Formwork Design Essentials for Construction Projects
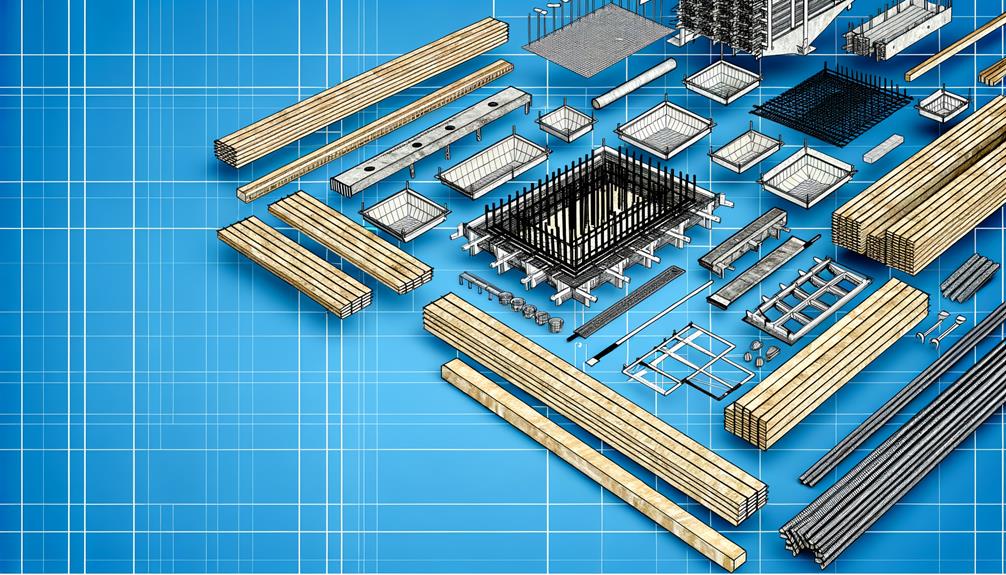
Formwork design dictates the success of construction projects. We prioritize understanding formwork basics, from traditional and modern materials to proper removal times. Our innovative design approach includes certifying formwork drawings, selecting effective materials, and adhering to construction codes. We meticulously design column and wall forms, strategize formwork frame erection, and guarantee safety on formwork decks. Curious about our techniques for suspended slabs or MEVA formwork system utilization? Stick around to find out more about our custom designs and the importance of quality assurance in formwork selection. You'll be amazed at what a well-designed formwork can achieve.
Understanding Formwork Basics
Delving into the basics of formwork, we comprehend it as a vital mold used in concrete construction, with its primary function being to shape structures like walls, columns, and slabs. It's an essential component in the building process, and its effective use can greatly impact the quality and safety of a construction project.
Traditionally, timber, steel, and plywood have been the mainstay materials for formwork. However, modern construction's innovative spirit has led to the introduction of aluminum and plastic alternatives. These cutting-edge materials offer benefits such as increased durability, lighter weight, and easier manipulation, while still maintaining the necessary sturdiness for concrete shaping.
Understanding the appropriate time for formwork removal is equally critical. We've found that it's generally best to remove the formwork after the concrete reaches a strength of around 5 N/mm2. This precaution helps prevent any potential damage to the newly shaped structures, securing the integrity of the build.
Formwork must fulfill a set of essential criteria to be deemed effective. It needs to be stable, leak-proof, and accurate in its function. In addition, it must rest on a secure base. These elements safeguard the quality and safety of the project, preventing any potential mishaps.
In essence, we've found that understanding the basics of formwork is akin to mastering the fundamentals of building construction. It's a gateway to better, safer, and more efficient construction practices. Armed with this knowledge, we're better equipped to navigate the complex world of construction, facilitating our quest for liberation in this dynamic field.
Importance of Formwork Design
Turning our attention to formwork design, it's evident that it plays a pivotal role in ensuring our construction projects aren't only safe and economical, but also structurally sound. This is because a well-executed formwork design serves as the backbone for our creations, influencing the concrete structures that meet both architectural and engineering requirements.
