating construction schedules. This simple, yet innovative approach, ensures that we can meet various project demands without compromising on construction speed or accuracy.
The adaptability of RUNDFLEX Wall Formwork is another feature worth highlighting. Its design allows for seamless integration into various project requirements, promoting an efficient workflow. It's this adaptability that notably improves construction speed and accuracy, leading to more precise and reliable outcomes.
Furthermore, RUNDFLEX Wall Formwork complies with industry standards, ensuring that the end result isn't only structurally sound but also meets the rigorous requirements of the construction industry. This compliance gives us confidence in the integrity of the structures we build using this system.
ORBIS Formwork: Pros and Cons
Diving into the world of ORBIS formwork, we discover a system that brilliantly caters to the construction of curved structures like water reservoirs and fermentation plants, balancing functionality with the pleasing aesthetics of tie-point free design. The formwork's design facilitates the creation of complex geometries with ease and precision, allowing for a streamlined construction process.
The ORBIS system integrates well with MRM climbing brackets and similar systems, further refining the construction process. This integration not only speeds up the building process but also guarantees the creation of durable and reliable structures. Additionally, the lack of tie points enhances the aesthetics of the finished concrete structures, providing an unblemished and smooth finish.
However, it's not all sunshine and roses with ORBIS formwork. While the system offers a tailored construction process, it also demands a higher level of expertise and precision from construction workers. The unique design of the ORBIS system, while innovative and practical, requires skilled hands for its implementation.
Additionally, the cost associated with the ORBIS system can be a deterrent for some. Its unique design and the high-quality materials used in its construction can make it a pricier option compared to other formwork systems.
Bira Formwork: A Comprehensive Review
Frequently hailed for its precision and efficiency, Bira Formwork offers a unique construction solution, combining tight joints in height to minimize grout loss with a simple radiusing mechanism for easy panel adjustment. This approach guarantees precise construction without the need for complex sequencing. We've found this to be a liberating feature for many of our clients, freeing them from the constraints often associated with traditional formwork systems.
Bira Formwork is also praised for its strength and durability. With a permissible concrete pressure of 60-80 kN/m2, it boasts high-strength steel shuttering faces for architectural F4 finishes. This robustness, combined with the system's ability to achieve a 1850 Outer Radius for columns from 750mm to 1200mm without ties, ensures an efficient and safe construction process.
For an analytical look at Bira Formwork, let's examine a simple two-column, three-row table:
Feature | Advantage |
---|---|
Tight joints in height | Minimizes grout loss, ensuring precise construction |
Radiusing mechanism | Allows for easy adjustment of panels without complex sequencing |
High-strength steel shuttering faces | Provides architectural F4 finishes |
Each Bira Formwork panel weighs 438 Kilos. They can be easily lifted and stacked, featuring aligning wedges and feet for easy adjustment on various ground conditions. This innovative design fosters a detailed and efficient construction process, further highlighting the liberating potential of Bira Formwork. To sum up, Bira Formwork's precision, strength, and adaptability make it an excellent choice for constructing circular concrete structures.
Achieving Various Curvature Radii
In our investigation of circular concrete formwork, it's crucial to grasp how different systems handle curvature radii, a key factor in creating smooth, curved walls and intricate geometries. Formwork systems like MEVA's Radius system, for example, can achieve a minimum curvature radius of 3.50m. This level of precision not only facilitates the creation of complex structures but also enhances aesthetic appeal.
In the domain of flexibility, the RUNDFLEX Circular Wall Formwork stands out. Its unique design offers variable adjustment for wall internal radii of 1.00m and larger. This capability frees us from the constraints of fixed radii, allowing us to craft concrete forms that reflect our vision without sacrificing structural integrity.
Meanwhile, the Bira Circular Formwork achieves a minimum radius of 2.2m. Besides this precision, Bira's system also offers remarkable efficiencies. With minimal nuts to turn per panel and efficient lifting mechanisms, it simplifies the radiusing process and speeds up construction.
As we push the boundaries of formwork, the ORBIS Circular Formwork system catches our attention. It facilitates the construction of diverse geometries, including columns with outer radii from 750mm to 1200mm without the need for ties. This versatility empowers us to explore new design possibilities.
Case Study: Municipal Water Reservoir
Let's turn our attention to a practical application of circular formwork systems, specifically the construction of a 28m diameter municipal water reservoir in Lasa. The scope of this project was vast, involving the formation of 8m high concrete walls meticulously constructed in three distinct concreting sections. The construction process was streamlined, thanks to a segmented approach that amplified efficiency while guaranteeing the highest quality of workmanship.
We chose to employ ORBIS circular formwork systems, which proved invaluable in delivering a precise and smooth construction process. Every segment of the reservoir's walls was crafted with meticulous attention to detail, allowing for seamless integration with the next. The result was a robust, sturdy structure that stood as a proof of the prowess of circular formwork systems.
Let's not overlook the reservoir's ceiling, an engineering marvel in itself. This was formed using ALUSTERN ceiling formwork, chosen for its proven durability and adaptability. Its use ensured a steady, reliable upper structure, effectively capping off the reservoir and providing a secure, leak-free environment for water storage.
In this case study, we've explored the application of circular formwork systems in a real-world scenario, shedding light on their immense potential in large-scale construction projects. Through strategic planning, meticulous execution, and the adoption of innovative construction techniques, we've demonstrated how circular formwork systems can revolutionize the construction of municipal water reservoirs. This isn't just about building structures; it's about liberating our approach to construction, breaking away from traditional constraints, and embracing the possibilities of the future.