The significance of formwork design can't be overstated. It's a vital factor that supports various loads, provides safe working conditions, and allows for easy removal without damaging the concrete – a trifecta of features that contributes to the overall efficiency of our projects.
We also can't forget the importance of certified formwork drawings. These essential documents are our safety net, ensuring that we comply with industry standards and regulations. They offer a visual guide that helps us avoid potential pitfalls and costly errors, while also providing a reliable roadmap towards successful project completion.
But where does innovation come into play, you ask? Well, formwork design isn't just about following standards and ticking boxes. It's also about being creative and flexible, adapting to the unique challenges each project presents. We need to analyze and consider factors like material selection, structural stability, and adherence to relevant codes and guidelines.
Selecting Suitable Formwork Materials
When it comes to selecting suitable formwork materials, we've got a plethora of options, each with its own unique blend of strength, durability, cost-effectiveness, and project suitability. Aluminum formwork, for instance, stands out for its strength and durability, not to mention its lightweight properties which make it a popular choice for construction projects.
Steel formwork, conversely, is a demonstration of cost-effectiveness. This material is especially suitable for symmetrical structures, despite having less concrete adhesion compared to others. Nevertheless, its durability is something we can't downplay.
Plastic formwork won't weigh down your budget, and its lightweight nature makes it apt for smaller projects. It also excels in reducing fresh concrete pressure during construction, a characteristic that can't be overlooked. However, let's be honest here, it may not be the best option for larger, more demanding projects.
Then there's timber formwork. Its flexibility and inexpensive nature can be tempting, but we need to be cautious of its susceptibility to termite damage and shorter lifespan. It's a good option, but perhaps for those projects where long-term durability isn't a primary concern.
Finally, we circle back to aluminum and steel formworks. Yes, they're pricier initially, but they're champions of the long game. Their reusability, durability, and efficiency in construction are bound to provide long-term savings.
In the end, it's about balancing the strengths and drawbacks of each material. We've got to take into account project needs, budget constraints, and durability demands, and then make an informed, liberating choice. The key is to choose wisely, without compromising the quality and efficiency of the project.
Types of Formwork in Construction
Delving into the world of formwork types, it's evident that the construction industry offers a variety, each with its unique composition and usage, ranging from traditional systems built on-site using timber or plywood, to modular ones created off-site from materials like hardboard, plastics, steel or aluminum.
Traditional formwork systems allow for flexibility in design and can be tailored to suit unique structural requirements. However, they are labor-intensive and slow to construct. On the other hand, modular systems offer the advantage of quick assembly and light weight but require careful bracing during installation to prevent instability and guarantee safety on-site.
To illustrate, let's present a comparison of these two formwork types.
Traditional Formwork | Modular Formwork | |
---|---|---|
Material | Timber or Plywood | Hardboard, Plastics, Steel or Aluminum |
Construction | Built On-Site | Created Off-Site |
Pros & Cons | Flexible design but labor-intensive | Quick assembly but needs careful bracing |
Detailed formwork drawings are critical for both types. They must provide precise details of joints, ties, and framing to ensure accurate construction and compliance with standards.
Furthermore, we can't stress enough the importance of certified formwork designs in guaranteeing structural integrity, safety, and adherence to legal requirements in construction projects. These certifications not only allow for peace of mind but also ensure that the construction project can withstand the test of time.
Designing Wall and Column Forms
In designing wall and column forms, we must skillfully consider a multitude of factors ranging from concrete pressure and formwork material stiffness, to tie spacing and lateral support, all crucial in ensuring safety, stability, and efficiency in construction projects.
Wall formwork designs, for instance, demand a keen understanding of the interplay between concrete pressure and material stiffness. Whether we're dealing with conventional, girder, frame, crane-independent, or crane-dependent systems, we ought to tailor our designs to the unique needs of each project.
Column formwork designs, on the other hand, require a different set of considerations. We need to optimize formwork thickness and tie spacing without compromising safety and stability. We're also fans of the intelligent design features in systems like MEVA's column formwork. These offer easy handling and built-in safety mechanisms, freeing us from unnecessary complications.
It's also worth noting that slab formwork techniques like conventional, modular, and drop-head-beam-panel methods offer flexibility and efficiency in slab construction. These techniques, however, will be covered in more detail in a future discussion.
In a nutshell, the science of designing wall and column forms is a careful balancing act. We're constantly innovating and analyzing, pushing the boundaries of what's possible while staying firmly grounded in the principles of safety and efficiency. It's a complex process, but it's also incredibly rewarding. As we discover new solutions, we're not just building structures, we're shaping the future of construction. And that's a responsibility we take very seriously.
Erecting Formwork Frames Procedure
Progressing further, let's explore the intricacies of setting up formwork frames, a process that demands meticulous planning and execution to guarantee the highest level of stability and safety during construction. We erect formwork frames progressively, each step building on the last, to make certain that the structure remains firm. As we erect, we promptly attach braces to the formwork frames. These braces serve as safeguards, preventing any tipping or collapse that may occur due to uneven weight distribution or external forces.
Beyond the physical structure, we also consider the movement of people and equipment around the site. We designate specific access ways to facilitate safe and efficient movement. By doing so, we reduce the likelihood of accidents resulting from collisions or missteps.
As we increase the height of the formwork frames, maintaining lateral stability becomes essential. Without proper balance, the formwork may lean or tilt, causing a potential safety hazard. We take measures to make sure that the structure remains upright and stable as it grows taller.
In addition to the frames themselves, we also pay close attention to the decking of each lift of formwork. A fully decked formwork enhances safety measures by controlling internal falls. It acts as a barrier, preventing workers or materials from falling inside the formwork.
Suspended Slabs Formwork Systems
Exploring the intricacies of suspended slab formwork systems, we discover that these structures, which support concrete slabs without direct ground contact, require a complex blend of props, beams, and formwork panels to guarantee safe and efficient construction. These systems ingeniously eliminate the need for an underlying earth base, allowing for the construction of various structures, including multi-story buildings, bridges, and tunnels.
To fully grasp the mechanics of these systems, let's delve into the primary components:
- *Props:* These provide vertical support, essentially acting as the backbone of the system. Their strength and stability are vital in maintaining the integrity of the overall structure.
- *Beams:* These elements transfer loads to the vertical supports. Their design must ensure that they can adequately bear the weight of the concrete and additional loads during construction.
- *Formwork Panels:* These create the mold for the concrete slab, dictating its shape and finish. The quality of the formwork panel directly impacts the aesthetics and durability of the final concrete structure.
- *Loading:* The system must be designed to withstand the weight of wet concrete, construction materials, and workers. Overlooking this factor can result in catastrophic failures.
- *Structural Integrity:* The system must maintain its stability under various conditions. This involves careful design, considering factors like wind loads and seismic activity.
Each component plays its part in the symphony of construction, working harmoniously to create structures that stand the test of time. Understanding these systems liberates us from traditional ground-dependent construction methods, pushing the boundaries of what we can build. As we continue to innovate and refine these systems, we aren't just constructing buildings, but also paving the way for future architectural wonders.
Ensuring Safety on the Formwork Deck
Shifting our attention to the formwork deck, we find that ensuring safety here is paramount to prevent falls, injuries, and accidents during the construction process. The deck is a bustling hub of activity, necessitating several safety measures to safeguard the workforce. We aren't just discussing standard safety goggles and helmets here; we explore a detailed safety strategy that encompasses more.
The installation of guardrails, toe boards, and safety nets can't be overlooked. These elements act as the first line of defense against falls, providing a physical barrier between the workers and the edges of the deck. But it's not just about installing them; it's about ensuring they're sturdy, well-maintained, and rightly positioned.
Regular inspections are also key. We're talking about meticulous checks for stability and integrity. Any sign of structural weakness could lead to catastrophic failures, so we advocate for frequent, thorough inspections. This isn't a one-and-done deal; it's an ongoing commitment to safety.
Training plays a significant role in safety as well. We believe in empowering workers with knowledge and skills to use the equipment properly and to recognize potential hazards. This includes detailed training on formwork safety procedures that are tailored to the specifics of the deck.