Case Study: Fermentation Plant Construction
Expanding on our examination of circular formwork systems, we now shift our focus to another impressive project – the construction of a fermentation plant in Bari. This project, like many others, posed its own unique challenges, but through innovative solutions and careful planning, the team was able to successfully incorporate the use of ORBIS circular formwork and MRM climbing brackets.
The formwork systems chosen for the project weren't selected at random. Rather, they were chosen for their adaptability and their ability to facilitate the construction of curved structures. This enhanced the efficiency of the project and ensured that the new fermentation plant met all project requirements effectively.
The ORBIS circular formwork system was particularly effective in this case. Its design allowed for a high degree of accuracy while also improving the speed of the construction process. Paired with the MRM climbing brackets, it demonstrated compatibility and reliability in the face of demanding construction conditions.
We've seen the positive impact of tailored formwork solutions firsthand in the construction of the Bari fermentation plant. The adaptability and efficiency of these systems, including ORBIS circular formwork and MRM climbing brackets, have proven to be essential tools in the construction industry.
As we further explore the study of circular formwork systems, the construction of the Bari fermentation plant stands as a proof of the possibilities of this technology. It's a shining example of how innovative solutions, when combined with detailed planning and analysis, can meet and even exceed project requirements.
Efficiency in Assembly and Lifting
How can we enhance efficiency in the assembly and lifting phase of formwork construction? The answer lies in leveraging the features of the Bira Circular Formwork system. Bira's design is a game-changer, minimizing rubbing and grout loss during assembly with its tight joints. We can exploit this feature to drive efficiency, as less grout loss translates to less time and resources spent on replenishing it.
The simple radiusing in Bira panels is another tool in our efficiency arsenal. It requires the turning of only four nuts per panel, and the best part is there's no need for sequencing. This cuts down assembly time significantly, allowing us to move to the pouring phase faster.
Lifting the formwork is often a time-consuming process, but not with Bira. Its easy lifting feature ensures that we can lift as needed in one piece. This reduces time from pour to pour, keeping our construction schedule on track. The weight of the Bira panels, 438 kilos each, is ideal for easy lifting and stacking in twos. It's not just about lifting, though. The aligning wedges designed into the system prevent grout loss, enhancing our efficiency even more.
Creating High-Quality Concrete Finishes
Achieving the gold standard in concrete finishes is within our grasp, thanks to precision formwork systems like the MEVA Radius Circular Formwork. This sophisticated tool allows us to create stunning, high-quality finishes on circular structures, enhancing their aesthetic appeal and functional integrity.
However, the MEVA Radius isn't the only tool in our arsenal. A variety of other specialized formwork systems are also instrumental in our quest for perfection. Let's explore a few of these:
- *MEVA Circo steel formwork*: This system guarantees fair-faced finishes on circular columns, providing a visually pleasing result that complements the overall structure.
- *RUNDFLEX Circular Wall Formwork*: With efficient adjustment procedures for wall radii of 1.00m and larger, it ensures precise finishes that adhere to the most exacting standards.
- *Bira Formwork's steel face panels*: These enable us to achieve an architectural F4 finish without panel lip joints, thereby enhancing the visual appeal of concrete surfaces.
- *ORBIS Circular Formwork*: This system's design, which lacks tie points, allows for smooth construction of circular structures, resulting in high-quality finishes.
Each of these systems presents a unique approach to creating high-quality concrete finishes. When we combine them with our expertise and dedication, we're able to achieve a level of precision and beauty in our work that truly sets us apart.
In our quest for liberation, we must remember that it's not just about constructing structures. It's also about creating art. And with these tools, we can paint a masterpiece with concrete.
Frequently Asked Questions
What Formwork Is Used for Circular Concrete Columns?
We use steel or aluminum formwork to shape circular concrete columns. It's adjustable, making it suitable for projects of various scales. This formwork is especially important for infrastructure projects like bridges and buildings. It provides the support needed to pour and shape the concrete.
Choosing the right formwork is essential for success. We're not just building structures, we're shaping the future.
What Size Is Circular Column Formwork?
We're often asked, 'What size is circular column formwork?'
It's important to understand that the size isn't one-size-fits-all. In fact, it's highly adjustable to fit columns of varying diameters.
The customization ranges from small to large diameters, offering great flexibility in construction. This adaptability guarantees precise and structurally sound concrete columns, regardless of their size.
As a result, the size of circular column formwork is determined by the specific requirements of each project.
How Is the Concrete and Formwork Measured for Circular Columns?
We measure the concrete for circular columns in cubic meters, factoring in the column's diameter and height.
On the other hand, we calculate formwork in square meters, considering the surface area needed to shape the column.
It's crucial to accurately measure both to guarantee we construct columns with precise dimensions.
It's a vital step in our process, ensuring efficiency and quality in our construction projects.
What Are the Different Types of Formwork?
We've got several types of formwork to discuss.
Traditional timber formwork is commonly used, it's versatile but labor-intensive.
Engineered Formwork Systems, often made of prefabricated modules, are reusable and offer speed and precision.
Re-usable plastic formwork is ideal for repetitive work, while permanent insulated formwork improves thermal insulation.
Finally, we've flexible formwork, a recent innovation that lets us create complex shapes with ease.
Each offers unique benefits, so it's about picking the right one for the job.
Conclusion
In wrapping up, we've found that formwork for circular concrete structures is undeniably essential. With options from RUNDFLEX to ORBIS and Bira, choosing wisely can greatly impact efficiency and outcome.
Our case studies showed how the right formwork can streamline projects like reservoirs and fermentation plants. It's clear: strategic formwork selection not only simplifies assembly and lifting but also results in superior concrete finishes.
Here's to transforming the construction landscape with smart formwork solutions!