Lastly, the implementation of strict safety protocols and guidelines is a must. We're advocating for a culture of safety that minimizes risks and promotes a secure working environment. Inculcating this culture requires clear communication, consistent enforcement, and a company-wide commitment to safety. It's not just about ticking boxes; it's about ensuring everyone returns home safely at the end of the day.
Process of Formwork System Removal
Diving into the process of formwork system removal, we find that it's a critical operation that hinges upon the concrete reaching a strength of 5 N/mm2, guaranteeing the structure remains unscathed during dismantling. It's a dance of precision and timeliness, where the smallest misstep can lead to damaging consequences.
During the disassembly process, we must tread lightly to prevent structural damage to the concrete elements. This requires a careful, thorough approach. We can't simply yank away the formwork. It needs to be gently eased out, one piece at a time.
Here's a brief overview of the essential steps involved:
- Verification of concrete strength: The concrete must reach a strength of 5 N/mm2 before any dismantling begins.
- Individual piece removal: Each piece of the formwork system is taken out one by one.
- Caution against early striking: Striking formwork too soon can lead to deformation or cracking. Patience is key.
- Planning and coordination: Proper planning guarantees safety and efficiency during the removal process.
- Consideration of aesthetics: The removal timing is critical to maintain the integrity and aesthetics of the concrete surface.
The process of formwork system removal isn't just about getting rid of the old to make way for the new. It's a meticulous procedure that requires a keen eye for detail, a steady hand, and a thorough understanding of the materials at play. It's about achieving liberation from the old while ensuring the new is left untouched, pristine, and ready for what's next.
Incorporating Slab Formwork Techniques
As we transition from formwork removal, it's crucial to explore the world of slab formwork techniques, which provide a blend of flexibility, efficiency, and adaptability in construction projects. Traditional slab formwork includes the use of stringers and joists, which offer flexibility in layout design. This method allows for customization, making it ideal for construction projects with unique design requirements. It's a demonstration of the adaptability inherent in construction design.
Furthermore, modern slab formwork techniques have evolved to offer even more efficiency. For example, modular slab formwork elegantly integrates panels with beams and props for quick assembly. This method significantly reduces the time needed to set up the formwork, thereby increasing the speed of construction. It's a clear example of innovation working hand in hand with practicality.
Various slab formwork methods exist to further enhance efficiency. Techniques such as drop-head-beam-panel and primary-and-secondary-beam methods have been developed to allow for efficient stripping and reuse. These techniques focus on the swift completion of projects, easy stripping of forms, and adaptability to different slab layouts. It's a clear nod to the necessity of speed and adaptability in today's fast-paced construction environment.
Utilizing MEVA Formwork Systems
Delving into MEVA formwork systems, we find intelligent, safety-focused solutions that bring stability, reliability, and quality to construction projects. These systems, designed with the user experience at the forefront, prioritize safety and efficiency without sacrificing the robustness required in the construction industry.
Now, to paint a clearer picture of the relevance of MEVA formwork systems, consider the following:
- *Safety*: MEVA systems provide enhanced safety features, minimizing risks on the construction site.
- *User-friendliness*: The design is intuitive, reducing the learning curve for construction teams.
- *Global support*: MEVA offers thorough support, ensuring construction teams have access to expert advice and assistance when required.
- *Efficiency*: These systems are designed for quick assembly and disassembly, saving valuable time on-site.
- *Tailored solutions*: MEVA can offer specialized formwork solutions to fit unique project requirements.
The selection of MEVA formwork systems should be driven by a few key considerations. One should look at the durability of the system, its design efficiency, and the level of support offered. These factors play an important role in ensuring project success, by providing a reliable, efficient, and robust formwork solution.
Customizing Formwork Designs
Moving on from MEVA systems, let's explore how customizing formwork designs can provide a tailored solution that enhances efficiency, safety, and cost-effectiveness in construction projects. By customizing, we mean adjusting the formwork system to fit the project's specific requirements, which may include altering dimensions, materials, and support elements to meet structural and architectural needs.
Through customization, we're not just building formworks; we're engineering solutions. By optimizing the formwork system for the project's unique characteristics, we streamline the construction process. Time is saved in assembly and disassembly, material waste is reduced, and the speed of construction is enhanced. But it's not just about efficiency, it's also about quality and safety.
Customized formwork designs guarantee proper support for complex shapes, sizes, and loads. By tailoring the formwork to the project's specifications, we create a safer work environment. The risk of formwork failure or collapse, which can lead to serious accidents, is greatly reduced.
Additionally, custom formworks also contribute to cost-effectiveness. Although the upfront cost may be higher, the long-term savings from reduced labor, faster project completion, and less waste make it a worthwhile investment. It's a classic case of spending a bit more now to save a lot later.
Ensuring Quality in Formwork Selection
Prioritizing quality in formwork selection is essential to make sure we're selecting solutions that offer durability, design efficiency, and most importantly, safety in our construction projects. It's not just about choosing the most expensive or the most advanced product on the market; it's about finding a balance between cost-effectiveness, functionality, and reliability.
When we think about quality in formwork selection, we focus on:
- Durability: The formwork must withstand the rigors of the construction process, from assembly to disassembly.
- Design Efficiency: Good formwork solutions are designed to streamline the construction process, simplifying installation and removal.
- Safety: High-quality formwork provides a solid and secure structure, reducing the risk of accidents and improving overall site safety.
- User-friendliness: The formwork should be easy to handle, reducing the time and effort needed for assembly and disassembly.
- Comprehensive Support: Quality formwork suppliers provide extensive support, from delivery and installation to maintenance and removal.
Choosing the right formwork is an investment in the success of our construction project. The right selection can lead to increased efficiency, reduced risks, and a final product that meets our exact specifications. It's about liberation – freeing ourselves from unnecessary complications, potential hazards, and inefficiencies. It's about taking control of our project, making informed decisions, and ensuring the end product aligns with our vision. As a result, we must pay attention to quality in formwork selection, ensuring it meets our project's unique needs and contributes towards a successful construction process.
Frequently Asked Questions
What Are the Essentials of Formwork?
We believe the essentials of formwork are rigidity, watertightness, and easy removability without damaging the concrete. It's important to take into account loads, concrete properties, and material stiffness.
Detailed blueprints, including joints, ties, and framing, guarantee compliance with laws and standards. We can't overlook maximum bending moments, shear forces, and deflection.
What Are Requirements of Formwork?
We're required to design formwork that accurately fits the desired size, shape, and finish of our concrete structures. It's imperative that it supports all loads without collapse.
We take worker and concrete safety seriously in our designs. Our assessments consider vertical and lateral loads, concrete properties, and formwork material stiffness. We also account for reinforcement details and compaction methods.
It's a complex process, but essential for successful construction.
What Are the Main Requirements for Designing Formwork?
We're focused on designing formwork that's rigid, watertight, and can be easily removed without causing damage. Our drawings comply with all laws and standards, detailing joint, tie, and framing information.
We're committed to consulting with seasoned designers to address health and safety risks. Our top priority is supporting all loads without collapse, ensuring the safety of our team and the integrity of the structure.
We're dedicated to smart, safe, and efficient formwork solutions.
What Are the Principles of Formwork Design?
We're concentrating on the principles of formwork design. It's not just about structure stability, but also ensuring worker safety and wet concrete protection. We must create rigid, watertight forms that can be easily removed without damaging the concrete.
Proper assessment of loads and concrete properties, along with material stiffness, is crucial. Additionally, we can't ignore the importance of reinforcement details and compaction methods. It's a detailed, innovative, and analytical process.
Conclusion
In sum, we've acknowledged that formwork design is essential in any construction project.
Choosing the right materials and types of formwork, and incorporating slab or MEVA systems, are all vital steps.
By customizing designs and ensuring quality selection, we can create efficient, sturdy structures.
Understanding these essentials not only strengthens our projects but also promotes innovative construction practices.
Keep these insights in mind as they can greatly shape our construction endeavors.